
УМК МАХП - 2 ч. Жаркова, Митинов
.pdfТаблица 6
Исходные данные для расчета
№ |
D |
L |
Ф |
n |
i |
Марка |
ρ |
Плн |
Плк |
|
варианта |
каучука |
|||||||||
|
|
|
|
|
|
|
|
|||
|
|
|
|
|
|
|
|
|
|
|
1 |
0,60 |
2,0 |
1,20 |
20 |
1,6 |
СКН-40 |
986 |
0,05 |
0,25 |
|
2 |
0,66 |
2,1 |
1,30 |
15 |
2,0 |
СКН-40 |
986 |
0,10 |
0,40 |
|
3 |
0,66 |
2,1 |
1,30 |
20 |
1,5 |
СКН-40 |
986 |
0,15 |
0,45 |
|
4 |
0,60 |
1,8 |
1,20 |
20 |
1,2 |
СКН-40 |
986 |
0,10 |
0,30 |
|
5 |
0,60 |
2,1 |
1,20 |
18 |
2,0 |
СКН-26 |
950 |
0,05 |
0,30 |
|
6 |
0,66 |
2,1 |
1,25 |
20 |
1,5 |
СКН-26 |
950 |
0,10 |
0,40 |
|
7 |
0,60 |
2,0 |
1,22 |
18 |
2,0 |
СКН-26 |
950 |
0,15 |
0,40 |
|
8 |
0,60 |
2,0 |
1,30 |
20 |
1,5 |
СКС-30 |
970 |
0,10 |
0,35 |
|
9 |
0,50 |
1,6 |
1,20 |
25 |
2,0 |
СКС-30 |
970 |
0,05 |
0,30 |
|
10 |
0,66 |
2,1 |
1,20 |
22 |
1,5 |
СКС-30 |
970 |
0,10 |
0,48 |
ЧЕРВЯЧНЫЕ МАШИНЫ
Наиболее широкое применение червячные машины получили в про- цессах переработки пластических масс и резиновых смесей, где они ис- пользуются для проведения различных технологических операций (экстру- зии, смешения, гранулирования и т.д.).
Помимо самостоятельного применения червячные узлы входят в со- став экструзионно-выдувных и литьевых машин.
Независимо от технологического назначения любая червячная ма- шина (рис. 6) состоит из цилиндра 4, имеющего каналы 5 для подачи хла- дагента (жидкость, воздух), электронагревателей 6 для позонного регули- рования температуры цилиндра, одного или двух червяков 3, головки для формирования профиля выдавливаемого материала 1, загрузочной воронки с бункером 7 и привода 8. Между головкой и концом цилиндра могут ус- танавливаться сетки, дроссельные решетки 2 и т.д.
Перерабатываемый материал в виде гранул, порошка или ленты по- ступает в машину через загрузочную воронку и по мере продвижения вдоль цилиндра уплотняется, переходит в вязкопластическое состояние под воздействием температуры и сдвиговых деформаций в канале червяка
ивыдавливается через формующую головку.
Всоответствии с претерпеваемыми физическими превращениями материала в червячной машине принято различать три зоны по длине ци- линдра: зону загрузки l1 , где материал находится в твердом состоянии; зо-
ну плавления (сжатия) l2 , в конце которой материал переходит в вязкопла-
231
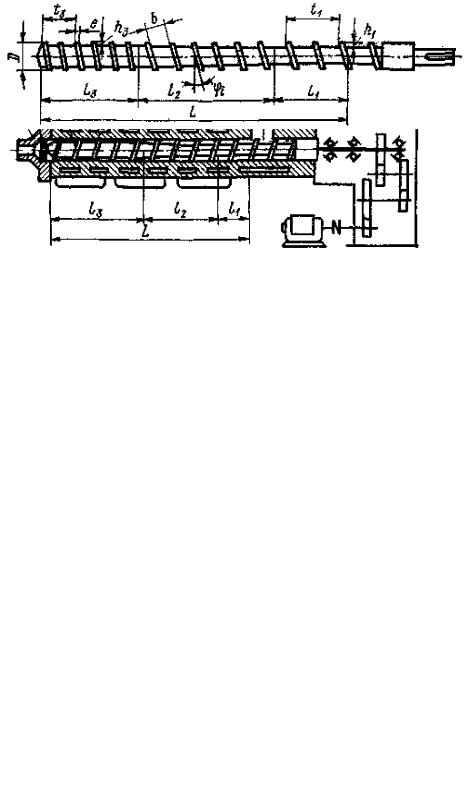
стическое состояние; зону дозирования l3 , где материал нагревается до температуры формования.
Рис. 6. Схема червячной машины
Главным рабочим органом машины является червяк. Конструкция червяка характеризуется следующими основными геометрическим пара- метрами (рис. 7): наружным диаметром D , длиной рабочей части L , ша- гом нарезки t1 и t3 или углом подъема винтовой линии ϕ , глубиной нарез-
ки h1 и h3 , шириной гребня нарезки e , числом заходов нарезки i и вели-
чиной геометрической компрессии Aг , шириной нарезки канала b .
За рабочую длину червяка принимается длина нарезной части, от- считываемая от передней кромки загрузочного отверстия. Длина загрузоч- ного отверстия равна (1,5 ¸ 2,0) × D .
По рабочей длине червяка в общем случае различают три геометри- ческие зоны (рис. 7): зону загрузки L1 ; зону сжатия L2 ; зону дозирования
L3 . Длины геометрических зон червяка могут не совпадать с длинами тех-
нологических зон машины.
Рис. 7. Геометрические характеристики червяка
232
Диаметры червяка D и отношение L / D нормализованы. Диаметр червяка следует выбирать из следующего параметрического ряда: 20, 32, 45, 63, 90, 125, 160, 200, 250, 320, 400, 450, 500 мм. Отношение L / D =20; 25 для типовых одночервячных универсальных прессов при переработке термопластов; L / D =30 для специальных червяных прессов; L / D =12÷18 для литьевых машин при переработке реактопластов; L / D =3; 4; 5 для од- ночервячных прессов при переработке горячих резиновых смесей; L / D =8; 10; 12 при переработке холодных резиновых смесей и L / D =12; 15 для двухчервячных прессов.
Конструкция червяка в большинстве случаев предусматривает плав- ное или ступенчатое уменьшение объемов межвиткового пространства от зоны загрузки до формующей головки. Создается это за счет уменьшения глубины или шага нарезки червяка и характеризуется величиной геомет- рической компрессии Aг . Для одночервячной машины
|
|
|
|
|
h |
(t |
- i × e |
) × cos j |
|
Dср |
||
|
|
|
|
A = |
1 |
× |
1 |
1 1 |
3 |
× |
1 |
, |
|
|
|
|
|
(t3 |
- i3 × e3 ) × cos j1 |
|
|||||
|
|
|
|
г |
h3 |
|
Dср |
|||||
|
|
|
|
|
|
|||||||
|
|
|
|
|
|
|
|
|
|
|
3 |
|
где Dср – средний диаметр нарезки; |
|
|
|
|
||||||||
|
t |
|
|
|
|
|
|
|
|
|
|
|
j = arctg |
|
|
|
– угол подъема нарезки. |
|
|
|
|||||
π× |
|
|
|
|
||||||||
|
D |
|
|
|
|
|
|
|
|
|
Червяки одночервячных машин выполняются обычно с постоянным шагом t и переменной глубиной нарезки h . Число заходов нарезки червя- ка при переработке термопластов i = 1; для резин i = 1; 2 .
При t = const и i = const можно принять
Aг = 0,93 ×(h1 / h3 ) .
С переменным шагом t и h = const делаются червяки больших диа- метров ( D ³ 160 ) для машин по переработке резин. В этом случае
Aг = t1 / t3 .
При выборе величины геометрической компрессии можно ориенти-
роваться на следующие рекомендации: |
Aг |
= 2,5 ¸ 4,5 |
для термопластов; |
||
Aг = 5 ¸ 6 |
для фторопласта; Aг |
= 1,2 ¸1,35 |
для резин; |
Aг = 0,8 ¸1,1 для ре- |
|
актопластов. |
|
|
|
|
|
Шаг |
нарезки червяков |
выбирается |
из следующих значений: |
t = (0,8 ¸1,2) × D для переработки термопластов; t = (0,4 ¸ 0,6) × D для пере-
работки резиновых смесей. В крупных машинах при переработке резин шаг нарезки плавно уменьшается от t1 = (0,9 ¸1,0) × D до t3 = (0,6 ¸ 0,7) × D .
233
У типовых червяков для переработки термопластов принят шаг на- резки t = D .
Глубина нарезки в зоне загрузки для переработки термопластов h1 = (0,12 ¸ 0,16) × D ; для резин h1 = (0,17 ¸ 0,25) × D .
Ширина гребня нарезки принимается равной e = (0,05 ¸ 0,12) × D .
В условиях переработки большинство полимеров при достижении пластичного состояния ведет себя как аномально-вязкие (псевдопластич- ные) жидкости, напряжение сдвига у которых, в отличие от ньютоновских жидкостей, возрастает не пропорционально скорости деформации. Наибо- лее простой зависимостью, связывающей напряжение сдвига τ и градиент скорости деформации γɺ, является степенной закон
τ = µ1 ×(γɺ)m ,
где µ1 – коэффициент консистентной вязкости, Па·с;
m < 1 – показатель степени, характеризующий отклонение поведения материала от ньютоновского.
При инженерных расчетах оборудования для переработки полимеров обычно пользуются не напряжением сдвига, а так называемой эффектив- ной вязкостью mэ, которую можно представить как
µэ = µ1 ×(γɺ)m−1 .
Для приближенной характеристики текучести различных марок тер- мопластичных материалов применяют условный показатель текучести расплава ПТР, представляющий собой количество материала, г, вытекшее из капилляра под действием груза за 10 мин.
Объемная производительность одночервячной машины при прове- рочном расчете определяется по зоне дозирования. При этом материал рас- сматривают как ньютоновскую жидкость с эффективной вязкостью, взятой при средней скорости сдвига и средней температуре в зоне в условиях ла- минарного течения. При таких допущениях объемная производительность может быть рассчитана по уравнению
V = V × n - K |
p |
× p - K |
з |
× p |
, м3/с, |
в |
µк |
µз |
|
||
|
|
|
|
где Vв – объем межвиткового пространства по длине шага нарезки, м3;
K p , K з – коэффициенты геометрической формы канала червяка и кольцевого канала зазора между гребнем витка и цилиндром, м3;
234

µк, µз – эффективные вязкости расплава в канале червяка и в зазоре,
Па·с;
n – частота вращения червяка, с-1;
p – перепад давления в зоне дозирования, определяемый величи-
ной сопротивления формующей головки, Па.
При расчете производительности червяков с постоянной глубиной нарезки в зоне дозирования значения Vв , K p , K з рассчитываются по сле-
дующим формулам:
|
= |
|
π × D × h × (t - i × e) × cos2 j |
×Фв ; |
|||||
Vв |
|
|
|
3 |
|
|
|||
|
|
|
2 |
|
|
||||
|
|
|
|
|
|
|
|
|
|
|
= |
|
h3 |
× (t - i × e) ×sin j × cos j |
×Фp |
|
|||
K p |
|
3 |
|
|
|
; |
|||
|
|
12 × L3 |
|||||||
|
|
|
|
|
|
|
|||
|
|
|
|
з = |
p2 × D2 × δ3 |
× tgj ×sin j |
|
||
|
K |
10 × e |
×i × L3 |
, |
|
||||
|
|
|
|
|
|
|
где δ – величина радиального зазора между цилиндром и червяком, мм; Фв ,Фp – форм-факторы, учитывающие тормозящее влияние боковых
стенок, зависящие от относительного размера сечения винтового канала h / b . Значения форм-факторов могут быть найдены из выражений:
|
h 2 |
|
|
h |
|
|||||
Фв = 0,125 × |
|
|
|
|
- 0,625 × |
|
|
+1; |
||
|
|
|
|
|||||||
|
b |
|
|
b |
|
|||||
|
h 2 |
|
h |
|
|
|||||
Фp |
= 0,13× |
|
|
|
|
- 0,71× |
|
|
+1. |
|
|
|
|
b |
|||||||
|
b |
|
|
|
Значения µк и µз определяются из реологических кривых течения при средней температуре в зоне дозирования или рассчитываются при из- вестных реологических константах µ1 и m .
Скорость сдвига в канале червяка определяется по формуле
|
ɺ |
|
π2 × (D - h ) × (D - 2 × h ) × n |
|
-1 |
|
||||||
|
= |
|
|
|
ср |
ср |
, с |
, |
||||
|
γк |
|
|
|
|
|
|
|
|
|||
|
|
|
|
|
|
|
|
|
||||
|
h × π2 × (D - 2 × h )2 |
+ t2 |
|
|||||||||
|
|
|
|
|
|
|||||||
|
|
|
ср |
|
|
ср |
|
|
|
|
|
|
а в зазоре – |
по формуле |
|
|
|
|
|
|
|
|
|
|
|
|
|
|
ɺ |
|
|
π2 × D2 × n |
|
|
|
|
|
|
|
|
|
= δ× (π2 × D2 + t 2 ) |
, |
|
|
|
|
||||
|
|
|
γз |
|
|
|
|
|||||
где hср – |
средняя глубина нарезки в зоне дозирования. |
235

Индикаторная или полезная мощность, затрачиваемая в червячной машине на переработку полимерного материала,
|
|
Nинд = N1 + N 2 + N3 + N г , |
|
где |
N1, N 2 , N3 , N г |
– расход мощности соответственно в зоне загрузки, |
|
плавления, дозирования, в формующей головке. |
|||
|
Величиной N1 |
вследствие ее сравнительной малости можно пренеб- |
|
речь. |
|
|
|
|
Мощность, расходуемая в зоне плавления, |
||
|
|
′ |
′′ |
|
|
N 2 = N 2 |
+ N2 , |
где |
′ |
|
|
N 2 – мощность, затрачиваемая на трение и диссипацию энергии в |
зазоре δ0 между цилиндром и поверхностью пробки твердого (на распла-
вившегося) материала, Вт;
′′ |
мощность, затрачиваемая в зазоре δ между цилиндром и греб- |
|||||||
N 2 – |
||||||||
нем витка, Вт. |
|
|
|
|
|
|
|
|
Первая составляющая мощности |
|
|
||||||
|
N ¢ |
= µ |
|
× Dw2 |
× |
|
t - i × e |
×l , |
|
|
|
× δ0 × tgj |
|||||
|
2 |
|
э |
пр |
2 |
2 |
||
где Dw2 |
– скорость перемещения пробки твердой фазы полимера по от- |
|||||||
пр |
|
|
|
|
|
|
|
|
ношению к стенке цилиндра, м/с,
Dwпр = (π× D × n - wпр × cos j)2 + (wпр ×sin j)2 .
Скорость движения пробки вдоль винтового канала определяется из выражения
|
wпр = |
|
G |
, |
|
rн |
×b × h1ср |
||
|
|
|
||
где ρ – |
насыпная плотность материала, кг/м3; |
|||
н |
|
|
|
|
G – |
массовая производительность машины, кг/с; |
|||
h1ср |
– среднее значение глубины нарезки в зоне загрузки, м. |
|||
Величина эффективной вязкости µэ определяется при средней тем- |
||||
пературе пристенного слоя tсл = (tц + tпл ) / 2 |
и среднем градиенте скорости |
γɺ = wпр / δ0 .
Толщина слоя расплава над пробкой материала в межвинтовом про- странстве
236
δ0 |
= |
|
2 ×(t - i × e) |
×Ф . |
||
ρ |
т |
× w ×sin j |
||||
|
|
|
||||
|
|
|
пр |
|
Величина Ф рассчитывается по формуле
Ф = |
|
λ×(tц |
- tпл ) |
|
|
|
|
, |
|
|
|
|
||
|
ст |
×(tпл - t1 ) + rпл |
где λ – теплопроводность расплава при средней температуре пристенно- го слоя tсл = (tц + tпл ) / 2 ;
cт – удельная теплоемкость твердой фазы полимера при средней температуре tср = (t1 + tпл ) / 2 ;
rпл – удельная теплота плавления, Дж/кг;
tц, tпл, t1 – соответственно температура стенки цилиндра, плавления
и загружаемого материала.
Мощность, диссипируемая в зазоре толщиной δ,
N ¢¢ = |
π2 × D2 × n2 |
×µ |
|
×i × e ×l . |
|
з |
|||
2 |
tgj × δ |
|
2 |
|
|
|
|
|
Эффективная вязкость µз в зазоре δ определяется при температуре пленки tпл ≈ tц и градиенте скорости γɺз .
Мощность в зоне дозирования затрачивается на преодоление трения
расплава в канале червяка N ′ и в зазоре между цилиндром и гребнем вит-
3
ка червяка N ′′ :
3
|
|
|
N ¢ = |
π3 × (t - i × e) ×l × I |
×µ |
|
× n |
2 |
|
|
|
||
|
|
|
3 |
|
к |
|
. |
|
|
||||
|
|
|
|
|
|
|
|
||||||
|
|
|
|
3 |
t |
|
|
|
|
|
|
||
|
|
|
|
|
|
|
|
|
|
|
|
||
Коэффициент I |
в общем случае для червяка с переменной глубиной |
||||||||||||
нарезки и шагом t = const определяется из выражения |
|
|
|||||||||||
I = |
π2 |
× D2 - 4 ×t 2 |
+ |
( D + d3 )3 - ( D + dн )3 |
+ |
|
|
|
2,3 × π2 × D5 |
|
) , |
||
|
|
|
|
(t2 + π2 × D2 )×(h - h |
|||||||||
|
π2 |
|
3 ×(d3 - dн ) |
||||||||||
|
|
|
|
|
|
|
|
|
|
|
н |
3 |
|
где hн , dн |
– соответственно глубина канала и диаметр сердечника в на- |
||||||||||||
чале зоны дозирования, м; |
|
|
|
|
|
|
|
|
|
||||
h3 , d3 |
– соответственно глубина канала и диаметр сердечника в кон- |
||||||||||||
це зоны дозирования, м. |
|
|
|
|
|
|
|
|
|
|
237
Мощность N |
′′ |
, диссипируемая в зазоре, рассчитывается по формуле |
||||
3 |
||||||
|
|
N ¢¢ = |
π2 × D2 × n2 |
×µ |
|
×i × e ×l . |
|
|
|
з |
|||
|
|
3 |
tgj × δ |
3 |
||
|
|
|
|
|
||
Мощность, диссипируемая в формующей головке, |
N г = V × Dpг .
Мощность электродвигателя привода машины
Nэ = Nинд / η,
где η – коэффициент, учитывающий потери энергии в приводе червяч-
ной машины, и другие, неучтенные расчетом потери; η = 0,7 ÷ 0,8 .
При упрощенных расчетах, когда не учитывается мощность, затра- чиваемая в зонах загрузки и плавления, кпд машины принимают η = 0,5 ÷ 0,6 .
Примеры для самостоятельного решения
Рассчитать мощность, теряемую в зоне дозирования одночервячной машины, оснащенной типовым червяком с L / D = 20 и t = D при перера- ботке полиэтилена низкой плотности ПЭНП и непластифицированного ПВХ. Исходные данные для расчета приведены в табл. 7. Зависимости из- менения плотности, теплопроводности и теплоемкости термопластов от температуры, необходимые для решения задач, приведены на рис. 8 – 10.
|
|
|
|
|
|
|
|
|
|
Таблица 7 |
|
|
|
|
Исходные данные для расчета |
|
|
|
|
||||
|
|
|
|
|
|
|
|
|
|
|
|
№ |
G , |
Марка |
|
Тип |
D , |
h3 , |
h1, |
n , |
t з , |
|
tц , |
вар. |
кг/ч |
материала |
|
червяка |
мм |
мм |
мм |
с-1 |
° С |
|
° С |
1 |
2 |
3 |
|
4 |
5 |
6 |
7 |
8 |
9 |
|
10 |
1 |
|
|
|
1А |
|
|
|
|
|
|
|
2 |
30 |
ПЭВП |
|
1Б |
45 |
2,2 |
8,2 |
1,1 |
160 |
|
220 |
3 |
ПТР–0,3 |
|
2А |
|
|||||||
|
|
|
|
|
|
|
|
|
|||
4 |
|
|
|
2Б |
|
|
|
|
|
|
|
5 |
|
|
|
1А |
|
|
|
|
|
|
|
6 |
45 |
ПЭНП |
|
1Б |
63 |
3,0 |
10,5 |
1,1 |
160 |
|
200 |
7 |
ПТР–0,3 |
|
2А |
|
|||||||
|
|
|
|
|
|
|
|
|
|||
8 |
|
|
|
2Б |
|
|
|
|
|
|
|
9 |
|
|
|
1А |
|
|
|
|
|
|
|
10 |
90 |
ПЭНП |
|
1Б |
90 |
4,0 |
14,8 |
0,85 |
180 |
|
240 |
11 |
ПТР–0,3 |
|
2А |
|
|||||||
|
|
|
|
|
|
|
|
|
|||
12 |
|
|
|
2Б |
|
|
|
|
|
|
|
238
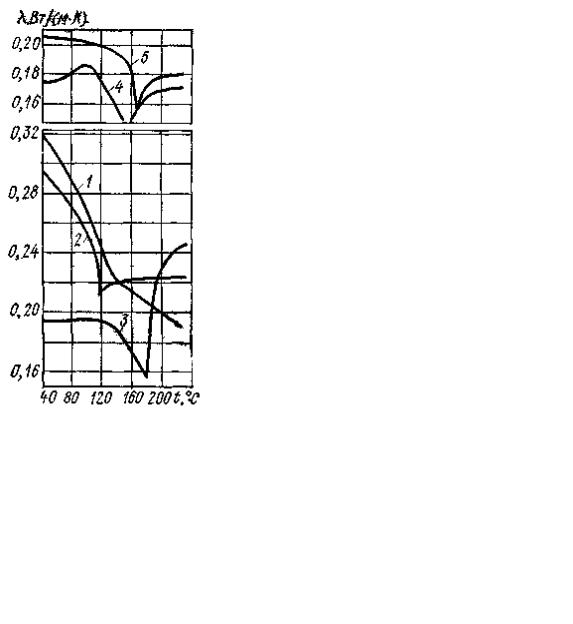
Окончание табл. 7
1 |
2 |
3 |
4 |
5 |
6 |
7 |
8 |
9 |
10 |
|
13 |
|
|
1А |
|
|
|
|
|
|
|
14 |
150 |
ПЭНП |
1Б |
125 |
5,0 |
17,5 |
0,72 |
180 |
220 |
|
15 |
ПТР–0,3 |
2А |
||||||||
|
|
|
|
|
|
|
||||
16 |
|
|
2Б |
|
|
|
|
|
|
|
17 |
|
|
1А |
|
|
|
|
|
|
|
18 |
220 |
ПЭНП |
1Б |
160 |
6,0 |
21,0 |
0,53 |
160 |
200 |
|
19 |
ПТР–0,3 |
2А |
||||||||
|
|
|
|
|
|
|
||||
20 |
|
|
2Б |
|
|
|
|
|
|
|
21 |
30 |
|
3А |
45 |
2,5 |
8,5 |
1,10 |
|
|
|
22 |
40 |
|
3Б |
63 |
3,0 |
10,5 |
1,05 |
|
|
|
23 |
90 |
ПВХнп |
3А |
90 |
4,2 |
15,0 |
0,83 |
160 |
190 |
|
24 |
140 |
|
3Б |
125 |
5,1 |
17,6 |
0,72 |
|
|
|
25 |
230 |
|
3А |
150 |
6,1 |
21,5 |
0,53 |
|
|
Рис. 8. Зависимость плотности термопластов от температуры: 1 – ПЭВП; 2 – ПЭНП; 3 – ПП; 4 – ПВХпл;
5 – ПВХнп
Рис. 9. Зависимость теплопроводности термопластов от температуры:
1 – ПЭВП; 2 – ПЭНП; 3 – ПП; 4 – ПВХпл; 5 – ПВХнп
239

Рис. 10. Зависимость теплоемкости термопластов от температуры:
1 – ПЭВП; 2 – ПЭНП; 3 – ПП; 4 – ПВХПЛ; 5 – ПВХНП
ДРОБИЛЬНО-РАЗМОЛЬНЫЕ МАШИНЫ И ГРОХОТЫ
Дробилки щековые
Щековые дробилки предназначены для крупного и среднего дробле- ния горных пород. По принципу действия они подразделяются на дробил- ки простого и сложного качания. Измельчение материала происходит пу- тем раздавливания, раскалывания и истирания при поджатии подвижной щеки к неподвижной.
Во избежание выталкивания дробимого материала угол между под- вижной и неподвижной щеками (угол захвата α) должен быть < 2j, кото- рый обычно принимают
α »1, 4 × j,
где ϕ – угол трения между дробимым материалом и щекой.
У большинства дробилок угол захвата α = 20 .
Число n качаний подвижной щеки, соответствующее числу оборотов эксцентрикового вала, обусловлено оптимальным выходом материала из
240