
МУ цил.кол с заданием
.pdf4.4. Определение основной базы. При посадках с натягом зазор в сопряжении деталей отсутствует и можно было бы предположить, что зубчатое колесо всегда устанавливают на валу точно, без перекоса. Однако практика показывает, что вследствие ряда причин колесо может быть установлено на валу с перекосом.
Нельзя указать точный критерий для оценки погрешности базирования при посадках с натягом, Приближенно, из опыта принимают
при lcm /dcm 0,7 основная база - цилиндр (рис. 8, а); при lcm /dcm < 0,7 основная база - торец (рис. 8, б).
4.5. Допуски формы и допуски расположения поверхностей. На рис. 8 показаны несколько зубчатых колес и условные обозначения баз и допусков формы и расположения поверхностей. В соответствии с позициями на этом рисунке в табл. 15 даны указания по определению допусков.
Назначение каждого из допусков:
-допуск цилиндричности посадочной поверхности (поз. 1) назначают, чтобы ограничить концентрацию контактных давлений;
-допуск перпендикулярности торца ступицы (поз. 2) задают, чтобы создать точную базу для подшипника качения, уменьшить перекос его колец и искажение геометрической формы дорожки качения внутреннего кольца;
|
|
-допуск параллельности торцов ступицы узких колес (поз. 3) |
задают по тем |
|||||||||
же соображениям, как и допуск перпендикулярности торца ступицы, поз. 2. |
||||||||||||
|
|
|
|
|
|
|
|
|
|
Таблица. 15. |
||
|
|
Позиция на |
|
|
|
|
|
Допуск |
|
|
|
|
|
|
рис. 8 |
|
|
|
|
|
|
|
|
||
|
|
|
|
|
|
|
|
|
|
|
|
|
|
1 |
|
Т/О/ 0,5t , где t - допуск размера поверхности. |
|
|
|
||||||
|
|
|
|
|
|
|
|
|
|
|||
|
|
|
|
Т┴ на диаметре dст при lст /dот > 0,7 по табл. 16. Степень |
|
|||||||
|
2 |
|
точности допуска при базировании подшипников: шариковых |
|
||||||||
|
|
|
|
- 8, роликовых - 7. |
|
|
|
|
|
|
||
|
|
|
|
Т// на диаметре dст при lст /dот < 0,7 по табл. 16. Степень |
|
|||||||
|
3 |
|
точности допуска при базировании подшипников: шариковых |
|
||||||||
|
|
|
|
- 7, роликовых - 6. |
|
|
|
|
|
|
||
|
4 |
|
Т// 0,5tшп; |
Т 2 tшп , где tшп - допуск ширины шпоночного |
|
|||||||
|
|
паза. |
|
|
|
|
|
|
|
|
||
|
|
|
|
|
|
|
|
|
|
|
|
|
|
|
|
|
|
|
|
|
|
|
Таблица 16 |
||
|
|
Интервал размеров, |
Допуск параллельности, перпендикулярности, мкм, |
|
||||||||
|
|
|
|
при степени точности допуска |
|
|
|
|||||
|
|
мм |
|
|
|
|
|
|
||||
|
|
|
|
6 |
|
7 |
|
8 |
|
|
||
|
|
|
|
|
|
|
|
|
|
|||
|
|
Св. 16 до 25 |
|
6 |
|
10 |
|
16 |
|
|
||
|
|
« 25 « 40 |
|
|
|
8 |
|
12 |
|
20 |
|
|
|
|
« 40 « 63 |
|
|
|
10 |
|
16 |
|
25 |
|
|
|
|
« 63 «100 |
|
|
12 |
|
20 |
|
30 |
|
|
|
|
|
|
|
|
Таблица 8 |
|
Степень |
Твердость |
|
Значения KFv при v, м/с |
|
|
||
точности |
|
|
|
||||
зубьев колеса |
|
|
|
|
|
|
|
по |
1 |
3 |
5 |
8 |
10 |
|
|
|
|
||||||
|
> 350 НВ |
1,02 |
1,06 |
1,10 |
1,16 |
1,20 |
|
|
1,01 |
1,03 |
1,06 |
1,06 |
1,08 |
|
|
6 |
|
|
|||||
|
|
|
|
|
|
|
|
350 НВ |
1,06 |
1,18 |
1,32 |
1,50 |
1,64 |
|
|
|
|
||||||
|
1,03 |
1,09 |
1,13 |
1,20 |
1,26 |
|
|
|
|
|
|||||
|
|
|
|
|
|
|
|
|
> 350 НВ |
1,02 |
1,06 |
1,12 |
1,19 |
1,25 |
|
|
1,01 |
1,03 |
1,05 |
1,08 |
1,10 |
|
|
7 |
|
|
|||||
|
|
|
|
|
|
|
|
350 НВ |
1,08 |
1,24 |
1,40 |
1,64 |
1,80 |
|
|
|
|
||||||
|
1,03 |
1,09 |
1,16 |
1,25 |
1,32 |
|
|
|
|
|
|||||
|
|
|
|
|
|
|
|
|
> 350 НВ |
1,03 |
1,09 |
1,15 |
1,24 |
1,30 |
|
|
1,01 |
1,03 |
1,06 |
1,09 |
1,12 |
|
|
8 |
|
|
|||||
350 НВ |
1,10 |
1,30 |
1,48 |
1,77 |
1,96 |
|
|
|
|
||||||
|
1,04 |
1,12 |
1,19 |
1,30 |
1,38 |
|
|
|
|
|
|||||
|
|
|
|
|
|
|
|
|
> 350 НВ |
1,03 |
1,09 |
1,17 |
1,28 |
1,35 |
|
|
1,01 |
1,03 |
1,07 |
1,11 |
1,14 |
|
|
9 |
|
|
|||||
|
|
|
|
|
|
|
|
350 НВ |
1,11 |
1,33 |
1,56 |
1,90 |
- |
|
|
|
|
||||||
|
|
1,04 |
1,12 |
1,22 |
1,36 |
1,45 |
|
Примечание. В числителе приведены значения для прямозубых, в знаменателе для |
|
||||||
косозубых зубчатых колес. |
|
|
|
|
|
|
|
|
|
|
|
|
|
|
|
KF — коэффициент, учитывающий влияние погрешностей изготовления шестерни и колеса на распределение нагрузки между зубьями, определяют так же, как при расчетах на
контактную прочность: K |
F |
K 0 |
. |
|
H |
|
В связи с менее благоприятным влиянием приработки на изгибную прочность, чем на контактную, и более тяжелыми последствиями из-за неточности при определении напряжений изгиба приработку зубьев при вычислении коэффициентов
KF |
и KF не учитывают. |
|
|
Вместо [ ]F подставляют меньшее из значений [ ]F2 и [ ]F1. |
|
|
Допускаемые напряжения изгиба зубьев шестерни [ ]F1 |
и колеса [ ]F2 |
определяют по общей зависимости (но с подстановкой соответствующих параметров для шестерни и колеса), учитывая влияние на сопротивление усталости при изгибе долговечности (ресурса), шероховатости поверхности выкружки (переходной поверхности между смежными зубьями) и реверса (двустороннего приложения) нагрузки:
|
|
F limYNYRYA |
. |
(9) |
|
||||
F |
|
SF |
|
|
|
|
|
30 |
11 |
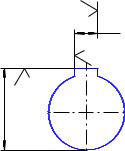
при отнулевом цикле напряжении вычисляют по эмпирическим формулам (табл. 9).
Минимальные значения коэффициента запаса прочности: для цементованных и нитроцементованных зубчатых колес - SF = 1,55; для остальных - SF =1,7.
|
|
|
|
Таблица 9 |
|
Способ термической или |
Марка |
Твердостьзубьев |
Flim, |
|
|
химикотермической |
на |
в сердцевине |
|
||
стали |
МПа |
|
|||
обработки |
поверхности |
|
|
||
|
|
|
|
||
|
|
|
|
|
|
|
45, 40Х, |
|
|
|
|
Улучшение |
40ХН, |
< 350 НВ |
< 350 НВ |
1,75НВср |
|
|
35ХМ |
|
|
|
|
|
|
|
|
|
|
Закалка ТВЧ по контуру зубьев |
40Х, 40ХН |
48-52 HRC |
27-35HRC |
600-700 |
|
Закалка ТВЧ сквозная (т< 3мм) |
35ХМ |
48-52 HRC |
48-52 HRC |
500-600 |
|
|
|
|
|
|
|
Цементация |
20Х, |
|
|
750-800 |
|
20ХН2М, |
|
|
|
||
|
|
|
|
|
|
|
18ХГТ, |
57-62 HRC |
30-45 HRC |
|
|
Цементация с автоматическим |
|
|
|||
регулированием процесса |
25ХГМ, |
|
|
850-950 |
|
|
12ХНЗА |
|
|
|
|
|
|
|
|
|
|
|
38Х2МЮА, |
|
|
12 НRCср |
|
Азотирование |
< 67 НRC |
24-40 HRC |
+ |
|
|
40ХНМА |
|
||||
|
|
|
+ 290 |
|
|
|
|
|
|
|
|
|
|
|
|
|
|
Коэффициент долговечности YN учитывает влияние ресурса,YN = 1. Коэффициент YR , учитывающий влияние шероховатости переходной
поверхности между зубьями, принимают: YR = 1 при шлифовании и зубофрезеровании с параметром шероховатости Rz 40 мкм; YR = 1,05... 1,2 при полировании (большие значения при улучшении и после закалки ТВЧ).
Коэффициент YA учитывает влияние двустороннего приложения нагрузки
(реверса). При одностороннем приложении нагрузки YA = 1. При реверсивном нагружении и одинаковых нагрузке и числе циклов нагружения в прямом и обратном направлении (например, зубья сателлита в планетарной передаче): YA = 0,65 - для нормализованных и улучшенных сталей; YA = 0,75 - для закаленных и цементованных; YA = 0,9 - для азотированных.
Из полученного диапазона (тmin ... mmах) модулей принимают меньшее значение т, согласуя его со стандартным (ряд 1 следует предпочитать ряду 2):
Ряд 1, мм……..1,0; 1,25; 1,5; 2,0; 2,5; 3,0; 4,0; 5,0; 6,0; 8,0; 10,0 Ряд 2, мм……..1,125; 1,375; 1,75; 2,25; 2,75; 3,5; 4,5; 5,5; 7,0; 9,0
Значение модулей т < 1 мм при твердости 350 НВ и т < 1,5 мм при твердости 40 HRC для силовых передач использовать нежелательно.
12
табл. 14.
|
|
|
|
|
|
|
Таблица 13 |
||
|
Интервалы размеров dom, |
|
|
|
Квалитеты |
|
|
|
|
|
|
7 |
|
8 |
|
9 |
|
|
|
|
мм |
|
|
|
|
|
|||
|
|
|
|
Ra, мкм |
|
|
|
||
|
|
|
|
|
|
|
|
||
|
Свыше 18 до 50 |
|
0,8 |
|
1,6 |
|
3,2 |
|
|
|
|
|
|
|
|
|
|
|
|
|
Свыше 50 до 120 |
|
|
1,6 |
|
3,2 |
|
|
|
|
|
|
|
|
|
|
|
|
|
|
|
|
|
|
|
|
Таблица 14. |
||
Вид поверхности |
|
|
|
|
Ra, мкм |
|
|||
Торцы ступиц зубчатых колес, базирующихся по торцу |
|
|
|
||||||
заплечиков валов, при отношении длины отверстия к диаметру |
|
|
|
||||||
lст /dот < 0,7 |
|
|
|
|
1,6 |
|
|
||
То же, при отношении lст /dот 0,7 |
|
|
|
|
3,2 |
|
|
||
Торцы ступиц зубчатых колес, по которым базируют |
|
|
|
||||||
подшипники качения |
|
|
|
|
1,6 |
|
|
||
Свободные (нерабочие) торцевые поверхности зубчатых колес |
6,3 |
|
|
||||||
Профили зубьев зубчатых колес степеней точности: |
|
|
|
||||||
6 |
|
|
|
|
|
0,4 |
|
|
|
7 |
|
|
|
|
|
0,8 |
|
|
|
8 |
|
|
|
|
|
1,6 |
|
|
|
9 |
|
|
|
|
|
3,2 |
|
|
|
Поверхности выступов зубьев колес |
|
|
|
|
6,3 |
|
|
||
Фаски и выточки на колесах |
|
|
|
|
6,3 |
|
|
||
|
|
|
|
||||||
Поверхность шпоночных пазов в отверстиях колес (рис. 7): |
|
|
|
||||||
рабочая |
|
|
|
|
1,6 |
|
|
||
нерабочая |
|
|
|
|
3,2 |
|
|
1,6 |
b |
|
|
|
1,6 |
3,2 |
|
2 |
|
+t |
|
om |
|
d |
|
Рис. 7 |
|
29 |
|
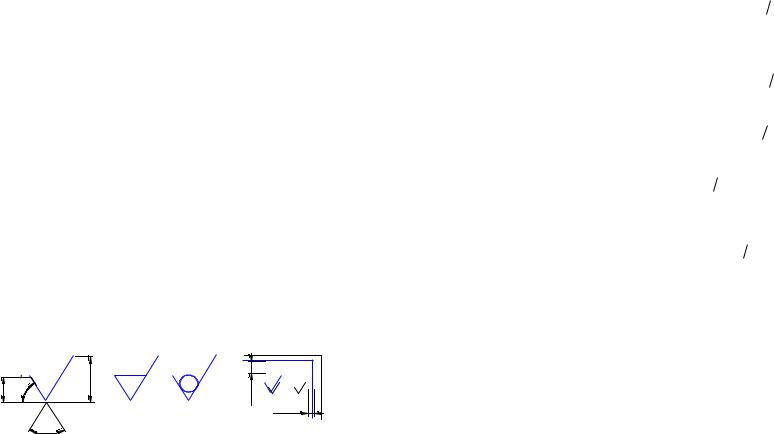
-размеры фасок f по 14 квалитету;
-толщину диска С, штамповочные радиусы и уклоны полученные в заготовительной операции (штамповке) не точнее 14 квалитета (значения штамповочных радиусов и углов можно также указывать в технических требованиях).
4.3.Обозначение шероховатости поверхностей. Из числа параметров шероховатости, установленных ГОСТ 2789—73, в машиностроении наиболее часто применяют:
Ra — среднее арифметическое отклонение профиля, мкм (основной из высотных параметров шероховатости; назначают на все обработанные поверхности);
Rz — высота неровностей профиля, мкм (определяют по пяти измерениям высот неровностей; назначают на поверхности, получаемые литьем, ковкой, чеканкой);
Для обозначения на чертежах шероховатости поверхностей применяют знаки (рис. 6, а - в). Высота h равна высоте размерных чисел на чертеже, высота H = (1,5... 3,0)h — в зависимости от объема записи.
Если вид обработки поверхности конструктор не устанавливает, то применяют знак по рис. 6, а. Это обозначение является предпочтительным. Если требуется, чтобы поверхность была образована обязательно удалением слоя материала, например точением, шлифованием, полированием и пр., применяют знак по рис. 6, б.
Если важно, чтобы поверхность была образована без удаления слоя материала (чеканка, накатывание роликами и пр.), применяют знак по рис. 6, в. Такой же знак применяют для обозначения шероховатости поверхностей, не обрабатываемых по данному чертежу.
Обозначение преобладающей шероховатости показывают в правом верхнем углу поля чертежа (рис. 6, г). Толщина линий и высота знака, заключенного в скобки, такая же, как в изображении на чертеже, а перед скобкой — в 1,5 раза больше.
h |
6 |
0 |
H |
|
|
|
60
5...10 |
6,3 |
|
( |
) |
|
|
|
|
|
5...10 |
|
а) |
б) |
в) |
г) |
|
|
Рис. 6 |
|
Обозначение |
шероховатости |
рабочих |
поверхностей зубьев колес |
(эвольвентной поверхности) наносят на линии делительной окружности. Числовое значение параметра шероховатости Ra можно принимать: для
посадочных поверхностей отверстий dom по табл. 13, для других поверхностей по
4. Суммарное число зубьев и угол наклона. Минимальный угол наклона
зубьев косозубых колес |
|
|
|
|
min arcsin 4m |
b2 ; |
(10) |
||
шевронных колес |
|
|
|
|
|
min |
25 . |
|
|
|
|
|
|
|
Суммарное число зубьев |
|
|
|
|
zS 2aw cos min |
m . |
(11) |
||
Полученное значение zS округляют в меньшую сторону до целого числа и определяют |
||||
действительное значение наклона зубьев: |
|
|
|
|
arccos zS m |
2aw . |
(12) |
||
Для косозубых колес = 8…20 , для шевронных = 25…40 . |
|
|||
5. Число зубьев шестерни и колеса. Число зубьев шестерни: |
|
|||
z1 zS |
u 1 z1min . |
(13) |
Значение z1 округляют в большую сторону до целого числа.
Для прямозубых колес z1min = 17; для косозубых и шевронных z1min = 17cos3. При z1 <
17 передачу выполняют со смещением. Коэффициент смещения |
|
x1 17 z1 17 0,6 . |
(14) |
При z1 17 можно принять х1 = 0. |
|
Коэффициент смещения для колеса х2 = -x1. |
|
Число зубьев колеса: |
|
z2 = zS - z1. |
(15) |
6. Фактическое передаточное число |
|
иф = z2 /z1. |
(16) |
Фактические значения передаточных чисел не должны отличаться от номинальных |
|
более чем на 2,5 % при и 4,5 и 4 % при и > 4,5. |
|
7. Диаметры колес (рис.1). Делительные диаметры d: |
|
шестерни |
|
d1 = z1m/cos ; |
(17) |
колеса |
|
d2 = 2аw - d1. |
(18) |
Диаметры da и df окружностей вершин и впадин зубьев для колес выполненных со смещением по формулам (19) и для колес выполненных без
смещения по формулам (19’): |
|
|
|
|
|
|
|
|
da 1 d1 2 1 x1 y m ; |
|
|||||||
d |
f 1 |
d |
1 |
2 1,25 x |
1 |
m ; |
|
|
|
|
|
|
(19) |
||||
|
|
|
|
|
|
|
|
|
da 2 d2 2 1 x2 y m; |
|
|||||||
d |
f 2 |
d |
2 |
2 1,25 x |
2 |
m . |
|
|
|
|
|
|
|
|
28 |
13 |
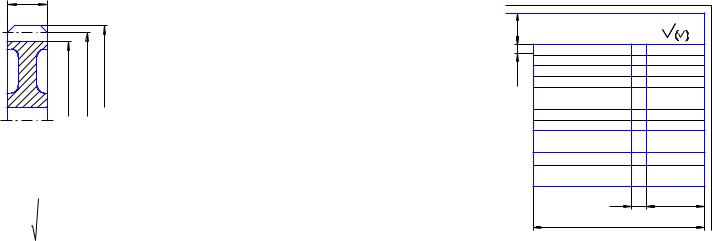
где y aw a m — коэффициент воспринимаемого смещения; а межосевое расстояние: а = 0,5m(z2 + z1).
da 1 |
d1 |
2m ; |
|
d f 1 |
d1 |
|
|
2 ,5m ; |
|||
da 2 |
d2 |
2m ; |
|
|
|||
d f 2 |
|
|
|
d2 2 ,5m . |
b |
a |
d |
d |
f |
d |
Рис.1 |
- делительное
(19’)
8. Проверка зубьев колес по контактным напряжениям. Расчетное значение контактного напряжения
|
|
|
|
|
|
|
|
|
H |
Z |
|
|
|
K H T1 uф 1 3 |
Н , |
(20) |
|
|
|
|
|
|
||||
aw |
|
|
|
|
||||
|
|
|
b2 uф |
|
где Z = 9600 для прямозубых и Z = 8400 для косозубых передач, МПа1/2.
Если расчетное напряжение Н меньше допускаемого [ ]н в пределах 15... 20 % или Н больше [ ]н в пределах 5 %, то ранее принятые параметры передачи принимают за окончательные. В противном случае необходим пересчет.
9. Силы в зацеплении (рис. 2):
окружная
F |
|
2 10 |
3 T |
|
||||
|
|
|
|
1 |
; |
(21) |
||
|
|
|
|
|
||||
t |
|
|
d1 |
|
|
|
|
|
|
|
|
|
|
|
|
||
радиальная |
|
|
|
|
|
|
|
|
Fr |
|
Ft tg |
; |
(22) |
||||
cos |
|
|||||||
|
|
|
|
|
|
|||
(для стандартного угла = 20° tg = 0,364); |
|
|
|
|
||||
осевая |
|
|
|
|
|
|
|
|
Fa |
Ft tg . |
(23) |
можно не заполнять), в третьей - справочные данные. Неиспользуемые строки исключают или ставят прочерк.
Впервой части таблицы параметров для цилиндрических колес приводят: модуль т, число зубьев z, угол наклона , направление линии зуба - правое, левое, шевронное; нормальный исходный контур со ссылкой на ГОСТ 13755-81; коэффициент смещения х; степень точности.
Вторую часть таблицы - одну - две строки оставляют свободной.
Втретьей части таблицы приводят делительный диаметр d и обозначение чертежа сопряженного колеса.
20 |
|
6,3 |
|
|
|
||
|
Модуль |
m |
|
7...10 |
Число зубьев |
z |
|
Угол наклона |
|
||
Направление линии зуба |
- |
||
|
|||
|
Нормальный исходный |
- |
|
|
контур |
||
|
|
||
|
Коэффициент смещения |
х |
|
|
Степень точности |
- |
|
|
Делительный диаметр |
d |
|
|
Обозначение чертежа |
|
|
|
сопряженного колеса |
|
|
|
10 |
35 |
|
|
110 |
|
Рис. 5
4.2. Размеры и предельные отклонения. На изображении цилиндрического зубчатого колеса должны быть указаны следующие размеры с допусками:
-ширина зубчатого венца b принимается из расчета зубчатой передачи, точность изготовления h14 если не оговариваются конструктивные особенности;
-диаметр вершин зубьев da выполняется по полям допуска h11 - для колес с модулем от 1 до 5 мм и h13 - для зубчатых колес с модулем более 5 мм. Установленный допуск не должен превышать 0,1т;
-диаметр ступицы dcm к этому размеру не выдвигается высоких требований по точности изготовления, его изготовляют с отклонением по h14;;
-длина ступицы lcm в зависимости от конструкции самой передачи, среднее значение устанавливают h12;
-диаметр отверстия dom точность изготовления этой поверхности определяет точность всей передачи, выполняется с полем отклонения Н7.
-шпоночный паз: ширина b - под шпонку для переходных посадок от JS9 до Р9, на
размер dom + t2 (см. рис. 6) при ширине шпонки b до 6 мм принимают +0,1 мм, от 6 до 32 принимают +0,2 мм;
14 |
27 |
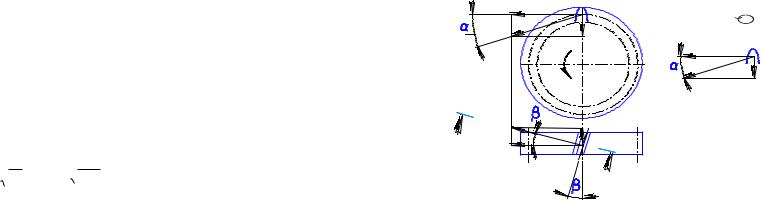
|
|
|
4Т 10 3 |
|
|
, |
(33) |
|
см |
dhl p |
см |
||||||
|
|
|
|
|
||||
|
|
|
|
|
|
|
где Т - передаваемый момент, Н м; d - диаметр вала (d = dот) , мм; lp - расчетная длина шпонки, мм; при скругленных торцах шпонки lp = l - b, при плоских торцах lp = l; [ ]см - допускаемое напряжение смятия, принимаемое при стальной ступице 150...
200, а при чугунной - 80... 110 МПа.
В последнее время передачу момента с колеса на вал все чаще осуществляют бесшпоночным соединением с натягом, методика расчета таких соединений широко приводится в различных справочных и учебных изданиях.
Пример 2. По данным примера 1 подобрать стандартную призматическую шпонку со скругленными торцами для рассчитанного колеса.
Решение. По формуле (30) определяем диаметр центрального отверстия колеса
dom 5...6 3T2 5...6 3
210 29,7...35,7 мм.
По табл. 7 принимаем диаметр отверстия dom = 32 мм.
Находим рабочую длину шпонки по формуле (33), при этом возьмем значение допускаемого напряжения смятия при стальной ступице [ ]см = 200 МПа, для центрального отверстия (вала) 32 мм по табл. 12 принимаем h = 8 мм, b = 10 мм:
l p |
4Т |
2 |
103 |
|
4 210 |
1000 |
16 ,4 |
мм |
|
dот h см |
32 8 |
200 |
|||||||
|
|
|
|
Полная длина шпонки:
l = b + lp = 10 + 16,4 = 26,4 мм.
Окончательно принимаем длину шпонки по примечанию 1 к табл. 12 l = 28 мм. Обозначение выбранной шпонки: Шпонка 10 8 28 ГОСТ 23360-78
4. Оформление рабочего чертежа
Чертеж зубчатого колеса оформляют на листах стандартного формата. Каждый чертеж должен иметь:
-таблицу параметров; -изображения детали с разрезами, необходимыми размерами, предельными
отклонениями размеров и формы, параметрами шероховатости; -основную надпись; -технические требования.
4.1. Таблица параметров. В правом верхнем углу поля чертежа приводят таблицу параметров зубчатого венца (рис. 5), данные таблицы параметров берутся из расчета зубчатой передачи.
Таблица параметров состоит из трех частей, отделенных друг от друга сплошными основными линиями. В первой части таблицы приводят данные для нарезания зубьев колес, во второй - данные для контроля (в учебных проектах эту часть
|
|
F |
t |
|
|
|
|
|
|
|
|
|
|
|
|
|
А -А |
|
|
|
F |
r |
F |
|
|
|
|
|
|
|
|
|
|
|
F |
|
|
|
|
|
r |
А |
F |
|
|
F |
a |
|
|
|
|
||
|
|
|
|
|
|
|
F |
t |
|
|
|
|
|
|
|
|
А
Рис. 2
11. Проверка зубьев колес по напряжениям изгиба. Расчетное напряжение изгиба:
в зубьях колеса
|
|
|
KF Ft |
Y |
|
Y Y |
|
|
; |
(24) |
|||||
F 2 |
|
||||||||||||||
|
|
|
|
b2 m |
|
|
FS 2 |
|
|
F 2 |
|
|
|||
|
|
|
|
|
|
|
|
|
|
|
|
|
|
|
|
в зубьях шестерни |
|
|
|
|
|
|
|
|
|
|
|
|
|
|
|
|
|
|
|
|
|
|
|
YFS 1 |
|
|
|
. |
|
(25) |
|
|
|
|
F 2 Y |
|
|||||||||||
|
|
|
F 1 |
|
|
F 1 |
|
|
|
||||||
|
|
|
|
|
|
|
|
|
FS 2 |
|
|
|
|
|
Значения коэффициента YFS, учитывающего форму зуба и концентрацию напряжений, в зависимости от числа зубьев и коэффициента смещения принимают по табл. 10.
Значение коэффициента Y , учитывающего угол наклона зуба в косозубой передаче, вычисляют по формуле ( в градусах):
Y =1- /100; при условии Y 0,7. Y - коэффициент, учитывающий перекрытие зубьев.
Для прямозубых передач: Y = 1; Y = 1 - при степени точности 8, 9; Y = 0,8 - при степени точности 5... 7.
Для косозубых передач Y = 0,65.
26 |
15 |
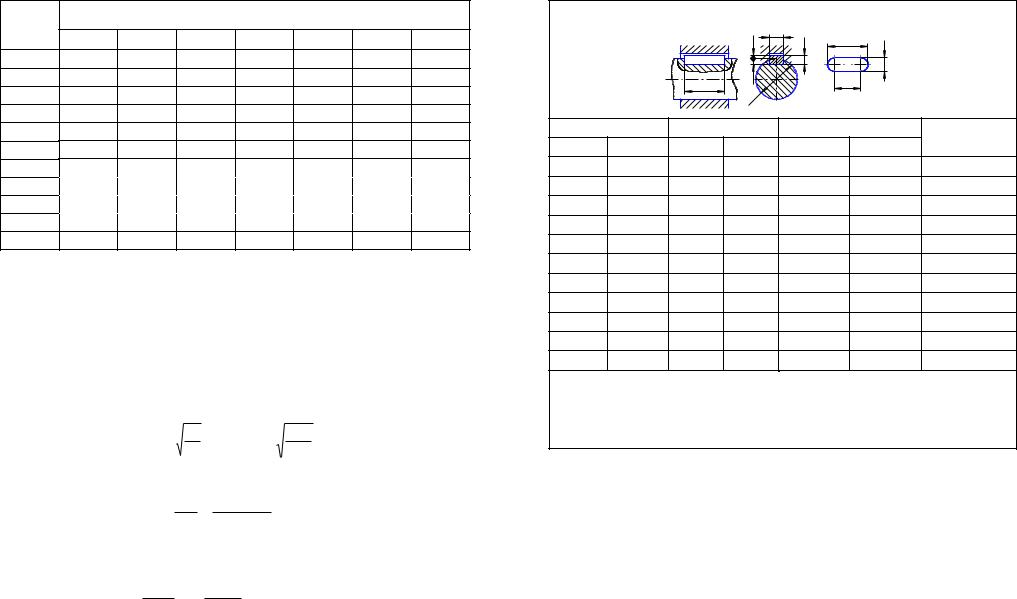
|
|
|
|
|
|
|
|
|
|
|
|
|
|
|
|
Таблица 10 |
|
|
|
|
|
|
|
|
|
|
Таблица 12 |
||
|
|
Значения YFS при коэффициенте х смещения инструмента |
|
|
|
|
Шпонки призматические (из ГОСТ 23360-78), мм |
|
|
||||||||||||||||||||
z |
|
|
|
|
|
|
|
|
|
|
|
|
|
|
|
|
|
|
|
|
|
|
|
b |
|
|
|
|
|
|
|
-0,6 |
-0,4 |
|
-0,2 |
|
0 |
|
+0,2 |
+0,4 |
|
+0,6 |
|
|
|
|
|
|
|
l |
|
|
|||||||
|
|
|
|
|
|
|
|
|
|
|
2 |
h |
|
|
|
||||||||||||||
|
|
|
|
|
|
|
|
|
|
|
|
|
|
|
|
|
|
|
|
|
|
|
t |
|
b |
|
|
||
12 |
|
|
|
|
|
|
|
|
|
|
|
|
|
|
3,67 |
|
|
|
|
|
|
|
|
|
|
|
|
|
|
14 |
|
|
|
|
|
|
|
|
|
|
|
|
4,00 |
3,62 |
|
3,30 |
|
|
|
|
l |
1 |
|
|
lp |
|
|
||
|
|
|
|
|
|
|
|
|
|
|
|
|
|
|
|
|
|
|
|
|
|
|
t |
|
|
|
|
|
|
17 |
|
|
|
|
|
|
|
|
|
|
4,30 |
3,89 |
3,58 |
|
3,32 |
|
|
|
|
|
d |
|
|
|
|
|
|||
20 |
|
|
|
|
|
|
|
|
|
|
4,08 |
3,78 |
3,56 |
|
3,34 |
|
|
|
|
|
|
|
|
|
|
|
|||
25 |
|
|
|
|
|
|
|
4,22 |
|
3,91 |
3,70 |
3,52 |
|
3,37 |
Диаметр вала d |
Сечение шпонки |
|
Глубинa паза |
Длина l |
||||||||||
|
|
|
|
|
|
|
|
|
|
|
|
|
|
|
|
|
|
||||||||||||
|
|
|
|
|
|
|
|
|
|
|
|
|
|
|
|
|
|
Свыше |
До |
|
b |
h |
вала t1 |
ступицы t2 |
|||||
30 |
|
|
|
4,38 |
|
|
4,02 |
|
3,80 |
3,64 |
3,51 |
|
3,40 |
|
|
|
|||||||||||||
40 |
|
4,37 |
|
4,06 |
|
|
3,86 |
|
3,70 |
3,60 |
3,51 |
|
3,42 |
12 |
|
17 |
|
5 |
5 |
|
3 |
2,3 |
10 56 |
||||||
60 |
|
3,98 |
|
3,80 |
|
|
3,70 |
|
3,62 |
3,57 |
3,52 |
|
3,46 |
17 |
|
22 |
|
6 |
6 |
|
3,5 |
2,8 |
14 70 |
||||||
80 |
|
3,80 |
|
3,71 |
|
|
3,63 |
|
3,60 |
3,57 |
3,53 |
|
3,49 |
22 |
|
30 |
|
8 |
7 |
|
4 |
3,3 |
18 90 |
||||||
100 |
|
3,71 |
|
3,66 |
|
|
3,62 |
|
3,59 |
3,58 |
3,53 |
|
3,51 |
30 |
|
38 |
|
10 |
8 |
|
5,5 |
3,8 |
22 110 |
||||||
200 |
|
3,62 |
|
3,61 |
|
|
3,61 |
|
3,59 |
3,59 |
3,59 |
|
3,56 |
38 |
|
44 |
|
12 |
11 |
|
7 |
4,4 |
28 140 |
||||||
Пример |
1. |
Рассчитать |
|
цилиндрическую |
закрытую |
косозубую |
|
передачу |
44 |
|
50 |
|
14 |
12 |
|
7,5 |
4,8 |
36 160 |
|||||||||||
|
|
50 |
|
58 |
|
16 |
14 |
|
9 |
5,4 |
45 180 |
||||||||||||||||||
одноступенчатого редуктора. Исходные данные: вращающий момент на валу колеса |
|
|
|
||||||||||||||||||||||||||
|
|
|
|
|
|
|
|
|
|
|
|||||||||||||||||||
Т2 = 210 Н м, угловая скорость 2 = 28 с-1, передаточное число u = 3,55. Передача не |
58 |
|
65 |
|
18 |
16 |
|
10 |
6,5 |
50 200 |
|||||||||||||||||||
реверсивная, нагрузка близка к постоянной, расположение зубчатых колес |
65 |
|
75 |
|
20 |
18 |
|
11 |
7,4 |
56 220 |
|||||||||||||||||||
симметричное. |
|
|
|
|
|
|
|
|
|
|
|
|
|
|
|
75 |
|
85 |
|
22 |
20 |
|
12 |
8,4 |
63 250 |
||||
Расчет. Для |
получения |
сравнительно |
не |
больших |
габаритных |
размеров |
|
|
|
||||||||||||||||||||
85 |
|
95 |
|
25 |
22 |
|
13 |
9,5 |
70 280 |
||||||||||||||||||||
передачи, |
выбираем |
материал |
и термическую обработку |
III группы, |
тогда для |
|
|
|
|||||||||||||||||||||
|
|
|
|
|
|
|
|
|
|
|
|||||||||||||||||||
шестерни |
и |
колеса |
будут |
одинаковыми |
материал |
и термическая |
обработка: |
Примечания: 1. Длины шпонок выбирают из ряда 10, 12, 14, 16, 18, 20, 22, 25, |
|||||||||||||||||||||
|
|
|
|
|
|
|
|
|
|
|
|||||||||||||||||||
легированная сталь 40ХН с твердостью поверхности Н1 = Н2 = 45…50 HRC. |
28, 32, 36, 40, 45, 50, 56, 63, 70, 80, 90, 100, 110, 125, 140, 160, 180, 200, 220, |
||||||||||||||||||||||||||||
250. |
|
|
|
|
|
|
|
|
|
|
|||||||||||||||||||
1. Предварительное значение межосевого расстояния по формуле (1) |
|
|
|
|
|
|
|
|
|
|
|
|
|||||||||||||||||
|
|
|
|
|
|
|
|
|
|
|
|
|
|||||||||||||||||
|
|
|
|
К и 1 3 Т1 |
6 3,55 1 3 |
61 |
|
|
|
|
2. Пример обозначения шпонки с размерами b = 18 мм, h = 16 мм, l =80 мм: |
||||||||||||||||||
|
|
|
a |
70 ,4 мм, |
|
|
«Шпонка 18 16 80 ГОСТ 23360-78» |
|
|
|
|
|
|||||||||||||||||
|
|
|
W |
|
|
|
|
и |
|
|
|
|
3,55 |
|
|
|
|
|
|
|
|
|
|
|
|
|
|
|
|
|
|
|
|
|
|
|
|
|
|
|
|
|
|
|
|
На участках крепления деталей, передающих вращающий момент, |
|||||||||||||
|
|
|
|
|
|
|
|
|
|
|
|
|
|
|
|
|
|
||||||||||||
К = 6 при Н1 |
и Н2 |
больше 45 HRC, |
|
|
|
|
|
|
|
|
|
выполняют шпоночные пазы. Размеры поперечного сечения шпонки выбираются в |
|||||||||||||||||
Т1 - вращающий момент на шестерне: |
|
|
|
|
|
|
|
|
зависимости от диаметра вала. Длина l шпонки обычно на 5 10 мм короче длины |
||||||||||||||||||||
|
|
|
|
|
Т |
|
|
Т2 |
|
210 |
61 Н м, |
|
|
|
ступицы lcm. |
|
|
|
|
|
|
|
|
|
|||||
|
|
|
|
|
1 |
|
|
|
|
|
|
Необходимость индивидуальной подгонки каждой шпонки по пазу вала |
|||||||||||||||||
|
|
|
|
|
|
|
и з |
|
3,55 0 ,97 |
|
|
|
|
|
|||||||||||||||
|
|
|
|
|
|
|
|
|
|
|
|
|
|
||||||||||||||||
здесь з - кпд зацепления, для цилиндрических зубчатых передач з = 0,96…0,98. |
затрудняет обеспечение условия взаимозаменяемости, что объясняет применение |
||||||||||||||||||||||||||||
призматических шпонок в индивидуальном и мелкосерийном производстве и |
|||||||||||||||||||||||||||||
Окружную скорость |
v, |
м/с, вычисляют |
по |
формуле |
(2) с учетом частоты |
||||||||||||||||||||||||
делает |
неэкономичным |
их |
применение |
в |
крупносерийном |
и |
массовом |
||||||||||||||||||||||
вращения шестерни п1: |
|
|
|
|
|
|
|
|
|
|
|
|
|
||||||||||||||||
|
|
|
|
|
|
|
|
|
|
|
|
|
производстве. |
|
|
|
|
|
|
|
|
|
|||||||
|
|
|
|
|
30 2 |
|
30 28 |
|
|
|
|
|
|
|
|
|
|
|
|
|
|
|
|
||||||
|
|
|
|
п1 |
и |
3,55 950 |
об/мин, |
|
|
Основным критерием работоспособности шпоночного соединения является |
|||||||||||||||||||
|
|
|
|
|
|
|
|
3,14 |
|
|
|
|
|
|
|
сопротивление смятий боковых поверхностей. |
|
|
|
||||||||||
|
|
|
|
|
|
|
|
|
|
|
|
|
|
|
|
|
|
Выбранную шпонку проверяют на смятие: |
|
|
|
16 |
25 |
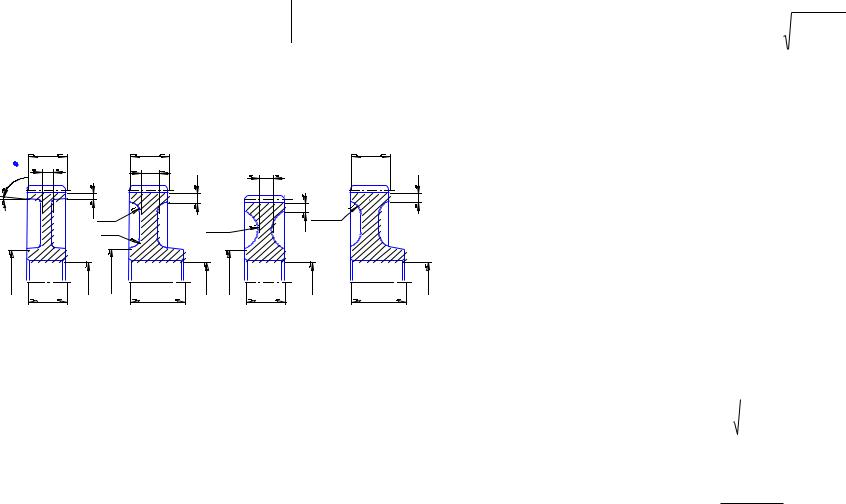
стандартного значения (см. ниже).
Острые кромки на торцах ступицы также притупляют фасками, размеры которых принимают по табл. 11:
|
|
|
|
|
|
|
|
Таблица 11 |
|
dom,мм |
20...30 |
30...40 |
40...50 |
50...80 |
80...120120 150... |
...150 250 |
250...500 |
||
f,мм |
1,0 |
1,2 |
1,6 |
2,0 |
2,5 |
3,0 |
4,0 |
|
5,0 |
|
|
||||||||
|
|
|
|
|
|
|
|
|
|
В среднесерийном, крупносерийном и массовом производствах заготовки колес |
|||||||
получают из прутка свободной ковкой, а также ковкой в штампах. Форму зубчатых |
|||||||
колес в этом случае проектируют по рис. 4, а, б. Для свободной выемки заготовок из |
|||||||
штампа принимают значения штамповочных уклонов 5…7° и радиусов закруглений |
|||||||
R 6 мм. Толщина диска |
|
|
|
|
|||
|
С 0,5(S + Scm) 0,25b2, где Scm = 0,5(dcm - dom). |
(32) |
|||||
|
b |
|
b |
|
|
|
b |
7 |
C |
|
C |
|
C |
|
|
. |
|
|
|
|
|
|
|
. |
|
|
|
|
|
|
|
. |
|
|
|
S |
|
|
S |
5 |
|
|
|
|
|
||
|
|
S |
R |
|
|
R10 |
|
|
|
|
R |
R |
|
S |
|
|
|
|
1 |
|
|
|
|
cm |
|
om |
cm |
cm |
|
om |
om |
d |
|
d |
om d |
|
|||
|
lcm = b |
d |
lcm |
d |
lcm = b |
d |
d |
|
|
|
|
lcm |
а) |
б) |
в) |
г) |
Рис. 4
Условия пластического деформирования металла при штамповке улучшены, если выемки в дисках колес выполнять по рис. 4, в, г. Радиусы закруглений принимают R1 20 мм, штамповочные уклоны 12 и больше, толщина диска С =
(0,4 0,5)b.
3. Соединения вал - ступица
Для закрепления на валах деталей, передающих момента вращения, с детали на вал и наоборот применяют конструктивные решения в виде шпоночных, штифтовых, профильных и с гарантированным натягом.
Из перечисленных разновидностей наиболее простыми являются соединения призматическими шпонками (табл. 1 2). Они имеют прямоугольное сечение и изготовляются из цельнотянутой стали.
|
2 a |
n |
2 3,14 70 ,4 950 |
|
|
v |
W |
1 |
|
|
1,54 м/с. |
6 104 u 1 |
6 104 3,55 1 |
При v = 1,54 м/с по табл.2 назначаем 9 степень точности, пст = 9. Уточненное значение межосевого расстояния по формуле (3):
aW Ka u 1 3 |
K H T1 |
, |
ba u 2H |
здесь ba = 0,315 - коэффициент ширины, при симметричном расположении колес (по условию) и Н 45 HRC.
|
KH = KHvKH KH = 1,01 1,04 1,38 = 1,45 |
||||
KHv= 1,01 по табл. 3. |
|
1 K 0 |
1 K |
|
1 1,07 1 0,63 1,04 |
K |
H |
HW |
|||
|
H |
|
|
К0 = 1,07 по табл. 4, для 6 схемы при найденном bd:
Н
bd 0,5 ba u 1 0,5 0,315 3,55 1 0,72
KHW = 0,63 по табл. 5. |
1 K 0 |
1 K |
|
1 1,6 1 0,63 1,38 , |
|
K |
H |
HW |
|||
|
H |
|
|
К0 1 А( п 5 ) 1 0,15 9 - 5 1,6 .
Н СТ
Допускаемое контактное напряжение по формуле (4)
|
Н lim Z N ZR Zv |
|
1007 ,5 1 1 1 |
915 ,9 МПа, |
|
||||
Н |
SH |
1,1 |
|
|
|
|
где Hlim предел контактной выносливости по табл. 6:
Hlim = 17 HRCcp + 200 = 17 47,5 + 200 = 1007,5 МПа
SH = 1,1;
ZN = 1;
ZR =1; Zv =1.
a 410 3,55 1 3 |
|
1,45 61 |
|
84 ,97 мм, |
|
0 ,315 3,55 915 ,92 |
|||||
W |
|
|
Принимаем аW = 85 мм (табл. 7).
2. Предварительные основные размеры колеса делительный диаметр по формуле (5):
d2 2 85 3,55 132,64 мм. 3,55 1
Ширина колеса по формуле (6):
b2 = φbaaW = 0,315 85 = 26,77 мм.
Принимаем b2 = 28 мм (табл. 7).
24 |
17 |
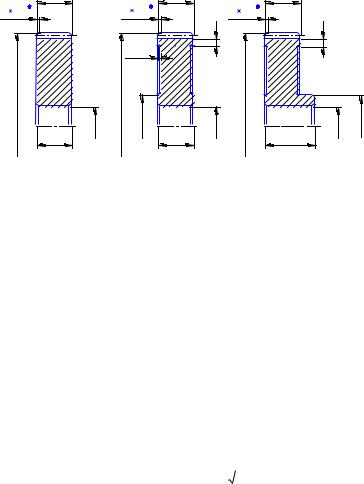
|
|
3. Модуль передачи. Максимально допустимый модуль по формуле (7) |
|||||||||
|
|
|
|
mmax |
2aw |
|
|
|
2 85 |
|
2,19 мм. |
|
|
|
|
17( u 1 ) |
17( 3,55 |
1 ) |
|||||
|
|
|
|
|
|
|
|||||
|
|
Минимальное значение модуля по формуле (8) |
|
|
|||||||
|
|
|
|
|
mmin |
Km KF T1 ( u 1 ) |
, |
|
|||
|
|
|
|
|
|
|
aw b2 F |
|
|||
|
|
|
|
|
|
|
|
|
|
||
Кт = 2,8 103. |
|
|
|
|
|
|
|
|
|||
|
|
|
|
KF = KFvKF KF =1,01 1,06 1,6 = 1,71 . |
|||||||
KFv = 1,01 по табл. 8. |
|
|
|
|
|
|
|
|
|||
K |
F |
0,18 0,82K 0 |
0,18 0,82 1,07 |
1,06 . |
|
|
|||||
|
|
H |
|
|
|
|
|
|
|
|
|
K |
F |
K 0 |
1,6 . |
|
|
|
|
|
|
|
|
|
H |
|
|
|
|
|
|
|
|
|
Допускаемые напряжения изгиба зубьев шестерни [ ]F1 и колеса [ ]F2 будут равны друг другу, т.к. шестерня и колесо выполнены из одного материала с одинаковой термической обработкой, т.е. [ ]F1 = [ ]F2 = [ ]F, тогда по (9)
|
|
|
F limYNYRYA |
. |
700 1 1 1 |
411,76 МПа, |
|||
F |
|
|
SF |
1,7 |
|
|
|||
|
|
|
|
|
|
||||
Flim = 700 МПа, по табл. 9. |
|
|
|
|
|
||||
SF = 1,7. |
|
|
|
|
|
|
|
|
|
YN = 1. |
|
|
|
|
|
|
|
|
|
YR = 1. |
|
|
|
|
|
|
|
|
|
YA = 1. |
|
|
|
|
|
|
|
|
|
m |
|
|
|
2,8 10 |
3 1,71 61 ( 3,55 1 ) |
1,35 мм. |
|||
min |
|
85 28 411,76 |
|||||||
|
|
|
|
||||||
|
|
|
|
|
|
Принимаем т = 1,5 мм.
4. Минимальный угол наклона зубьев косозубых колес по формуле (10)
|
|
|
|
|
|
|
|
|
|
|
|
|
|
|
|
4 1,5 |
|
|
|
||
|
|
|
|
|
|
|
|
|
4т |
|
|
|
|
|
|
|
|
||||
min |
arcsin |
|
|
|
|
|
arcsin |
|
12,37 . |
||||||||||||
|
b2 |
|
|
||||||||||||||||||
|
|
|
|
|
|
|
|
|
|
|
|
|
|
28 |
|
|
|
||||
Суммарное число зубьев по формуле (11) |
|
|
|
|
|
|
|||||||||||||||
z |
|
|
2a |
w |
cos |
min |
|
|
|
2 85 cos 12,37 |
110 ,7 . |
||||||||||
|
|
|
|
|
|
|
|
|
|
|
|
|
|
||||||||
S |
|
|
m |
|
|
|
|
|
1,5 |
|
|
|
|||||||||
|
|
|
|
|
|
|
|
|
|
|
|
|
|
|
|||||||
|
|
|
|
|
|
|
|
|
|
|
|
|
|
|
|
||||||
Принимаем zS = 110. |
|
|
|
|
|
|
|
|
|
|
|
|
|
|
|
|
|
|
|
|
|
Действительное значение наклона зубьев по формуле (12) |
|
||||||||||||||||||||
|
|
|
|
|
z |
S |
m |
|
|
|
110 1,5 |
|
|
||||||||
arccos |
|
|
|
|
arccos |
|
|
|
|
13,93 . |
|||||||||||
|
|
|
|
|
|
|
|||||||||||||||
|
|
|
|
|
|
|
|
|
|
|
|
|
|
|
2 85 |
|
|
|
|
||
|
|
|
|
|
|
2aw |
|
|
|
|
|
|
мелкосерийном производстве. При небольших диаметрах колес их изготовляют из прутка, а при больших - заготовки получают свободной ковкой с последующей токарной обработкой. Чтобы уменьшить объем точной обработки резанием, на дисках колес выполняют выточки от 1 до 2 мм (рис. 3, б, в). При диаметре dа < 80 мм эти выточки, как правило, не делают (рис. 3, а).
|
b |
|
|
b |
|
f |
45 |
|
f |
45 |
|
|
|
|
|
|
S |
|
|
|
1...2 |
|
|
a |
|
|
a |
|
|
d |
|
|
d |
|
|
|
|
от |
cm |
от |
|
|
|
d |
|
||
|
|
d |
|
|
d |
|
lcm = b |
|
|
lcm = b |
|
|
b |
|
f |
45 |
|
|
S |
|
a |
|
|
d |
|
|
|
от |
cm |
|
d |
|
|
d |
|
|
lcm |
|
а) |
б) |
в) |
|
Рис. |
3 |
Длину lcт посадочного отверстия колеса желательно принимать равной или больше ширины b2 зубчатого венца (lcт b2). Принятую длину ступицы согласуют с расчетной (см. расчет соединения вал - ступица шлицевого, с натягом или шпоночного, выбранного для передачи вращающего момента с колеса на вал) и с диаметром посадочного отверстия dom:
|
lcт = (0,8...1,5)dom , обычно lcт = (1,0...1,2) dom. |
(26) |
При lcт > b2 |
выступающую часть ступицы располагают по направлению действия |
|
осевой силы Fа в зацеплении. |
|
|
Диаметр dсm назначают в зависимости от материала ступицы для: |
|
|
стали |
dсm = (1,5...1,55) dom; |
(27) |
чугуна |
dсm = (1,55...1,6) dom; |
(28) |
легких сплавов dсm = (1,6... 1,7) dom, |
(29) |
меньшие значения для шлицевого соединения колеса с валом, большие - для шпоночного и соединения с натягом.
Диаметр dom посадочного отверстия принимается в зависимости от передаваемого
момента Т: |
|
||
dom 5...6 3 |
|
. |
(30) |
T |
|||
Ширину S торцов зубчатого венца принимают: |
|
||
S= 2,2т + 0,05 b2, |
(31) |
||
где т - модуль зацепления, мм. |
|
||
На торцах зубчатого венца (зубьях и углах обода) выполняют фаски: |
|||
f=(0,5...0,6)т, которые округляют в зависимости от диаметра отверстия |
dom до |
18 |
23 |
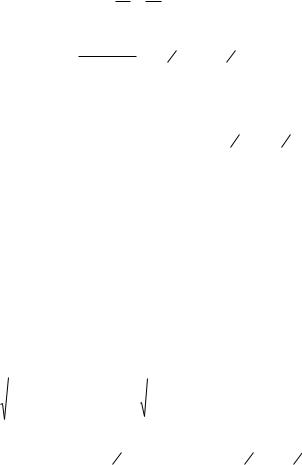
Параметры рассчитанной передачи
Параметр |
Значение |
Момент на ведомом валу Т2, Н м |
210 |
Частота вращения вала, мин-1: |
|
ведущего п1 |
950 |
ведомого п2 |
265,4 |
Угловая скорость вала рад/с: |
|
ведущего 1 |
100,24 |
ведомого 2 |
28 |
Передаточное число и |
3,58 |
Материал зубчатых колес: |
|
шестерни |
Сталь 40Х |
колеса |
Сталь 40Х |
Твердость зубьев: |
|
шестерни |
45…50 HRC |
колеса |
45…50 HRC |
Тип передачи |
Косозубая |
Угол наклона зубьев |
13,93 |
Направление зубьев: |
|
шестерни |
Правое |
колеса |
Левое |
Межосевое расстояние aw, мм |
85 |
Число зубьев: |
|
шестерни z1 |
24 |
колеса z2 |
84 |
Модуль зацепления т, мм |
|
Диаметры делительных окружностей, мм: |
|
шестерни d1 |
37,11 |
колеса d2 |
132,89 |
Силы действующие в зацеплении, Н: |
|
окружная Ft |
3287,5 |
радиальная Fr |
1233,7 |
осевая Fa |
815,4 |
2. Конструкции цилиндрических зубчатых колес
Конфигурация зубчатого колеса в определенной степени зависит от технологии получения заготовки, которая находится в тесной взаимосвязи с объемом выпуска изделия.
На рис. 3 показаны простейшие формы колес, изготовляемых в единичном и
5. Число зубьев шестерни по (13)
z1 |
|
zS |
|
|
110 |
24 ,17 . |
|
u |
1 |
3,55 1 |
|||||
|
|
|
|
Принимаем z1 = 25.
Коэффициент смещения для шестерни и колеса х1 = x2 = 0. Число зубьев колеса по формуле (15)
z2 = zS - z1 = 110 - 25 = 85.
6. Фактическое передаточное число по формуле (16)
иф z2 85 3,4 . z1 25
Отклонение и фактического передаточного числа иф от заданного и
и 3,4 3,55 100 0 0 4 ,22 0 0 ,
3,55
Условие и < 2,5 % не выполняется. Производим перерасчет.
Принимаем новые значения чисел зубьев для шестерни и колеса оставляя суммарное
значение зубьев: z1 = 24 и z2 = 86, тогда иф |
и |
и: |
|
|
|
|
|
|
|
|
|
||||||||||||||||
|
|
и |
|
|
86 |
3,58 и |
и |
|
3,58 3,55 |
100 |
0 |
0 ,94 0 |
. |
||||||||||||||
|
|
ф |
24 |
|
|
|
|
|
|
|
|
|
|
|
|
3,55 |
|
|
0 |
|
0 |
|
|||||
|
|
|
|
|
|
|
|
|
|
|
|
|
|
|
|
|
|
|
|
|
|
|
|
||||
Принимаем z1 = 24 и z2 = 86. |
|
|
|
|
|
|
|
|
|
|
|
|
|
|
|
|
|
|
|
|
|
||||||
7. Делительные диаметры |
|
|
|
|
|
|
|
|
|
|
|
|
|
|
|
|
|
|
|
|
|
||||||
шестерни по формуле (17) |
|
|
|
|
|
|
|
|
|
|
|
|
|
|
|
|
|
|
|
|
|
||||||
|
|
|
|
|
|
d1 |
z1m |
|
|
|
|
24 1,5 |
37 ,11 мм; |
|
|
|
|
|
|||||||||
|
|
|
|
|
|
cos |
|
0 ,97 |
|
|
|
|
|
||||||||||||||
|
|
|
|
|
|
|
|
|
|
|
|
|
|
|
|
|
|
||||||||||
колеса по формуле (18) |
|
|
|
|
|
|
|
|
|
|
|
|
|
|
|
|
|
|
|
|
|
||||||
|
|
|
|
|
d2 = 2аw - d1 = 2 85 - 37,11 = 132,89 мм. |
|
|
|
|
||||||||||||||||||
Диаметры da окружностей вершин и df |
впадин зубьев по формулам (19’): |
||||||||||||||||||||||||||
|
|
|
|
|
da1 = d1 + 2m = 37,11 + 2 1,5 = 40,11 мм, |
|
|
|
|
||||||||||||||||||
|
|
|
|
|
df1 = d1 - 2,5m = 37,11 - 2,5 1,5 = 29,61 мм, |
|
|||||||||||||||||||||
|
|
|
|
|
da2 = d2 + 2m = 132,89 + 2 1,5 = 135,89 мм, |
|
|||||||||||||||||||||
|
|
|
|
df2 = d2 - 2,5m = 132,98 - 2,5 1,5 = 129,14 мм. |
|
||||||||||||||||||||||
8. Расчетное значение контактного напряжения по формуле (20) |
|
||||||||||||||||||||||||||
|
|
|
|
|
|
|
|
|
|
|
|
|
|
||||||||||||||
|
|
|
|
K H T1 uф 1 3 |
|
|
|
|
|
|
|||||||||||||||||
H |
Z |
|
|
|
8400 |
|
1,45 61 3,58 1 3 |
931,6 МПа. |
|||||||||||||||||||
|
|
|
|
|
|
|
|
|
|
|
|
|
|
|
|
|
|
|
|
|
|
|
|||||
aw |
|
|
|
b2 uф |
|
|
|
|
|
85 |
|
|
|
|
28 3,58 |
|
|
|
|
||||||||
|
|
|
|
|
|
|
|
|
|
|
|
|
|
|
|
|
|
|
|
||||||||
Проверяем превышение расчетного значения Н от допустимого [ ]H |
|||||||||||||||||||||||||||
|
|
|
Н Н 100 |
0 |
|
931,6 915 ,9 |
100 |
0 |
1,71 |
0 |
|||||||||||||||||
|
Н |
|
|||||||||||||||||||||||||
|
|
|
|
|
Н |
|
|
|
|
|
|
0 |
|
|
|
|
915,9 |
|
|
|
0 |
|
|
|
0 |
||
|
|
|
|
|
|
|
|
|
|
|
|
|
|
|
|
|
|
|
|
|
|
|
|
|
22 |
19 |
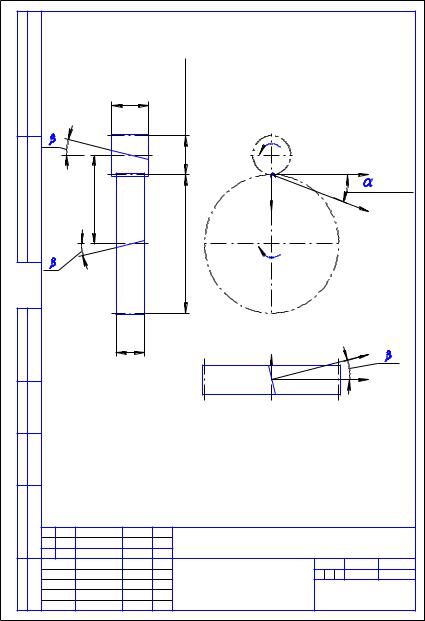
Расчетного значения Н не превышает 5%, ранее принятые параметры передачи принимаем за окончательные.
9. Силы в зацеплении по формулам (21), (22), (23):
|
F |
|
2 10 |
3 T |
|
2 103 |
61 |
3287 ,5 |
|
|||
окружная |
|
|
1 |
|
|
|
Н; |
|||||
|
|
|
|
|
|
|||||||
|
t |
|
|
d1 |
|
|
|
37 ,11 |
|
|
|
|
|
|
|
|
|
|
|
|
|
|
|||
радиальная |
Fr |
|
Ft tg |
|
|
3287 ,5 0 ,364 |
1233,7 |
Н; |
||||
cos |
|
|
0 ,97 |
|
|
|||||||
|
|
|
|
|
|
|
|
|
|
|||
осевая |
Fa |
Ft tg |
3287 ,5 0,248 815,4 Н. |
Пример оформления расположения сил показан на стр. 21.
11.Проверка зубьев колес по напряжениям изгиба.
взубьях колеса по формуле (24)
|
|
|
|
|
K F Ft |
Y |
|
|
Y Y |
|
|
1,71 3287 ,5 |
3,6 0 ,86 0 ,65 269 МПа, |
||||
|
|
F 2 |
|
b2 m |
FS 2 |
|
|
28 1,5 |
|||||||||
|
|
|
|
|
|
|
|
|
|
||||||||
YFS2 = 3,6 по табл. 10; |
|
|
|
|
|
|
|
|
|
|
|||||||
Y 1 |
|
|
1 |
13,93 |
|
0 ,86 ; |
|
|
|
|
|
|
|||||
|
|
|
|
|
|
|
|
|
|
||||||||
|
100 |
|
|
100 |
|
|
|
|
|
|
|
|
|
|
|||
|
|
|
|
|
|
|
|
|
|
|
|
|
|||||
Y = 0,65. |
|
|
|
|
F |
|
|
|
|
|
|
|
|
|
|
||
Условие F 2 |
|
выполнено. |
|
|
|
|
|||||||||||
в зубьях шестерни по формуле (25) |
|
|
|
|
|||||||||||||
|
|
|
|
|
|
|
|
|
|
|
YFS 1 |
269 |
3,91 |
292 МПа, |
|||
|
|
|
|
|
|
|
|
|
F 1 |
|
F 2 |
Y |
3,6 |
|
|||
|
|
|
|
|
|
|
|
|
|
|
|
|
|||||
|
|
|
|
|
|
|
|
|
|
|
|
|
FS 2 |
|
|
|
|
YFS1 = 3,91 по табл. 10. |
|
|
|
|
|
|
|
|
|
|
|||||||
Условие F 1 |
F |
выполнено. |
|
|
|
|
Все выбранные геометрические параметры зубчатой передачи соответствуют условиям прочности.
20
н. |
|
|
|
|
|
|
|
|
Перв. приме |
|
|
b1 |
=37,11 |
|
|
|
|
|
|
|
|
|
|
|
||
|
|
|
|
1 |
|
|
|
|
|
|
|
|
d |
|
|
|
|
|
|
|
|
|
Ft |
|
|
|
|
|
=85 |
|
|
|
|
= 20 |
o |
№ |
|
|
|
|
|
|
||
|
|
Fr |
|
|
|
|
||
правС . |
|
w |
|
2,89 |
|
|
|
|
|
a |
|
|
Fn |
|
|
||
|
|
|
|
=13 |
|
|
|
|
|
|
|
|
2 |
|
|
|
|
|
|
|
|
d |
|
|
|
|
и дата |
|
|
b2 |
Fа |
|
F |
|
|
одп. |
|
|
|
|
n |
|
|
|
|
|
|
|
|
|
|
||
П |
|
|
|
|
|
|
|
|
убл. |
|
|
|
|
|
Ft |
|
|
в. № д |
|
Си лы: |
|
|
|
|
|
|
Ин |
|
|
|
|
|
|
|
|
. № |
|
окружн ая Ft = 3287,5 Н ; |
|
|
|
|
||
инв |
|
ради альн ая Fr = 1233,7 Н ; |
|
|
|
|
||
Взам. |
|
|
|
|
|
|||
|
осевая |
|
Fа = 815,4 Н . |
|
|
|
|
|
Подп. и дата |
|
|
|
ПР-расчет зубчатых передач |
|
|||
|
Изм.Л ист № докум. |
Подп. |
|
|||||
подл. |
Д ата |
|
|
|
|
|||
Разраб. |
|
|
|
Лит. |
Лист |
Листов |
||
Пров. |
|
|
Схема расположения сил |
|
|
1 |
|
|
№ |
|
|
|
|
|
|
|
|
Инв. |
Н.контр. |
|
|
|
гр. ___ |
|
||
|
|
|
|
|
||||
Утв. |
|
|
|
|
|
|
|
|
|
|
|
|
|
|
|
|
|
|
|
|
|
Копировал |
Формат |
A4 |
|
|
|
|
|
|
21 |
|
|
|
|