
laboratornyj praktikum bitumy-asfaltobeton
.pdf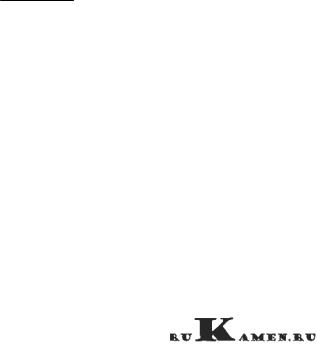
22
3.4. Определение остатка на сите
Приборы и материалы: лабораторные весы, сушильный шкаф, сито с сеткой № 014, чашка фарфоровая 250 мл, стеклянная палочка, стеклянный стакан 250 мл, соляная кислота (1%-ный раствор), едкий натр (1%-ный раствор), дистиллированная вода, бензин.
Предварительно тщательно промытое бензином и высушенное сито помещают в фарфоровую чашку и взвешивают, затем сито вынимают из чашки и обильно смачивают:
для анионных эмульсий 1%-ным раствором едкого натра;
для катионных эмульсий 1%-ным раствором соляной кислоты.
Встеклянный стакан отвешивают 100 г предварительно перемешанной эмульсии. Навеску эмульсии равномерно процеживают через сито. При процеживании анионной эмульсии одновременно с эмульсией вливают раствор щелочи, при процеживании катионной – раствор кислоты; освобожденный от эмульсии стакан и стеклянную палочку промывают раствором щелочи или кислоты, сливая его на сито. Остаток на сите также промывают, пропуская через сито раствор щелочи или кислоты до получения прозрачных промывных вод, не содержащих следов эмульсии.
После этого сито ставят в фарфоровую чашку, вместе с кото-
рой его предварительно взвешивали, сушат до постоянной массы при температуре 105±5 оС, охлаждают до комнатной температуры и взвешивают вместе с чашкой. Остаток на сите М, % по массе, вычисляют по формуле
M m2 m1 100, m3
где m1 |
– масса сита и чашки, г; |
m2 |
– масса сита с остатком и чашкой, г; |
m3 |
– масса эмульсии, г. |
Остаток на сите вычисляют как среднее арифметическое значение результатов двух параллельных определений, округленное до целого числа.

23
3.5. Определение условной вязкости
Приборы: прибор для определения условной вязкости с отверстием 3 мм, секундомер, мерный цилиндр.
Внутреннюю поверхность цилиндра прибора, а также затвор тщательно промывают бензином или другим растворителем и просушивают при комнатной температуре. Сточное отверстие рабочего цилиндра закрывают затвором и подставляют под него мерный цилиндр. Баню прибора наполняют водой с температурой 20±0,5 оС.
Эмульсию с температурой 20±0,5 оС наливают в рабочий цилиндр прибора при закрытом затворе до уровня отметки на затворе. Залитую в цилиндр прибора эмульсию хорошо перемешивают термометром, замеряют температуру, вынимают термометр и быстро поднимают затвор. При сливе эмульсия не должна разбрызгиваться по стенкам мерного цилиндра.
В момент, когда уровень эмульсии в мерном цилиндре достигнет отметки 25 см3, включают секундомер. Когда уровень битума достигнет отметки 75 см3, секундомер останавливают и вычисляют время истечения эмульсии.
За условную вязкость принимают время истечения в секундах 50 см3 эмульсии. За результат испытания принимают среднее арифметическое результатов двух определений, округленное до целого числа.
3.6. Определение устойчивости при хранении
Приборы и материалы: лабораторные весы, сушильный шкаф, сито с сеткой № 014, чашка фарфоровая 250 мл, стеклянная палочка, стеклянный стакан 250 мл, стеклянные цилиндры 250 мл с плотно закрывающимися крышками – 4 шт.; соляная кислота (1%- ный раствор), едкий натр (1%-ный раствор), дистиллированная вода, бензин.
В каждый из четырех цилиндров отвешивают по 200 г эмульсии. Цилиндры плотно закрывают и оставляют на хранение в спокойном состоянии при комнатной температуре.
По истечении 7 суток проводят испытание эмульсии из двух цилиндров, эмульсию из двух других цилиндров испытывают по истечении 30 суток. Испытания и обработку результатов проводят так же как и определение остатка на сите битумной эмульсии (см. п. 4 «Определение остатка на сите» данной лабораторной работы, стр. 22).
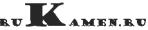
24
3.7. Определение сцепления эмульсии 1-го и 2-го классов с поверхностью щебня
Приборы и материалы: стаканы химические термостойкие 500 мл, электроплитка, асбестовая сетка, дистиллированная вода, фильтровальная бумага, гранитный щебень фракции 20…40 мм, щебень из карбонатных пород фракции 20…40 мм, штатив, сушильный шкаф, секундомер.
Навеску щебня из карбонатных пород при испытании анионных эмульсий или из гранита при испытании катионных эмульсий массой 1 кг каждая промывают и высушивают в сушильном шкафу при температуре 105±5 оС. Затем щебень равномерно распределяют на листе бумаги, линейкой делят пробу на четыре квадрата, из каждого берут для испытания по одному зерну щебня. Зерна обвязывают ниткой или мягкой проволокой, погружают на 1…2 с в стакан с дистиллированной водой, вынимают из воды, стряхивают капли и сразу окунают 2…3 раза в испытуемую эмульсию, затем подвешивают на штативе так, чтобы зерна щебня не касались друг друга.
Зерна щебня испытывают через сутки. На закрытой электроплитке нагревают до 100 оС стакан с дистиллированной водой (не допуская бурного кипения), каждое из подвешенных на штативе зерен щебня поочередно погружают в кипящую воду на 30 мин.
Таблица 3.1 Оценка качества сцепления эмульсии со щебнем
|
Оценка |
Характеристика пленки вяжущего |
сцепления, |
|
балл |
Пленка вяжущего полностью сохраняется на |
|
поверхности зерен |
5 |
Пленка вяжущего частично отделилась с острых |
|
углов и ребер зерен |
4 |
Пленка вяжущего свыше 50 % сохраняется на |
|
поверхности зерен |
3 |
Пленка вяжущего менее 50 %сохраняется на |
|
поверхности зерен |
2 |
По истечении указанного времени фильтровальной бумагой снимают с поверхности воды всплывшее вяжущее, вынимают зерна щебня, погружают их на 1…2 с в холодную воду, вынимают из воды и помещают на фильтровальную бумагу. Поверхность зерен щебня осматривают и проводят оценку качества сцепления эмульсии со
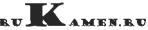
25
щебнем по степени сохранности пленки вяжущего в соответствии с табл. 3.1. За результат испытаний принимают среднеарифметическое значение результатов четырех определений, округленное до целого числа.
3.8. Определение сцепления эмульсии 3-го класса с минеральной частью смеси
Приборы и материалы: весы лабораторные, стаканы химические термостойкие 500 мл, сетки металлические с размером отверстий 0,16 мм с проволочными дужками (диаметр сетки должен быть на 5…10 мм меньше диаметра химического стана), электроплитка или баня песчаная, асбестовая сетка, дистиллированная вода, фильтровальная бумага, секундомер.
Готовят смесь эмульсии со смесью минеральных материалов плотного зернового состава (см. работу «Определение устойчивости эмульсии при перемешивании с минеральными материалами», стр. 21).
Приготовленную смесь раскладывают на фильтровальной бумаге и оставляют при комнатной температуре. На следующий день от смеси берут две навески по 50 г каждая. Одну навеску помещают на сетку, вторую оставляют для последующего сравнения со смесью, прошедшей испытание.
Химический стакан заполняют примерно на 2/3 объема дистиллированной водой, устанавливают на электрическую плитку или песчаную баню и доводят до кипения. Сетку с навеской смеси опускают в стакан с кипящей водой таким образом, чтобы уровень воды над смесью был не менее 30…40 мм, и укрепляют проволочными дужками за край стакана. Сетку с испытуемым образцом выдерживают в кипящей воде 30 мин. Кипение не должно быть бурным. Вяжущее, отделившееся от поверхности минеральных зерен в процессе кипения и всплывшее на поверхность, удаляют фильтровальной бумагой.
По истечении указанного времени сетку со смесью извлекают из стакана и переносят в стакан с холодной водой для охлаждения, после чего смесь переносят на фильтровальную бумагу. Смесь осматривают и, сравнивая со смесью, не проходившей испытание, проводят оценку качества сцепления эмульсии с минеральными материалами в соответствии с табл. 3.1. За результат испытания принимают среднеарифметическое значение результатов двух определений, округленное до целого числа.
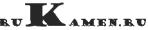
26
3.9. Определение физико-механических свойств остатка после испарения воды из эмульсии
Эмульсию наливают в выпарительную чашку в количестве не менее 500 мл, ставят на электрическую плитку и выпаривают из нее воду, не допуская интенсивного кипения, периодически помешивая стеклянной палочкой. Выпаривание заканчивают, когда прекращается выделение пузырьков пара и поверхность остатка станет зеркальной.
Вполученном остатке определяют:
глубину проникания иглы в остаток – так же, как и глубину проникания (пенетрацию) вязких битумов (см. лабораторную работу «Определение свойств вязких дорожных битумов». стр 3);
температуру размягчения по кольцу и шару остатка – так же, как и температуру размягчения по кольцу и шару вязких битумов (см. лабораторную работу «Определение свойств вязких дорожных битумов», стр. 5);
растяжимость остатка – так же, как и растяжимость вязких битумов при 25о С (см. лабораторную работу «Определение свойств вязких дорожных битумов», стр. 7);
эластичность остатка при 25о С.
Эластичность остатка определяют после определения растяжимости остатка. Формы с разорвавшимися образцами снимают со штифтов и укладывают на дно ванны дуктилометра или другой емкости с водой. С целью ускорения сокращения образцов температуру воды доводят до 35±0,5 оС. Затем проводят замеры обеих частей образца с точностью до 1,0 мм от свободного конца образца до зажима формы. Измерения проводят до момента изменения длины не более 0,1 мм за 15 мин.
Показатель эластичности Э, %, определяют по формуле
Э |
( Д Lo ) L |
100, |
|
Д |
|||
|
|
где Д – растяжимость, см;
Lo – длина образца до его растяжения, равная 3 см;
L – сумма длин двух частей образца после их восстановления (по последнему замеру), см.
За эластичность принимают среднеарифметическое значение результатов трех параллельных определений, округленное до целого числа. Допустимое расхождение между результатом каждого определения и среднеарифметическим значением не должно превышать 10 % среднеарифметического результата.
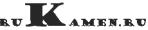
27
3.10. Определение устойчивости при транспортировании
Приборы: аппарат для встряхивания жидкостей в сосудах, выполняющий 130±5 движений в минуту (65 движений вперед, 65 движений обратно) с амплитудой 8 мм, колбы стеклянные плоскодонные 250 мл, 2 шт.
Эмульсию тщательно перемешивают и наливают по 200 мл в чистые сухие колбы, плотно закрывают их пробками и устанавливают на площадку аппарата, закрепляя зажимами.
Испытание эмульсии производят в течение 2 ч. По истечении времени испытания аппарат выключают, колбы снимают и, когда образовавшаяся пена спадет, производят визуальную оценку состояния эмульсии. Эмульсию считают выдержавшей испытание, если не произошло необратимого распада эмульсии на воду и вяжущее, что характеризуется появлением четко выраженной границы между вяжущим и водой в колбе.
4. АСФАЛЬТОБЕТОН
Асфальтобетонная смесь - это рационально подобранная смесь минеральных материалов [щебня (гравия) и песка с минеральным порошком или без него] с битумом, взятых в определенных соотношениях и перемешанных в нагретом состоянии.
Асфальтобетон - это уплотненная асфальтобетонная смесь.
4.1. Требования, предъявляемые к асфальтобетону
Асфальтобетон применяется для устройства покрытий и оснований автомобильных дорог, аэродромов, городских улиц и площадей, дорог промышленных предприятий.
Основные параметры и типы асфальтобетонных смесей и асфальтобетона представлены в табл. 1 прил. 2. В зависимости от показателей физико-механических свойств и применяемых материалов асфальтобетон подразделяется на марки I, II и III, указанные в табл. 2 прил. 2.
Зерновые составы минеральной части смесей и асфальтобетонов должны соответствовать:
для верхних слоев покрытий автомобильных дорог - пределам, представленным в табл. 3 и на рис. 1 прил. 2.
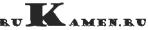
28
для нижних слоев покрытий и оснований – данным табл. 4 прил. 2.
Показатели физико-механических свойств высокоплотных и плотных асфальтобетонов из горячих смесей различных марок, применяемых во II и III климатических зонах, должны соответствовать данным табл. 5 прил. 2.
Водонасыщение высокоплотных и плотных асфальтобетонных смесей и пористость минеральной части асфальтобетонов из горячих смесей должны соответствовать данным. указанным в табл. 6 прил.2.
Рекомендуемое содержание битума в асфальтобетонных смесях представлено в табл. 7. прил. 2.
Для верхних слоев покрытий автомобильных дорог и городских улиц выбор вида и марки асфальтобетона и марки битума нужно производить по рекомендациям ГОСТ 9128-97 (табл. 8 прил.2).
При выборе типа и марки смеси необходимо учитывать закономерности. Например, при интенсивности движения, соответствующей дороге I категории, т.е свыше 7000 авт/сут, требуется высокая сдвигоустойчивость асфальтобетона, что обеспечивается смесями типа А марки I, содержащими повышенное количество прочного щебня. На дороге IV категории можно применять смеси типа В марок II и III. В соответствии с этой закономерностью тип и марку смесей выбирают по табл. 9 прил. 2.
Область применения асфальтобетонов при устройстве верхних слоев взлетно-посадочных полос и магистральных рулежных дорожек аэродромов представлена в табл. 10 прил. 2.
4.2. Требования, предъявляемые к материалам для приготовления асфальтобетонной смеси
4.2.1. Нефтяные дорожные битумы
Марку вязкого битума, а также класс и марку жидкого битума выбирают в зависимости от вида асфальтобетона, климатических условий района строительства и категории дороги.
Для приготовления горячих смесей применяют вязкие нефтяные битумы марок БНД 40/60, БНД 60/90, БНД 90/130, БН 60/90 по ГОСТ 22245-90 и жидкие битумы марок СГ 130/200, МГ 130/200 и МГО 130/200 по ГОСТ 11955-82. Область применения марок битумов приведена в прил.1 (табл. 1) и прил. 2 (табл. 8 и 10).
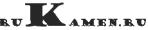
29
4.2.2. Щебень и гравий
Для асфальтобетонных смесей применяют щебень из естественного камня, полученный дроблением горных пород, а также щебень из гравия, металлургических шлаков, соответствующих требованиям стандартов.
Щебень, полученный из магматических и метаморфических горных пород должен иметь прочность не менее 1000…1200 МПа, а осадочных карбонатных горных пород и металлургических шлаков - не менее 80…100 МПа. Для нижнего слоя асфальтобетонного покрытия можно применять щебень из горных пород и металлургических шлаков прочностью не менее 60 МПа.
Показатель износостойкости щебня в полочном барабане – 25…35%, содержание пыли и глины – не более 2%. Форма зерен щебня должна быть приближена к тетраидной и кубовидной, а поверхность – шероховатой. содержание лещадных и игловатых зерен ограничивается 15…25%. Морозостойкость щебня для верхнего слоя покрытия должна быть не менее 50 циклов, для нижнего – не менее 25.
Дробленый гравий должен содержать не менее 80% дробленых зерен. К нему предъявляются те же требования, что и к щебню из скальных горных пород.
4.2.3. Песок
Для приготовления асфальтобетона применяют средне- и крупнозернистые природные и дробленые пески и отсевы продуктов дробления горных пород и гравия, которые должны соответствовать требованиям ГОСТ 8736. Песок должен быть чистым и содержать глинистых частиц, определяемых методом набухания, не более 0,5…1% в зависимости от типа и марки асфальтобетона.
По прочности исходной горной породы дробленый песок делят на марки:1000, 800, 600 и 400.
4.2.4. Минеральный порошок
Минеральный порошок, входящий в состав асфальтобетонов, должен соответствовать требованиям ГОСТ 16557
Минеральный порошок получают размолом известняков, доломитов прочностью не менее 20 МПа. Карбонатные породы, используемые для получения минеральных порошков, не должны содержать глинистых примесей более 5%.
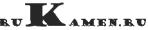
30
Тонкость помола порошков должна быть такой, чтобы при мокром рассеве сквозь сито с отверстиями 1,25 мм проходило 100%, 0,315 мм - не менее 90% и 0,071 мм – не менее 70% порошка. При этом пустотность их при уплотнении в специальной форме грузом 40 МПа должна быть не более 35%.
Для асфальтобетонов не рекомендуются порошки с коэффициентом гидрофильности более 1 (отношение набухания минерального порошка в воде к набуханию в обезвоженном керосине). Набухание смеси порошка с битумом при остаточной пористости образцов 5…6% не должна превышать 2,5%.
Допускается применять в качестве минеральных порошков для пористого и высокопористого асфальтобетона, а также для плотного асфальтобетона II и III марок техногенные отходы промышленного производства (измельченные основные металлургические шлаки, золы-уноса, золошлаковые смеси, пыль-уноса цементных заводов и пр.) при условии соответствия их требованиям ГОСТ9128-97.
4.3. Подбор состава асфальтобетона
Проектирование асфальтобетона включает в себя:
1)анализ условий работы проектируемого асфальтобетона
вконструкции;
2)выбор способа производства работ в зависимости от по- годно-климатических условий района строительства;
3)выбор исходных материалов с учетом их стоимости и дефицитности;
4)расчет состава асфальтобетона, который включает в себя:
подбор состава минеральной части;
расчет оптимального содержания битума;
приготовление и испытание контрольных образцов асфальтобетона.
4.3.1. Пример подбора состава асфальтобетона
Задание. Подобрать состав горячего мелкозернистого асфальтобетона типа Б, марки I непрерывной гранулометрии, предназначенного для верхнего слоя покрытия автомобильной дороги II категории во II дорожно-климатической зоне.
Характеристика исходных материалов Щебень гранитный марки 1200 по прочности при раздавлива-
нии в цилиндре. Гранулометрический состав приведен в табл.4.1.
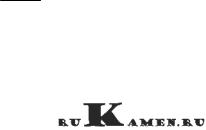
31
Таблица 4.1
|
Показатели |
|
|
|
|
Размеры отверстий сит, мм |
|||||||||||||||||||
|
|
|
|
|
|
|
40 |
|
|
20 |
|
|
15 |
|
10 |
|
|
5 |
|
|
<5 |
||||
|
Частные остатки, % |
|
|
0 |
|
|
8,3 |
|
21,5 |
35,2 |
|
|
32,4 |
|
2,6 |
||||||||||
|
|
|
|
|
|
|
|
|
|
|
|
|
|
|
|
|
|
|
|
|
|
|
|||
|
Полные остатки, % |
|
|
0 |
|
|
8,3 |
|
29,8 |
65,0 |
|
|
97,4 |
|
100 |
||||||||||
|
Песок речной. Гранулометрический состав приведен в табл. 4.2. |
||||||||||||||||||||||||
|
|
|
|
|
|
|
|
|
|
|
|
|
|
|
|
|
|
|
|
|
|
Таблица 4.2 |
|||
|
Показатели |
|
|
|
|
|
Размеры отверстий сит, мм |
|
|
||||||||||||||||
|
|
|
5 |
|
2,5 |
1,25 |
|
|
0,63 |
0,315 |
0,16 |
|
0,071 |
<0,071 |
|||||||||||
|
Частные остат- |
|
9,8 |
|
14,0 |
16,0 |
|
|
20,9 |
|
20,6 |
13,6 |
|
3,4 |
|
1,7 |
|||||||||
|
ки, % |
|
|
|
|
|
|
|
|
|
|
|
|
|
|
|
|
|
|
|
|
|
|
|
|
|
Полные остатки, |
|
9,8 |
|
23,8 |
39,8 |
|
|
60,7 |
|
81,3 |
94,9 |
|
98,3 |
|
100 |
|||||||||
|
% |
|
|
|
|
|
|
|
|
|
|
|
|
|
|
|
|
|
|
|
|
|
|
|
|
|
Минеральный порошок известняковый. Гранулометрический |
||||||||||||||||||||||||
|
состав приведен в табл. 4.3. |
|
|
|
|
|
|
|
|
|
|
|
|
|
|
|
Таблица 4.3. |
||||||||
|
|
|
|
|
|
|
|
|
|
|
|
|
|
|
|
|
|
|
|
|
|
||||
|
Показатели |
|
|
|
|
|
Размеры отверстий сит, мм |
|
|
||||||||||||||||
|
|
|
1,25 |
|
0.63 |
|
0,315 |
|
0,16 |
|
0,071 |
|
<0,071 |
||||||||||||
|
|
|
|
|
|
|
|
|
|
|
|
|
|
|
|
|
|
||||||||
|
Частные остатки, % |
|
0,9 |
|
|
2,8 |
|
|
8,2 |
|
|
8,5 |
|
|
7,6 |
|
72,0 |
||||||||
|
Полные остатки, % |
|
|
0,9 |
|
|
3,7 |
|
|
11,9 |
|
20,4 |
|
28,0 |
|
100 |
Битум вязкий дорожный марки БНД 60/90.
Подбор минеральной части асфальтобетонной смеси по предельным кривым
Зерновые составы исходных материалов записываем в табл. 4.4 (графы 2, 3, 4).
Подбор состава асфальтобетона начинаем с определения количества щебня. Исходим из того, что в 100% используемого щебня содержится 97,4 % частиц крупнее 5 мм (см. табл.4.10, а в минеральной части асфальтобетона типа Б должно содержаться таких частиц от 40 до 50 % (табл. 3 прил. 2, рис. 1 прил. 2). Приняв за необходимое количество 45 % частиц крупнее 5 мм, составляем пропорцию
100 % – 97,4 % Щ – 45 %
Щ 97,445 100 46,2%