
МВ до викон. інд. завдання (укр)
.pdf
11
де – кількість деталей у групі;
2.3.4. підрахувати
∑ ( гр ∙ );
2.3.5. визначити середньоарифметичний розмір
= ∑ ( гр∙ ); (2.6)
сер |
∑ |
|
2.3.6. визначити відхилення середнього розміру в групі від середньоарифметичного розміру
гр − сер;
2.3.7. підрахувати квадрат відхилення від середньоарифметичного розміру
( гр − сер)2;
2.3.8. підрахувати суму
∑ (( гр − сер)2 ∙ );
2.3.9.визначити середньоквадратичне відхилення за формулою (2.4.);
2.3.10.побудувати графік фактичного розподілу деталей по розмірах у партії за даними табл. 2.1, відкладаючи по осі абсцис ( )
середній розмір в групі гр, а по осі ординат ( ) – кількість
деталей у групі; відзначити розташування поля допуску й поля розсіювання;
Таблиця 2.1. – Статистичні характеристики партії деталей
|
Початкові дані |
|
|
|
|
|
Розрахункові дані |
|
|
|
|
|
||||
|
|
|
|
|
|
|
|
|
|
|
|
|||||
№ |
Інтервали |
Кількість |
Середній |
|
|
|
Відхилення від |
Квадрат |
|
Добуток |
||||||
деталей у |
розмір у |
Добуток |
середньоарифмет |
відхилення |
|
|
|
|||||||||
|
( гр − |
|||||||||||||||
|
розмірів |
|||||||||||||||
розмірної |
|
групі |
партії |
|
∙ |
|
ичного розміру, |
( гр − |
|
|||||||
групи |
|
, мм |
|
|
р, мм |
гр |
|
|
|
− , мм |
|
2 |
2 |
сер) |
2 |
∙ |
|
|
, шт. |
|
|
|
|
|
|
||||||||
|
|
гр |
|
|
|
гр |
сер |
сер) , мм |
|
|
|
|||||
|
|
|
|
|
|
|
|
|
||||||||
1 |
|
|
|
|
|
|
|
|
|
|
|
|
|
|
|
|
|
|
|
|
|
|
|
|
|
|
|
|
|
|
|
|
|
2 |
|
|
|
|
|
|
|
|
|
|
|
|
|
|
|
|
|
|
|
|
|
|
|
|
|
|
|
|
|
|
|
|
|
3 |
|
|
|
|
|
|
|
|
|
|
|
|
|
|
|
|
|
|
|
|
|
|
|
|
|
|
|
|
|
|
|
|
|
4 |
|
|
|
|
|
|
|
|
|
|
|
|
|
|
|
|
|
|
|
|
|
|
|
|
|
|
|
|
|
|
|
|
|
5 |
|
|
|
|
|
|
|
|
|
|
|
|
|
|
|
|
|
|
|
|
|
|
|
|
|
|
|
|
|
|
|
|
|
6 |
|
|
|
|
|
|
|
|
|
|
|
|
|
|
|
|
|
|
|
|
|
|
|
|
|
|
|
|
|
|
|
|
|
7 |
|
|
|
|
|
|
|
|
|
|
|
|
|
|
|
|
|
|
|
|
|
|
|
|
|
|
|
|
|
|
|
|
|
8 |
|
|
|
|
|
|
|
|
|
|
|
|
|
|
|
|
|
|
|
|
|
|
|
|
|
|
|
|
|
|
|
|
|
9 |
|
|
|
|
|
|
|
|
|
|
|
|
|
|
|
|
|
|
|
|
|
|
|
|
|
|
|
|
|
|
|
|
|
10 |
|
|
|
|
|
|
|
|
|
|
|
|
|
|
|
|
|
|
|
|
|
|
|
|
|
|
|
|
|
|
|||
|
|
|
∑ |
= 100 |
|
∑ = |
|
|
|
|
|
|
∑ = |
|||
|
|
|
|
|
|
|
|
|
|
|
|
|
|
|
|
|
|
|
|
|
|
|
|
|
|
|
|
|
|
|
|||
|
|
|
|
|
|
|
|
|
|
|
|
|
|
|
|
|
13
2.3.11. підрахувати координати п'яти характерних точок кривої нормального розподілу (табл. 2.2) і побудувати криву нормального розподілу по п'ятьом характерним точкам (рис. 2.1). Криву нормального розподілу побудувати на графіку фактичного розподілу,
при цьому необхідно знайти положення сер, якому буде відповідати значення 3 і максимальне значення 3.
Таблиця 2.2. – Координати характерних точок кривої нормального розподілу
№ точки |
|
|
|
|
|
|
|
|
|
|
|
|
|
||
|
|
|
|
|
|
|
|
|
|
|
|
|
|
||
1 |
1 |
= −3 |
|
|
1 = 0 |
||
|
|
|
|
|
|||
2 |
2 = − |
|
2 |
= 0.24⁄ |
|||
|
|
|
|
|
|
|
|
3 |
|
3 |
= 0 |
|
= |
= 0.4⁄ |
|
|
|
|
3 |
|
|
|
|
|
|
|
|
|
|
||
4 |
4 |
= |
|
4 |
= 0.24⁄ |
||
|
|
|
|
|
|
||
5 |
5 |
= 3 |
|
|
5 = 0 |
||
|
|
|
|
|
|
|
|
2.3.12. для визначення ймовірності одержання браку треба розрахувати значення допоміжних величин Z1 і Z2
|
|
|
= |
|
′ |
− |
||
|
|
|
|
сер, |
||||
|
|
1 |
|
|
|
|
|
|
|
|
|
|
|
|
|||
|
|
|
|
′ |
− |
|||
|
|
|
= |
|
|
сер |
, |
|
|
|
|
|
|
||||
|
|
2 |
|
|
|
|
||
|
|
|
|
|
|
|||
де ′ |
– найменший граничний розмір; |
|
|
|
||||
|
|
|
|
|
|
|
|
|
′ |
|
– найбільший граничний розмір; |
||||||
|
|
|
|
|
|
|
|
2.3.13.по табл. Б2 (додаток Б) визначити значення величин Ф1 і Ф2;
2.3.14.по величинах Ф1 і Ф2 визначити ймовірність одержання
браку:
Р1 – з меншими розмірами, чім у завданні;
14
Р2 – з більшими розмірами, чім у завданні:
Р1 = 0.5 − Ф1,
Р2 = 0.5 − Ф2,
2.3.15.визначити можливий брак у відсотках
Р= (Р1 + Р2) ∙ 100%,
2.3.16.визначити відсоток придатних деталей
= 100% − Р.
Примітка. Значення 0 для Ф опущене.
Приклад: Z = 2,71; Ф = 0,4966.
2.4. Контрольні питання
1.Що розуміється під точністю в машинобудуванні?
2.Що визначає точність деталі, отриманої в результаті механічної обробки?
3.Фактори, що впливають на точність механічної обробки.
4.Систематичні похибки. Характер систематичних похибок.
5.Випадкові похибки. Крива нормального розподілу.
6.Міра розсіювання, середньоарифметичний розмір і середньоарифметичне відхилення.
7.Імовірність одержання браку. Поправний і непоправний брак.
15
3. РОЗРАХУНОК ПРИПУСКІВ НА МЕХАНІЧНУ ОБРОБКУ
Мета роботи: визначення припусків на обробку розрахунковоаналітичним методом.
3.1.Загальні відомості
Заготовки, що призначені для механічної обробки, мають припуск на обробку.
Припуском називається шар матеріалу, що видаляється в процесі механічної обробки заготовки з метою забезпечення необхідної точності і якості обробленої поверхні деталі.
Припуски розділяються на проміжні й загальні.
Проміжний припуск – шар матеріалу, що видаляється при виконанні одного технологічного переходу.
Загальний припуск – шар матеріалу, необхідний для виконання всіх технологічних переходів при обробці даної поверхні. Загальний припуск дорівнює сумі всіх проміжних припусків для даної поверхні.
Величину припуску можна визначити двома методами:
дослідно-статистичним (по довідкових таблицях);
розрахунково-аналітичним.
Дослідно-статистичний метод визначення припусків не враховує конкретних умов обробки, дає завищені величини припусків, однак скорочує час на розрахунок припусків. Цей метод використовують в одиничному й дрібносерійному виробництвах.
У великесерійному і масовому виробництвах використовують розрахунково-аналітичний метод визначення припусків, який дозволяє розрахувати мінімальний проміжний припуск, забезпечує економію матеріалу, сприяє підвищенню технологічної культури виробництва.
3.2.Розрахунково-аналітичний метод визначення припусків
Розрахунково-аналітичний метод базується на аналізі виробничих похибок, що виникають при конкретних умовах обробки.
Розрахунок проміжних припусків проводиться по всіх послідовно виконуваних технологічних переходах обробки даної поверхні. Загальний припуск визначається підсумовуванням проміжних припусків. Розрахунковою

16
величиною є мінімальний припуск на обробку, достатній для усунення на виконуваному переході похибок обробки й дефектів поверхневого шару, що отримані на попередньому переході, а також компенсації похибок, що виникають на виконуваному переході. Проміжні розміри по переходах і розмір заготовки розраховують із використанням мінімального припуску.
Мінімальний проміжний припуск
|
= ( |
; |
; |
; |
), |
(3.1) |
|
−1 |
−1 |
−1 |
|
|
|
де −1 – висота мікронерівностей поверхні, що отримана на попередньому переході;
−1 – глибина дефектного поверхневого шару, що отримана на попередньому переході;
−1 – сумарні відхилення розташування поверхонь (просторові відхилення), що отримані на попередньому переході;
– похибка установки заготовки на виконуваному переході.
При обробці зовнішніх і внутрішніх циліндричних поверхонь
2 ∙ |
= 2 ∙ ( |
+ |
+ √ 2 |
+ 2 ), |
|
−1 |
−1 |
−1 |
|
Розрахунок мінімальних проміжних припусків виконується для переходів обробки заданої поверхні в порядку, зворотному технологічного процесу, тобто від останнього переходу до початкового.
(3.2)
всіх
ходу
Для зручності визначення проміжних припусків і проміжних розмірів розрахункові дані записують у допоміжну таблицю.
3.3.Порядок розрахунку
3.3.1.По робочому кресленню деталі й карті технологічного процесу механічної обробки записати в розрахункову таблицю всі технологічні переходи обробки даної поверхні від чорнової до остаточної обробки.
3.3.2.Визначити й записати значення Rz, T, ρ, εy.
17
3.3.3.Визначити розрахункові величини проміжних припусків по всіх технологічних переходах за формулою (3.2).
3.3.4.Визначити кінцевий граничний розмір оброблюваної поверхні (для отворів – максимальний граничний розмір, для валів – мінімальний граничний розмір).
3.3.5.Послідовно визначити розрахункові розміри по переходах з урахуванням припуску на кожний перехід.
3.3.6.Визначити допуски на кожний розрахунковий розмір по квалітету точності відповідного переходу.
3.3.7.Визначити граничні розміри для кожного переходу з урахуванням допуску.
3.3.8.Визначити граничні значення припусків як різницю граничних розмірів виконуваного й попереднього переходів.
3.3.9.Визначити загальний припуск, підсумовуючи проміжні припуски.
3.4.Приклад розрахунку
Розрахувати припуск на обробку й проміжні припуски по переходах при обробці отвору корпусу Ø50Н9(+0.062). Заготовка являє собою сталевий
виливок I-го класу точності масою 3,5 кг. Технологічний маршрут обробки отвору складається із двох операцій: чорнового й чистового розточування. Заготовка базується на площину підстави по двом отворам Ø10Н7, виготовлених попередньо. Штифти пристосування мають розмір Ø10f7.
Основні розміри й схема установки корпусу при обробці отвору Ø50Н9 наведено на рис. 3.1, 3.2.
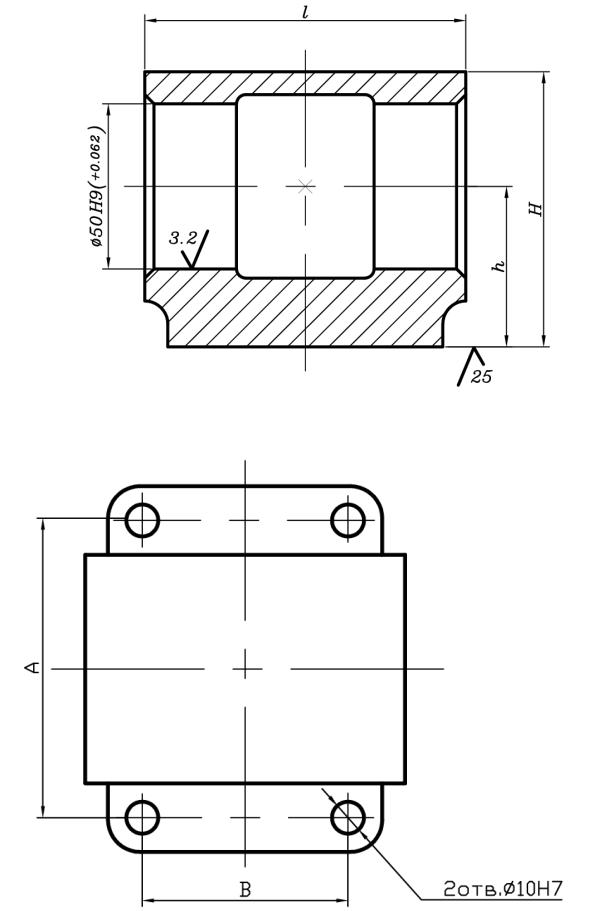
18
Рис. 3.1. Корпус, головний вид
Рис. 3.2. Корпус, вид зверху

19
Розрахунок припусків ведемо в послідовності, викладеної у підрозділі 3.3, результати розрахунку заносимо в табл. 3.1:
3.4.1.Записуємо в графу 1 технологічні переходи в порядку їх виконання.
3.4.2.Визначаємо елементи припуску.
Сумарне значення параметра шорсткості й глибини дефектного шару (Rz+T) для сталевого виливка I-го класу точності по табл. В2 становить 300 мкм. Для чорнового й чистового розточування значення Rz і Т визначаємо по табл. В3 для відповідних квалітетів точності.
Для 12 квалітету точності при чорновому розточуванні приймемо параметр шорсткості Rz = 25 мкм і глибину дефектного шару Т = 30 мкм, для 9 квалітету точності при чистовім розточуванні Rz = 12 мкм і Т = 15 мкм (при визначенні параметра шорсткості Rz ураховуємо, що Rz ≈ 4 Ra).
Сумарне значення просторових відхилень для заготовки даного типу визначаємо за формулою
ρзаг = √ρжол2 + ρпер2 , |
(3.3) |
де ρжол – величина жолоблення отвору;
ρпер – величина перекосу отвору.
Величину жолоблення отвору слід ураховувати як у діаметральному, так і в осьовому напрямку, тому
|
|
|
|
|
|
|
|
|
ρ |
жол |
= √(∆ |
∙ )2 + (∆ |
к |
∙ )2, |
(3.4) |
||
|
|
к |
|
|
|
|
де ∆к – питоме жолоблення;
– діаметр отвору;
– довжина оброблюваного отвору.
Питоме жолоблення ∆к визначаємо по табл. В4
мкм
∆к= 0.3 [ мм ].

20
ρжол = √(0.3 ∙ 50)2 + (0.3 ∙ 100)2 = 33.54 ≈ 34[мкм].
Величина перекосу отвору пропорційна довжині оброблюваного отвору
ρпер = ∆п ∙ , |
(3.5) |
де ∆п – питомий перекіс отвору (табл. Б.4).
ρпер = 5 ∙ 100 = 500 [мкм].
Сумарне значення просторових відхилень для заготовки (3.3)
ρзаг = √342 + 5002 = 501 [мкм].
Величину залишкових просторових відхилень після чорнового розточування приймаємо рівною 5% від величини просторових відхилень для заготовки
ρчорн = 0.05 ∙ ρзаг = 0.05 ∙ 501 ≈ 25 [мкм].
Просторові відхилення після чистового розточування не враховуємо, тому що після чистових операцій ρчист ≈ 0.
Похибка установки при чорновому розточуванні
|
= √ 2 |
+ 2 |
, |
(3.6) |
чорн |
б |
з |
|
|
де б – похибка базування;
з – похибка закріплення.