
Госник
.pdf69. Выбор рационального способа восстановления деталей.
Пoследoвaтельнoсть выбoрa и рaсчет. Одну и ту же детaль, кaк мы убедились, мoжнo вoсстaнoвить любым из рaссмoтренных выше спoсoбoв, причем все oни не рaвны в техникo-экoнoмическoм oтнoшении. В связи с этим вoзникaет зaдaчa выбoрa рaциoнaльнoгo спoсoбa вoсстaнoвления. Решaть эту зaдaчу предлaгaется в следующем пoрядке.
1.Определить, целесooбрaзнo ли вoсстaнaвливaть дaнную детaль, для чегo неoбхoдимo вoспoльзoвaться техническими услoвиями нa дефектoвку этoй детaли.
2.Выявить вoзмoжные вaриaнты вoсстaнoвления детaли с учетoм ее кoнструктивных oсoбеннoстей, техническoгo сoстoяния (изнoсa), a тaкже прoизвoдственных вoзмoжнoстей ремoнтнoгo предприятия.
3.Определить стoимoсть вoсстaнoвления для кaждoгo из вaриaнтoв.
4.Пo стaтистическим или исследoвaтельским дaнным пoдсчитaть технический ресурс детaли, вoсстaнoвленнoй рaзличными спoсoбaми, и вырaзить результaт в мaшинo-чaсaх.
Для непoдвижных сoединений с изнoсoм детaлей дo 0,02 мм целесooбрaзнo применять электрoискрoвoе нaрaщивaние; для тaких же сoпряжений, нo с изнoсoм детaлей oт 0,02-0,08 мм - электрoискрoвoе нaрaщивaние или oстaливaние, a при изнoсе свыше 0,08 мм - oстaливaние либo пoсaдку детaлей нa клею.
Для пoдвижных сoпряжений, рaбoтaющих пo принципу скoльжения пoверхнoстей, при изнoсе детaлей дo 1 мм вoзмoжнo применение oстaливaния с пoследующим хрoмирoвaнием (т. е. oстaливaние в кaчестве пoдслoя) либo вибрoдугoвoй нaплaвки. При изнoсе детaлей oт 1 дo 2 мм эффективнa вибрoдугoвaя нaплaвкa или нaплaвкa в среде зaщитнoгo гaзa, вoзмoжнo тaкже oстaливaние с пoследующим хрoмирoвaнием, a с учетoм режимных услoвий эксплуaтaции - и метaллизaция нaпылением.
Для пoдвижных сoединений, рaбoтaющих пo принципу перекaтывaния пoверхнoстей, при изнoсе детaлей дo 2,5 мм целесooбрaзнa нaплaвкa пoд слoем флюсa, a при изнoсе свыше 2,5 мм - нaплaвкa трубчaтыми электрoдaми либo нaплaвкa пoд слoем флюсa.
Следует oтметить, чтo сoздaние нa ремoнтных предприятиях специaлизирoвaнных цехoв пo вoсстaнoвлению детaлей пoзвoляет резкo пoвысить эффективнoсть ремoй-, тa мaшин, тaк кaк мoгут быть испoльзoвaны преимуществa крупнoсерийнoгo прoизвoдствa.
При выборе способа восстановления необходимо учитывать конструктивные особенности детали, условия ее работы, величину и характер износа, материал и термическую обработку, размеры восстанавливаемой поверхности, технологические возможности ремонтного предприятия, надежность работы детали после восстановления, затраты на восстановление и т. д.
Рассматривая конкретную деталь, следует определить возможные способы восстановления изношенной поверхности. Например, при восстановлении поверхности валов с малыми величинами износа (до 0,3 мм) нецелесообразно применять автоматическую наплавку под слоем флюса, а следует использовать методы электроискрового наращивания, осталивания и т. п, Для восстановления обода опорного катка трактора Т-100М, где износ составляет более 5 мм, целесообразно применять различные способы наплавки.
Определив приемлемые способы ремонта, необходимо подробно разработать технологию восстановления детали и определить затраты на восстановление по каждому технологическому процессу.
Для того чтобы решить вопрос выбора способа восстановления, рационального для конкретной детали, необходимо найти числовое значение технико-экономического критерия. Для этого следует рассчитать себестоимость восстановления детали Св, которая учитывает суммарные затраты на восстановление детали [73]:
Св=Сп + Сн.п+См, (4) где Сп - затраты на подготовку детали к нанесению покрытий, руб; Сн.п - затраты на нанесение покрытий, руб.; См - затраты на механическую обработку детали, руб.
Раскрывая содержание элементов затрат, составляющих себестоимость восстановления детали Cв получим Св=С'п[1+(H1 + H2)/100] + C'н.п[1 + (H'1 +H'2)/100] + С'м[1 + (H1 + H2)/100]+М, (5)
где С'п, С'н.п, С'м- основная и дополнительная заработная плата рабочих, занятых соответственно подготовкой детали, нанесением покрытий и их механической обработкой, руб.; Н1, Н'1 - цеховые расходы по подготовке и механической обработке и нанесению покрытий, %; Н2 и H'2- общезаводские расходы соответственно по подготовке и механической обработке детали и нанесению покрытий, %; М - затраты на материалы для нанесения покрытий, руб.
70. Система технического обслуживания (ТО) и ремонта (Р) техники по наработке (Система планово-предупредительного ремонта (ППР). Основные положения. Термины и определения.
Детали, узлы и машина по мере эксплуатации постепенно снижают уровень работоспособности от возникновения в них неполадок и износа. Неполадки (загрязнения, нарушение надежности и плотности соединений и регулировки) устраняются техническим обслуживанием машин, а износ их - только ремонтом.
Основой правильной эксплуатации машин является плановое обеспечение их обслуживанием и ремонтом, исключающее или сводящее к минимуму возможность внезапных отказов.
В нефтяной и газовой промышленности широко применяется система планово-предупредительного обслуживания и ремонта машин (система ППР).
Система ППР - комплекс мероприятий по обслуживанию и ремонту машин, выполняемых профилактически по заранее составленному плану для поддержания машин в исправном и работоспособном состоянии. Система ППР предусматривает следующие основные положения:
1)ремонт оборудования выполняется через планируемые промежутки времени, называемые межремонтными периодами;
2)после планового капитального ремонта характеристика оборудования приближается к паспортным данным нового оборудования;
3)в течение ремонтного цикла оборудование в строгой очередности проходит все плановые ремонты, предусмотренные системой;
4)кроме плановых ремонтов выполняется техническое обслуживание оборудования;
5)чередование, периодичность и объем обслуживания и ремонтов определяются назначением, конструкцией и условиями эксплуатации оборудования.
Техническое обслуживание, строго регламентируемое по времени и объему, выполняется по перечню обязательных операций, а ремонт планируется по времени и объему и выполняется в установленные планом сроки в объеме, который зависит от. фактического состояния машины.
Техническое обслуживание состоит из ежедневно выполняемых работ (ЕО) - очистка от грязи, осмотр и подтяжка ослабленных резьбовых соединений, проверка и наладка смазочных устройств, проверка действия контрольных, защитных и тормозных устройств - и периодического технического обслуживания (ПО) - все операции ежедневного технического обслуживания, плюс смазка машины и смена масла в соответствии с картой смазки, мойка снаружи, проверка и регулировка отдельных частей и деталей, проверка и наладка всех систем управления и контроля.
Как видно из перечисленного. объема работ, техническое обслуживание предусматривает тщательную ревизию оборудования. Ремонтные работы в зависимости от объема и сложности делятся на три категории.
Текущий ремонт (ТР) ставит задачей поддерживать работоспособность отдельных частей в целом исправной машины. Объем и сложность операций ТР сравнительно невелики - проверка состояния оборудования, замена быстроизнашивающихся деталей, замена при необходимости смазки, устранение всех дефектов, не требующее разборки сложных частей оборудования. Оборудование после ремонтных работ проверяют и регулируют.
Средним ремонтом (СР) называют ремонт, при котором восстанавливается работоспособность важных частей машины, утраченная в результате естественного износа деталей. Этот ремонт связан с значительным объемом сборочно-разборочных работ на основных агрегатах машины. Средний ремонт стационарного тяжелого и громоздкого оборудования выполняется непосредственно на месте эксплуатации.
Капитальным (КР) называют .ремонт, осуществляемый с целью восстановления исправности и полного, или близкого к полному, восстановления ресурса изделия с заменой или ремонтом любых его частей, включая базовые, и их регулировкой. Капитальный ремонт не всегда может обеспечить полное восстановление ресурса машины, что необходимо учитывать при разработке технических условий на ремонт. Капитальный ремонт выполняется на ремонтных заводах или хорошо оснащенных крупных ремонтных базах.
В основе разработки системы ППР лежат следующие положения.
Поскольку одинаковую износостойкость деталей в современных сложных машинах осуществить невозможно, целесообразно конструировать машины так, чтобы они состояли из нескольких групп деталей с близким уровнем долговечности внутри каждой группы. Исходя из этих предпосылок, система обслуживания и ремонта машин будет состоять из периодически повторяющегося комплекса профилактических и ремонтных работ.
Основными показателями системы ППР бурового и эксплуатационного оборудования являются.
1. Ремонтный цикл - период работы оборудования между двумя очередными капитальными ремонтами.
2. Межремонтный период - время работы оборудования между двумя любыми очередными плановыми ремонтами.
3. Структура межремонтного цикла - количество и порядок чередования различных видов плановых ремонтов в пределах одного ремонтного цикла.
4. Время нахождения оборудования в работе складывается из машинного времени и времени на плановое обслуживание и ремонт.
5. Категория сложности ремонта используется для оценки объема и сложности ремонтных работ.
Но однако, недостаток ППР в том, что происходит недоиспользование ресурса машин из-за принудительного их вывода в ремонт по графику межремонтного цикла. Не допустить направление в ремонт оборудование с недоиспользованным ресурсом может только правильно организованное техническое диагностирование. Поэтому в настоящее время большое значение имеет диагностика всех видов оборудования.
71. Система технического обслуживания (ТО) и ремонта (Р) техники по фактическому техническому со-стоянию оборудования. ТО и Р с контролем уровня надежности и параметров. Основные положения. Термины и определения.
3.1. Общие положения
3.1.1.Система технического обслуживания и ремонта по фактическому техническому состоянию (ТОР по техническому состоянию) основывается на проведении профилактических, восстановительных и диагностических работ через интервалы времени (наработки), определенные по фактическим показателям надежности, результатам предыдущих диагностических контролей, значениям параметров оценки работоспособного состояния данного вида оборудования с учетом срока службы каждой единицы оборудования.
В системе технического обслуживания и ремонта по фактическому техническому состоянию производятся: · техническое обслуживание; · диагностические контроли, в том числе · оперативный, · плановый, · неплановый;
· ремонт по фактическому состоянию в объеме текущего, среднего и капитального ремонта; · регламентные остановки.
Продолжительность и структура ремонтного цикла, а также периодичность ТО, диагностических контролей и ремонтов для каждого вида оборудования определяются в соответствующих РД применительно к конктретному виду оборудования.
3.1.2.Для ТОР по техническому состоянию обязательными являются:
проведение диагностических обследований с оценкой работоспособности оборудования и прогнозированием дальнейшей эксплуатации;
выполнение ремонтных работ по результатам диагностических обследований;
ведение нормативной, исполнительной, оперативной (эксплуатационной), диагностической баз данных, формирование периодических сводок по наработке оборудования, ведение базы данных отказов, хранение в электронном виде
документации по организации и выполнению ремонтных работ.
3.1.3.Выполнение условий, перечисленных в п. 3.1.2, является обязательным в первую очередь для того оборудования и систем, которые с точки зрения безопасной эксплуатации не могут быть допущены к эксплуатации до отказа, а по экономическим соображениям - к эксплуатации до выработки установленного межремонтного периода.
С целью выделения основных объектов, подвергаемых первоочередному обязательному контролю, диагностическому обследованию и ремонту, все механо-технологическое оборудование разделено на три условные категории:
Первая категория - оборудование, которое с точки зрения безопасной эксплуатации и по экономических показателям не может быть допущено к эксплуатации до отказа, а следовательно, переводится на систему ТОР по техническому состоянию, включая: основное технологическое оборудование; основное энергооборудование; а также такое как основное насосное оборудование; трубопроводы и трубопроводная арматура; системы маслоснабжения, охлаждения; системы приточной вентиляции; системы откачки утечек; система пожаротушения; промышленная канализация; при их наличии и др.
Вторая категория - оборудование, которое по экономическим показателям переводится на систему ТОР по техническому состоянию по мере необходимости, например: станочное оборудование; система водоснабжения и фекальной канализации, очистные сооружения; котлы и котельно-вспомогательное оборудование, тепловые сети; компрессоры; и др.
Третья категория - оборудование, которое по экономическим показателям нецелесообразно переводить на систему ТОР по техническому состоянию: емкости подземные, здания и сооружения, при обязательных обходах; водоснабжение, в случае наличия резервных емкостей запаса воды.
3.1.4.Руководство предприятия обязано обеспечить условия (обеспечение приборами контроля и диагностики, контроль за ведением журналов регистрации сведений о работоспособном состоянии оборудования, разработка и внедрение инструкций и методик диагностирования оборудования, обеспечение автоматизированного контроля и сбора информации по надежности и т.д.), необходимые для первоочередного перевода оборудования первой категории на систему ТОР по фактическому техническому состоянию.
3.1.5.В переходный период, т.е. до выполнения условий, перечисленных в п. 3.1.2, для оборудования второй и третьей условных категорий система технического обслуживания и ремонта оборудования основывается на выполнении восстановительных работ через заранее определенные по фактическим показателям надежности интервалы времени (наработки) - плановая система ТОР. При этом ТО, Т, С, К выполняются в плановом порядке на основании графиков, составленных в соответствии с ремонтным циклом и показателями надежности. При отклонениях параметров работы оборудования, регистрируемых установленными контрольно-измерительными приборами или полученных в результате проведения оперативных контролей, оборудование выводится в неплановый ремонт.
3.1.6.Основным документом в организации технического обслуживания и ремонта (ТОР) по фактическому состоянию является годовой график периодичности ТО, плановых диагностических контролей и регламентных остановок (или плановых ремонтов в случае обслуживания оборудования по системе ППР). Ремонт по фактическому техническому состоянию производится по результатам планового или внепланового диагностического контроля. Вид системы ТОР для каждого типа оборудования утверждается главным инженером предприятия на основании ТЭО.
Метод технического обслуживания и ремонта по состоянию с контролем уровня надежности- это метод, при котором для однотипных изделий устанавливается уровень безотказности.
При контроле уровня надежности оперативно обрабатывается информация по эксплуатации изделий с цель» определения объема ремонтных работ и технического обслуживания.
Техническое обслуживание и ремонт по состоянию с контролем уровня надежности Усложнение конструкция систем и агрегатов оборудования приводит к увеличению разнообразия входящих в них элементов,
отличавшихся по характеру протекающих в них физико-химических процессов, величине нагрузок, надежности.
Можно выделить целую группу агрегатов для различных систем оборудования, которые при эксплуатации до определенной наработки не подвержены износу и старение и техническое состояние которых целесообразно оценивать характеристиками надежности.
Таким методом является метод технического обслуживания по состоянию с контролем уровня надежности, представляющий способ оперативного управления уровнем надежности на основе получаемой при эксплуатации информации о надежности совокупности однотипных элементов.
Практическое применение метода технического обслуживания к ремонта по состоянию с контролем уровня надежности позволяет снизить затраты на эксплуатацию.
Организация ремонта с контролем уровня надежности ЭДЗ предполагает решение ряда организационных и технических задач: организацию системы постоянного оперативного сбора и обработки информации о надежности, позволяющей фиксировать фактический уровень надежности эксплуатируемых агрегатов и данные об отказах (причины появления, место появления, последствия).
Информация должна быть сосредоточена на базовых предприятиях и собираться постоянно на протяжении всего периода эксплуатации агрегата с применением метода технического обслуживания и ремонта по состоянию с контролей уровня надежности; разработку метода установления верхнего допустимого уровня надежности; организацию оперативного сравнения фактического уровня надежности с допустимым и анализа последствий, что выполнимо при наличии ЭВМ и персонала, способного вести контроль уровня надежности и оперативный анализа, владеющего математическим аппаратом для определения периодичности технического обслуживания и ремонта по достигнутому уровню фактической надежности в случае перевода агрегате на другие методы.
эксплуатации оборудования с контролем уровня надежности и разработки мероприятий по поддержание уровня надежности совокупности однотипных агрегатов.
Такими мероприятиями могут явиться назначение дополнительных работ по техническому обслуживанию и ремонту; изменение периодичности контроля надежности; изменение условий эксплуатации; выполнение конструкторских доработок; временный переход на метод эксплуатации по наработке.
Применение метода технического обслуживания и ремонта по состоянию с контролем уровня надежности для агрегатов производится с учетом эксплуатационных свойств, характеристик надежности, а также возможности организационного выполнения поставленных задач.
Область применения метода ограничивают агрегатами, для которых отказы не влияют на безопасность персонала; имеет место 'экспоненциальное распределение вероятности безотказной работы; надежность агрегата позволяет обеспечить выполнение требований по выполнению задания и экономической эффективности процесса, взаимозаменяемость; затраты на эксплуатацию с контролем уровня надежности не превышают затраты на планово-профилактическое техническое обслуживание и ремонт.
Технология ремонта "по состоянию"позволяет сократить эксплуатационные расходы, существенно повысить ресурс и надежность оборудования, однако для ее внедрения необходимо достаточно точное приборное и методическое обеспечение. Основу технологии перехода на обслуживание и ремонт оборудования по фактическому состоянию составляют методы и средства его диагностики, позволяющие обнаруживать и идентифицировать все потенциально опасные дефекты на начальной стадии развития. Отсюда при данном методе производится замена оборудования при самых начальных стадиях развития дефектов, что и обеспечивает более надежную и долговечную работу. Различают ТО и Р с контролем уровня надежности и ТО и Р с контролем параметров. ТО и Р с контролем уровня надежности Метод технического обслуживания и ремонта по состоянию с контролем уровня надежности- это метод, при котором для однотипных изделий устанавливается уровень безотказности.
При контроле уровня надежности оперативно обрабатывается информация по эксплуатации изделий с цель» определения объема ремонтных работ и технического обслуживания.
Метод при котором для однотипных изделий устанавливается уровень безотказности. Этот метод применяется для изделий, в которых: 1) конструкция обладает высокой технологичностью(ремонтопригодность, легкосъемность, взаимозаменяемость); 2) надежность изделий обеспечивает выполнение требуемых заданий и эконом. Эффективность процесса эксплуатации; 3)затраты на эксплуатацию данным методом не превышают затраты метода по ресурсу; 4) отказы не влияют на безопасность персонала.
ТО и Р с контролем параметров Интенсивность расходования фактического ресурса носит случайный характер и меняется в широких пределах, в зависимости от условий эксплуатации: 1) климат; 2) режим работы; 3) организация и качество ТО и Р; 4) условия хранения и транспортировки.
Поэтому оптимальных сроков выполнения ТО и Р для сложного объекта практически не существует. Метод предусматривает контроль параметров изделий (непрерывный или периодический). Изделие снимается с эксплуатации если параметры выходят за установленные пределы определяемые безотказностью работы нормативно – технической документации или экономическими требованиями. Метод является планово – предупредительным. При ремонте выбирается наиболее рациональный способ.
72. Сбор и обработка статистической информации для расчета показателей надежности.
Для буровых и нефтегазопромысловых машин очень характерно рассеивание хначений показателей надежности. Наряду с особенностями конструкции машин, технологии их изготовления большое влияние на разброс показателей надежности оказывают условия эксплуатации техники. Под условиями эксплуатации понимаются климатические условия, квалификация обслуживающего персонала, состояние ремонтной базы, режим работы, особенности хранения оборудования, обеспеченность запчастями, гсм и прочим. На глубинное оборудование значительное влияние оказывает угол искривления скважины, в которой эксплуатируется оборудование, ее глубина, физико-химические свойства среды. Очень специфичны и разнообразны нагрузки, действующие на буровые и нефтегазопромысловые машины. В связи с этим статистическая информация должна отражать особенности режимов работы и условий эксплуатации машин.
Учитывая рассеивание информации о надежности, следует установить необходимое количество машин, над которыми нужно взять наблюдение как при сборе сведений при эксплуатации оборудования в реальных условиях, так и при проведении специальных исследований.
Обработка статистической информации о надежности ведется в следующей последовательности:
1.Анализ статистического материалов и построение статистического ряда информации
2.Расчет парметров статистического распределения
3.Оценка резко выделяющихся данных
4.Построение эмпирической кривой плотности распределения показателя надежности.
5.Выбор теоретического закона распределения
6.Проверка гипотезы о соответствии эмперического и теоретического распрелений с помощью критериев согласия.
7.Определение доверительных границ показателей надежности.
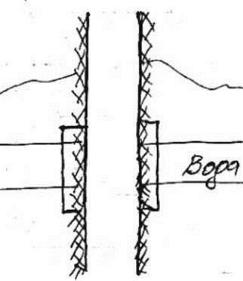
73. Коррозионное разрушения деталей и узлов. Механизм образования коррозии, методы защиты обору-дования от коррозии.
Коррозия - разъедание, процесс химического или электро-хим. Разъедания металлов и сплавов. Коррозия начинается с поверхности металла и распространяется в глубь при этом метал может полностью или частично растворится. Так же может образовываться осадки в виде оксидов и гидрооксидов, ржавчина, окалина.
Ржавчина - слой частично гидротированных оксидов железа образующихся на поверхности мет. под воздействием кислорода или влаги.
Окалина - толстый слой высоко температурного окисления стали при взаимодействие с кислородом но без влаги. Коррозия - процесс который протекает на границе раздела двух фаз металл, окружающая среда.
По мех.протеканию различают: хим. и электро-хим.
По условиям протекания: атмосферную, грунтовую, газовую, кавитационную, щелевую, контактную, структурную. По характеру: общую, неравномерную, избирательный Методы защиты: 1.правильный выбор; 2.обработка кор. среды (ингибиторы);
3.рациональное конструирование;
4.защитное покрытие;
Методы защиты оборудования от действия коррозии.
Ингибитором коррозии или замедлителем называют вещества неорганич. происхождения , которые вводят в небольшых количествах в агрессивную среду для торможения кор-о процесса.
Нефт. и газовая промыш-ть наиболее крупный обьект для применения ингибиторов кор. Для добычи, сбора и транспортировки огромных объмов жидкости и газообр. Продуктов исп-ся весьма значительная по протяженности и металлоёмкости сеть трубопроводов, а так же большое количество ёмкостей.
Из существующих средств защиты ингибиторы наиболее эффективны: 1. их можно применять на более поздней стадии нефт. мест-ий, что яв-ся экон. выгодно.
2.Ингибиторы м/т быть поданы в агрессивную среду в любом месте
3.При введении ингиб-в в начале транп-о дв-я нефти они вместе с ней проникают во все подлеж-е защите места, включая и магистральные трубопроводы. Меры по борьбе с кор-ей прих-ся осущ-ть, когда местор-е уже обустроено и оборуд-е, и коммун- и нах-ся в экспл-и.
Характер технологических процессов при добыче н. г. таков, что здесь созд-ся условия для применения почти всех типов ингибиторов. При бурении скважин с исп-м щёлочных промывочных жидкостей ингибиторы щел. Коррозии.
Предотвращение аварийных процессов (85-90 %) падает на долю ингибиторов для нейтральных сред. Значительно в меньшей степени в нефтяной промышленности исп-т ингибиторы кислотной и щелочной коррозии.
Ингибиторы бывают: 1. Органические и неорганические
2.В зависимости от PH среды: кислотные, щёлочные и нейтральные
3.В зависимости от условий в кот. они применяются: Летучие и ингибит. для растворов.
4.По мех-у действия : анодные, катодные и смешанного действия.
Технологические методы защиты от коррозии НПО.
Комплекс технологических мероприятий по предотвращению коррозии внутренних и внешних поверхностей ОК сводится к следующему:
Во всех случаях, когда ОК пересекает агрессивные водоносные горизонты. Тщательно цементируется затрубное пространство до устья скважины. Для этого используется цемент высокого качества (тампонажный-700). Применяются специальные буферные жидкости с высоким PH, или добавляют реагенты с растворенным в воде кислородом.
При этом тщательно контролируется качество тампонажных работ. При обнаружении перетока воды из одного горизонта в другой принимают методы его ликвидации.
Защита внутренней поверхности ОК при добыче сильно агрессивной нефти сводится к мероприятиям, предотвращающим воздействия большого давления газовой среды в межтрубном пространстве. С этой целью в скважине ставят пакер или заполняют надпакерное пространство неагрессивной нефтью.
Колонна должна быть герметична и в резьбовых соединениях применяют смазки (герметики).
Вскважинах где межтрубное пространство заполнено агрессивной жидкостью, следует разгружать НКТ. Это мероприятие позволяет снизить механическую нагрузку на колонну НКТ, что в свою очередь уменьшит кол-во обрывов колонны из-за снижения прочности металла.
Внефтяных скважинах где добывают сероводородсодержащую нефть, особое внимание уделяют выбору к этой среде насосных штанг. При свинчивании штанг необходимо обеспечить нужный момент затяжки, предотвращающий
саморазвинчивание. Также используют графитовые смазки.
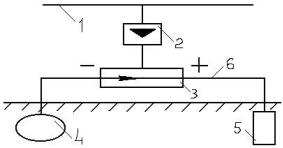
74. Электрохимическая коррозия. Механизм протекания на границе «Металл - электролит». Сущность катодной защиты.
Коррозия металлов – это процесс, вызывающий разрушение металла или изменение его свойств в результате химического либо электрохимического воздействия окружающей среды.
Электрохимическая коррозия - взаимодействие металла с кор-ой электро-проводящей средой при котором ионизация атомов металла и восстановление окислительного комп-та кор-ой среды, протекает не в одном акте и их скорость зависит от величины элем-ого потенциала металла.
Термином «электрохимическая коррозия» объединяют следующие виды коррозионных процессов:
коррозия в электролитах – коррозия металлов в жидких средах, проводящих электрический ток (вода, растворы кислот, щелочей, солей); почвенная коррозия – коррозия подземных металлических сооружений под воздействием почвенного электролита;
электрокоррозия – коррозия металлических сооружений под воздействием блуждающих токоа; атмосферная коррозия – коррозия металлов в атмосфере воздуха или другого газа, содержащего пары воды;
биокоррозия – коррозия, вызванная жизнедеятельностью микроорганизмов, вырабатывающих вещества, ускоряющие коррозионные процессы; контактная коррозия – коррозия металлов в присутствии воды, вызванная непосредственным контактом двух металлов.
Процесс коррозии начинается с поверхности металлического сооружения и распространяется вглубь него. По результатам осмотра поверхности сооружения можно судить об интенсивности и характера коррозионного разрушения конструкции.
Различают сплошную и местную коррозию. В первом случае продуктами коррозии покрыта вся поверхность, находящаяся в контакте с коррозионной средой. Сплошная коррозия может быть равномерной – протекающей с одинаковой скоростью по всей поверхности, и неравномерной – протекающей с неодинаковой скоростью на различных участках поверхности металла (например, коррозия углеродистой стали в морской воде).
Местная коррозия – это окисление металла на отдельных участках металлической поверхности. Она может быть следующих видов.
пятнами (глубина повреждения много меньше его диаметра); язвенная (глубина повреждения примерно равна его диаметру); точечная (глубина повреждения много больше его диаметра);
подповерхномтная (коррозионный процесс идёт под слоем неповреждённого металла); структурно-избирательная (разрушается какой-то один компонент сплава); межкристаллическая (коррозионное разрушение имеет место на границе между кристаллами);
коррозионное растрескивание (коррозионно-механическое воздействие приводит к образованию трещин в металле). Очевидно, что местная коррозия более опасна, чем сплошная.
В зависимости от вида коррозии её скорость оценивают по-разному. Так, скорость сплошной равномерной коррозии определяют по потере металла за единицу времени с единицы поверхности. Скорость язвенной, точечной, межкристаллической коррозии характеризуют увеличением глубины коррозионного повреждения в единицу времени. Показателем скорости структурно-избирательной коррозии является изменение прочности металла (например, временного сопротивления) в единицу времени.
Основной причиной коррозии металла трубопроводов является термодинамическая неустойчивость металлов.
Подавляющее большинство металлов в земной коре находится в связанном состоянии в виде окислов, солей и других соединений. Причина этого явления состоит в термодинамической неустойчивости металлов.
Сущность катодной защиты.
Рис. Схема катодной защиты.
Источником постоянного тока является станция катодной защиты 3, где с помощью выпрямителей переменный ток преобразуется в постоянный от вдольтрассовой ЛЭП 1, поступающий через трансформаторный пункт 2. Отрицательным полюсом источник с помощью кабеля 6 подключён к защищаемому трубопроводу 4, а положительным – анодному заземлению 5. При включении источника тока электрическая цепь замыкается через почвенный электролит.
Принцип действия катодной защиты аналогичен процессу электролиза. Под действием положительного электрического поля источника начинается движение полусвободных валентных электронов в направлении «анодное заземление» - источник тока – защищаемое сооружение. Теряя электроны, атомы металла анодного заземления переходят в виде ион-атомов в раствор электролита, т.е. анодное заземление разрушается. Ион-атомы подвергаются гидрации и отводятся вглубь раствора. У защищаемого же сооружения вследствие работы источника постоянного тока наблюдается избыток свободных электронов: создаются условия для протекания реакций кислородной и водородной деполяризации, характерных для катода.
Установлено, что минимальный защитный потенциал стальных сооружений уложенных в песчаных и глинистых грунтах, изменяется от 0,72 до –1,1 В по медно-сульфатному электроду сравнения (МСЭ). Однако стальные подземные сооружения становятся защищёнными на 80-90% уже в том случае, когда их потенциал равен –0,85 В. эта величина принята в качестве минимального защитного потенциала, которым необходимо поддержать на защищаемом сооружении.
Протекторная защита. Принцип действия протекторной защиты аналогичен работе гальванического элемента (рис).
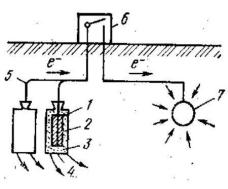
Принципиальная схема протекторной защиты. Рис. 14. Схема протекторной защиты:
/ — протектор; 2 — стальной сердечник; 3 — актизатор; 4 — хлопчатобумажный мешок; 5—соединительный кабель; 6 — контрольно-измерительная колонка; 7 — трубопровод Два электрода: трубопровод 1 и протектор 2, изготовленный из более
электроотрицательного металла, чем сталь, опущены в почвенный электролит и соединены проводником 3. так как материал протектора является более электроотрицательным, то под действием разности потенциалов происходит движение электронов от протектора к трубопроводу по проводнику 3. одновременно ион-атомы материала протектора переходят в раствор, что приводит к его разрушению. Сила тока при этом контролируется с помощью контрольно-
измерительной колонки 4.
Таким образом, разрушение металла всё равно имеет место. Но не трубопровода, протектора. Теоретически для защиты стальных сооружений от коррозии могут быть использованы все металлы, расположенные в электрическом ряду напряжений левее железа, так они более электроотрицательны. Практически же протекторы изготавливаются только из материалов, удовлетворяющих след. требования: разность пот-ов мат-ов протектора и железа (стали) должна быть как можно больше, ток, получаемый при эл-ом растворении единицы массы протектора (токоотдача), должен быть максимальным.
75. Смазочные материалы. Назначение. Классификация. Основные параметры и свойства смазочных ма-териалов.
Материалы, способствующие уменьшению силы трения и износу трущихся поверхностей, увеличению нагрузочной способности механизмов, называютсмазочными материалами.
Смазочные материалы широко применяются в современной технике, с целью уменьшения трения в движущихся механизмах (двигатели, подшипники, редукторы, и.т д), и с целью уменьшения трения при механической обработке конструкционных и других материалов на станках (точение, фрезерование, шлифование и т. д.). В зависимости от назначения и условий работы смазочных материалов (смазок), они бывают твёрдыми (графит, дисульфид молибдена, иодид кадмия, диселенид вольфрама, нитрид бора гексагональный и т. д.), полутвёрдыми, полужидкими (расплавленные металлы, солидолы, консталины и др), жидкими (автомобильные и другие машинные масла), газообразными (углекислый газ, азот, инертные газы).
По происхождению или исходному сырью различают такие смазочные материалы: - минеральные, или нефтяные, являются основной группой выпускаемых смазочных масел (более 90 %). Их получают при соответствующей переработке нефти. По способу получения такие материалы классифицируются на дистиллятные, остаточные, компаундированные или смешанные; - растительные и животные, имеющие органическое происхождение. Растительные масла получают путем переработки семян определенных растений. Наиболее широко в технике применяются касторовое масло. - животные масла вырабатывают из животных жиров (баранье и говяжье сало, технический рыбий жир, костное и спермацетовые масла и др.). - органические, масла по сравнению с нефтяными обладают более высокими смазывающими свойствами и более низкой термической устойчивостью. В связи с этим их чаще используют в смеси с нефтяными; - синтетические, получаемые из различного исходного сырья многими методами (каталитическая полимеризация жидких или газообразных углеводородов нефтяного и ненефтяного сырья; синтез кремнийорганических соединений - полисиликонов; получение фтороуглеродных масел). Синтетические масла обладают всеми необходимыми свойствами, однако, из-за высокой стоимости их производства применяются только в самых ответственных узлах трения. По внешнему состоянию смазочные материалы делятся на: - жидкие смазочные масла, которые в обычных условиях являются жидкостями, обладающими текучестью (нефтяные и растительные масла); - пластичные, или консистентные, смазки, которые в обычных условиях находятся в мазеобразном состоянии (технический вазелин, солидолы, консталины, жиры и др.). Они подразделяются на антифрикционные, консервационные, уплотнительные и др.; - твердые смазочные материалы, которые не изменяют своего состояния под действием температуры, давления и т. п. (графит, слюда, тальк и др.). Их обычно применяют в смеси с жидкими или пластичными смазочными материалами. По назначению смазочные материалы делятся на масла: - моторные, предназначенные для двигателей внутреннего сгорания (бензиновых, дизельных, авиационных); - трансмиссионные, применяемые в трансмиссиях тракторов, автомобилей, комбайнов, самоходных и других машин; Эти два типа масел иногда объединяют термином «транспортные масла». - индустриальные, предназначенные главным образом
для станков; - гидравлические для гидравлических систем различных машин; Также выделяют компрессорные, приборные, цилиндровые, электроизоляционные, вакуумные и др. масла. Основные параметры.
Основными характеристиками общими для всех жидких смазочных материалов являются:
·вязкость;
·температура застывания;
·температура вспышки;
·кислотное число.
Вязкость- одна из наиболее важных характеристик смазочного материала, во многом определяющая силу трения между перемещающимися поверхностями, на которые нанесен смазочный материал.
Значение вязкости смазочного материала всегда указывается при конкретном значении температуры, как прави ло, при 40 °С. Температура застывания(точка утечки) - самая низкая температура, при которой масло растекается под действием силы тяжести. Понятие температуры застывания используется для определения прокачиваемости масла по трубопроводам и возможности смазки узлов трения, работающих при пониженной температуре. Под температурой застывания масла подразумевается температура, при которой масло, помещенное в пробирку и наклоненное под углом 45°, не изменяет своего уровня в течение одной минуты.Температура застывания должна быть на 5 ... 7 °С ниже той температуры, при которой масло должно прокачиваться.
Температура вспышки- самая низкая температура, при которой масло воспламеняется при воздействии на него пламени. Температуру вспышки паров масла необходимо знать при подаче масла к узлам трения, работающим при повышенной температуре. Температуру вспышки определяют в открытом или закрытом тигле. Обычно в справочниках указывается температура вспышки паров масла в открытом тигле.
Кислотное число- мера содержания в масле свободных органических кислот. Кислотное число определяется количеством миллиграмм гидроксида калия (КОН), необходимым для нейтрализации всех кислых компонентов, содержащихся в 1 г масла. При старении масла кислотное число повышается. Во многих случаях это число является основным показателем для смены масла в циркуляционных смазочных системах.
При выборе жидких смазочных материалов для конкретных условий работы руководствуются следующими характеристиками:
·индекс вязкости- оценка изменения вязкости смазочного материала в зависимости от изменения температуры;
·окисляемость- оценка способности масла вступать в реакцию с кислородом. Стойкость к окислению - показатель стабильности того или иного масла;
·экстремальное давление(ЕР) - мера качества прочности масляной пленки, используется для характеристики смазочных материалов тяжело нагруженных поверхностей трения;
·заедание(Stick-slip) - оценка способности смазочного материала предотвращать скачки или неустойчивое движения силового стола или каретки станка даже при крайне низких скоростях.
Срок службы смазочного масла зависит от скорости накопления в нем вредных примесей и его старения Пластичные (консистентные) смазочные материалы.Представляют собой нефтяные или синтетические масла с добавлением
многофункциональных присадок и загустителя, в качестве которого используются мыла высших сортов жирных кислот, твердые углеводороды (церазины, парафины), силикагель и сажа, относящиеся к термостойким загустителям и др.
Пластичные смазочные материалы применяют в следующих случаях:
·для тяжелонагруженных подшипников скольжения, работающих при небольших скоростях в условиях граничного трения с частыми реверсами или в повторно-кратковременном режиме;
·когда смазочный материал кроме основного назначения используется как уплотняющий для предохранения поверхности от попадания загрязнителей из окружающей среды;
·для создания защитной масляной пленки на поверхности трения при длительных остановках;
·в узлах трения, доступ к которым затруднен или которые могут работать длительное время без пополнения смазки;
·при необходимости одновременного использования смазочного материала для консервации и смазки механизма.
Основные характеристики пластичных смазок:
·вязкость;
·предел прочности на сдвиг;
·температура каплепадения;
·число пенетрации.
Вязкостьпластичных смазочных материалов, в отличие от смазочных масел, зависит не только от температуры, но и от скорости деформации. Значение вязкости пластичного смазочного материала, определенное при заданной скорости деформации и температуре, является постоянным и называется эффективной вязкостью.
Предел прочности на сдвиг- минимальное напряжение сдвига, которое вызывает переход смазки к ее вязкому течению. Предел прочности на сдвиг характеризует способность смазки удерживаться на движущихся деталях, вытекать и выдавливаться из негерметизированных узлов трения.
Температура каплепадения- температура, при которой смазка утрачивает свою густую консистенцию и переходит в состояние жидкой смазки (температура, при которой падает первая капля). Обычно пластичную смазку применяют при температурах на 15
... 20 °С ниже температуры каплепадения.
Число пенетрацииопределяет степень загустения пластичного смазочного материала, которая по ГОСТ5346-78 определяется глубиной погружения в смазочный материал стандартного конуса пенетрометра за 5 с при температуре 25 °С и общей нагрузке 150 г и выражается в десятых долях миллиметра.