
книги2 / geokniga-ekologo-ekonomicheskaya-i-socialnaya-effektivnost-geotehnologicheskih-metodov
.pdfсодержит конденсируемых продуктов пиролиза угля, потому что они сгорают в потоке воздуха сразу же после выхода из угля, а продукты сгорания вступают в реагирование с раскаленным коксом и превращаются в газ, который (кроме азота, поступающего с воздухом) состоит в основном из водорода и оксида углерода (Н2 + СО). Отмывка газа от смол в классической технологии и последующая их утилизация — одна из главнейших проблем слоевой газификации. В том числе она связана с громоздкими сооружениями для переработки больших объемов воды, загрязненной фенолами и канцерогенными органическими соединениями. Характерным признаком такой технологии является специфический запах летучих веществ, которые пронизывают весь завод. Они депрессивно воздействуют на окружающую экосистему (вода, воздух, растительность) и, конечно, в первую очередь, на здоровье персонала. В новой технологии эта проблема полностью устранена - в производимом газе нет даже следов угольных смол. И это радикально удешевляет промышленное производство.
После прохождения через слой угля фронта термических превращений (термической волны) в газификаторе остается высокопористый твердый продукт. В зависимости от сорта исходного угля и выбранных технологических параметров процесса он может представлять собой активированный углерод или среднетемпературный кокс металлургического назначения. Как известно, активированный углерод является незаменимым веществом для адсорбции очень широкого спектра загрязняющих веществ. Его применяют для очистки самых разнообразных газовых выбросов. А кокс является универсальным технологическим топливом для многочисленных металлургических технологий и эффективным углеродным восстановителем для электротермических производств (например, получение ферросплавов, кремния, фосфора), где требуется высокая реакционная способность и большое электрическое сопротивление.
Новый процесс газификации (процесс «Термококс») использует только два исходных компонента — уголь и воздух и имеет только два конечных продукта — газ и активированный кокс. И ни одного побочного продукта. Энергия исходного угля распределяется между продуктами примерно поровну, а потери тепла в окружающую среду не превышают 4-5%. Это означает, что термический КПД процесса около 95% [151, С.70].
На основе детального изучения экспериментальных результатов в 1994 г. было принято решение о строительстве в г. Красноярске опытнопромышленного завода для переработки до 40 тыс. т бурого угля в год. В настоящее время он принадлежит компании «Карбоника-Ф». За время эксплуатации завода были отработаны технологические режимы переработки широкого спектра бурых и неспекающихся каменных углей. Производимый кокс из канско-ачинских углей аттестован как активированный уголь марки АБГ, в том числе для очистки питьевой воды. Он поставляется ряду предприятий России и на экспорт.
А исследователи продолжают открывать все новые особенности этой уникальной технологии. Так, выяснилось, что с помощью нестационарных
231
воздействий на управляющие параметры скорость процесса можно увеличить в несколько раз. Почти такого же результата можно добиться, изменяя традиционное для слоевой газификации аппаратурное оформление процесса. Эти усовершенствования существенно снизят капитальные затраты при строительстве новых заводов.
В настоящее время технология «Термококс» готова для крупномасштабного внедрения и тиражирования. В этой связи необходимо остановиться на перспективах использования получаемого газа.
Известно, что условно можно выделить два направления потенциального применения газа — энергетическое и химическое. Для первого наиболее эффективным является производство электроэнергии и тепла по парогазовому циклу. В этом случае газ сжигается в газовой турбине, а тепло продуктов сгорания используется для получения пара, который вращает паровую турбину.
Укрупненно можно выделить три потенциальные сферы использования газа как технологического сырья:
1.Использование основных компонентов (СО+Н2) как сырья для широкого спектра процессов химического синтеза, которые уже освоены промышленностью. Здесь, прежде всего, следует выделить производство метанола и особенно диметилового эфира как перспективной альтернативы нефтяному дизельному топливу.
2.Второе направление связано с выделением водорода (его содержание в продуктовом газе составляет 20-25 %). Это — универсальный продукт, потребление которого радикально возрастет уже в ближайшем будущем. Сфера его применения чрезвычайно обширна: от топлива для водородной энергетики до питательного субстрата для бактерий при производстве синтетических кормов для животноводства и биоразрушаемых полимеров, которые должны прийти на смену традиционному полиэтилену и полипропилену. Очень важно отметить, что в настоящее время промышленное внедрение всех перечисленных технологий сдерживается только высокой ценой водорода.
3.Использование газа как восстановителя в металлургических процессах прямого восстановления железа и других металлов.
Необходимо заметить, что ориентация на производство газа химического назначения требует изменения параметров процесса по сравнению с вариантом производства энергетического газа. И это допускает новая технология. Действующий в Красноярске завод управляется автоматизированной системой. Очень важно, что технология имеет очень простое и надежное аппаратурное оформление. Модульная схема позволяет оперативно изменять мощность в очень широком интервале значений.
Перечисленные выше сферы приложения угольного газа известны достаточно давно. Однако до настоящего времени их масштабное внедрение сдерживается экономическими показателями, так как во многих случаях угольный газ не выдерживает конкуренции с природным газом и нефтью. Здесь технология «Термококс» совершает своеобразный экономический прорыв. Схема когенерации с производством сравнительно дорогого кокса позволяет
232
предельно снизить (если необходимо, даже до нуля) издержки, относимые на производство газа. При таком ценообразовании угольный газ оказывается просто вне конкуренции [151, С.71].
Таким образом, на примере только одной из многих новых разработок по газификации угля мы смогли убедиться в том, что в этой области произошел качественный рывок. Процессы газификации угля с радикально улучшенными характеристиками, среди которых не последнюю роль играет высокий уровень экологической безопасности, остро необходимы именно в сегодняшних условиях нестабильности мирового энергетического рынка и повышенной техногенной нагрузки на окружающую среду.
Создание эффективных угольных технологий с пониженной эмиссией вредных веществ в пределах технологического цикла, позволяющих получать конкурентоспособные продукты и генерировать электрическую и тепловую энергию, является приоритетной задачей мировой энергетической стратегии.
Обобщая все вышесказанное хотелось бы особо отметить следующее. Сегодня вопрос, который задают скептически: «Газификация угля – это возврат в прошлое или шаг в будущее?», можно уверенно ответить: технологии газификации угля нового поколения являются шагом в самое ближайшее будущее.
233
Глава 10. ТЕОРЕТИЧЕСКИЕ И ПРАКТИЧЕСКИЕ РЕЗУЛЬТАТЫ СОЗДАНИЯ И ВНЕДРЕНИЯ НОВОЙ ТЕХНОЛОГИИ ПОЛУЧЕНИЯ ТЕПЛОВОЙ ЭНЕРГИИ ПРИ ПОДЗЕМНОМ СЖИГАНИИ УГЛЯ
10.1Теоретические основы технологии подземного сжигания угольных пластов
На сегодняшний день из направлений совершенствования традиционной технологии подземной добычи угля, приносящих ощутимый эффект, следует отметить переход на вскрытие шахтных полей блоками, погоризонтную подготовку пластов, агрегатную и бесцеликовую выемку. Расширение области применения гидравлической выемки угля, короткозабойных систем разработки, схем отработки пластов без постоянного присутствия людей в забоях сдерживается отсутствием надежной добычной и доставочной техники, эффективных способов управления кровлей и другими процессами.
Развитие подземного способа разработки тонких пологих пластов сопровождается постоянно растущей энерго- и материалоемкостью добычи угля, увеличением расходов на его транспортирование. Вопрос разработки тонких пластов в Карагандинском бассейне имеет и специальный аспект: в связи с углублением горных работ и выемкой пластов малой мощности престиж шахтерского труда снижается.
Даже краткий анализ современного состояния разработки тонких пластов показывает необходимость промышленных испытаний нетрадиционных способов их разработки, в частности, способов прямого получения энергии из недр через скважины. В настоящее время наиболее проработанными нетрадиционными бесшахтными технологиями, позволяющими преобразовать уголь на месте его залегания в источники тепловой и электрической энергии, являются подземная газификация угля (ПГУ) и подземное сжигание угля
(ПСУ).
По мнению профессора Ю.Ф. Васючкова [182, С.16], под нетрадиционными технологиями разработки угольных месторождений понимаются технологии, основанные на физико-химическом, микробиологическом и волновом (например, электромагнитном, акустическом и др.) воздействии на угольной массив. К таким технологиям относятся: скважинная добыча метана и угля, микробиологический способ борьбы с метаном в шахте, микробиологический способ снижения серосодержания угля, подземное сжигание угольного пласта, скважинный способ получения электроэнергии. Большинство перечисленных технологий основано на воздействии на угольный массив через поверхностные или подземные скважины. Поэтому их (за исключением микробиологического снижения серосодержания угля) можно отнести к скважинным геотехнологиям.
Теоретической основой ПСУ в отличие от ПГУ являются следующие положения:
а) подготовка участка ПСУ блоками с размерами, обеспечивающими
234
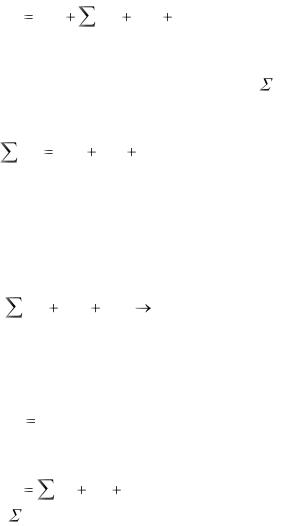
наибольшую полноту сгорания угля при использовании существующей топологии горных выработок [183];
б) всасывающий способ подачи свежего воздуха в инициированный очаг горения с достижением минимально возможных температур газовой смеси на выходе из продуктивной скважины;
в) скважинная подготовка пласта и подземное сжигание небольшого по площади блока с применением способов управления состоянием массива [184]; г) прямое использование физического тепла продуктов горения
угольного пласта непосредственно на поверхности отрабатываемого участка; д) подача свежего воздуха в очаг горения на большие (100 м и более)
расстояния через обрушенные породы выработанного пространства; е) схема направленной подачи свежего воздуха в очаг горения и отвода
горячих газов на поверхность.
По мнению специалистов [185, С. 5-6], при обосновании необходимости применения технологии использования энергии подземного сжигания угольных пластов необходимо произвести следующие расчеты:
1. Тепловой баланс зоны горения, системы выработок (скважин) и поверхностного теплопреобразовательного комплекса (ПТК) можно представить уравнением
Qry Qпол Qпн Qппк Qот , |
(22) |
где Qry —тепло, выделяемое при сгорании 1 т угля в недрах, ГДж; Qпол — удельное полезное физическое тепло, получаемое на выходе из ПТК в виде горячей воды или водяного пара, ГДж/т; пн— удельные потери тепла в недрах, ГДж/т,
Qпн Qпор Qисп Qпр , |
(23) |
Qпop, Qисп и Qпр — удельные потери тепла соответственно на нагревание вмещающих пород, испарение влаги и нагревание породных прослойков с рассеянной минеральной частью угольного пласта, Дж/т; Qппк и Qот — удельные потери тепла в ПТК и с отходящими из теплообменника дымовыми газами, ГДж/т.
2.Главная задача — сведение к минимуму потерь:
( Qпн Qппк Qот ) min . |
(24) |
3. Опыт ПСУ и теория горения угля показывают, что для сжигания 1 м3 углеродного вещества требуется 8-10 м3 воздуха, что позволяет рассчитать расход его на участке Qyч при заданной суточной производительности q:
Qуч (10...12)q /86400. |
(25) |
4.Депрессию тягодутьевого комплекса определяют по формуле
hуч |
hrв hвп hнтк , |
(26) |
где hrb— максимальная депрессия сети выработок, воздухоподающей и
235
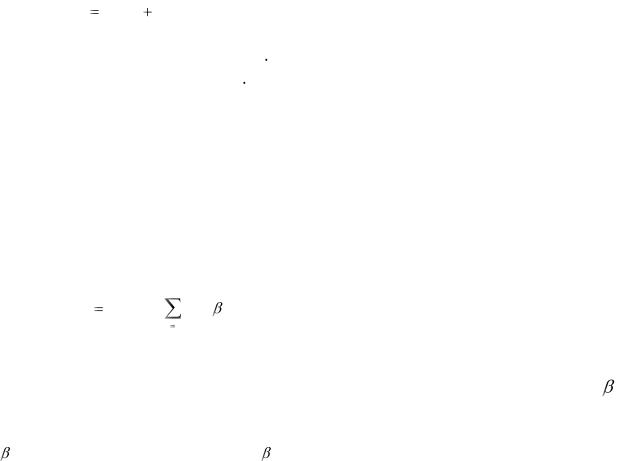
продуктивной (газоотводящей) скважин, Па; hвп — максимальная депрессия выработанного пространства, Па,
h |
R*Q |
R*Q2 |
, |
(27) |
вп |
1 уч |
2 уч |
|
|
R*1— линейное аэродинамическое сопротивление фильтрующей части выработанного пространства, Н с/м5; R*2— квадратичное аэродинамическое сопротивление той же зоны, Н с2/м8; hнтк — максимальная депрессия наземного технологического комплекса, Па.
5. Должна быть разработана методика расчета количества сгоревшего угля по концентрации в исходящей горючей смеси углеродсодержащих газов - оксида углерода, углекислого газа и метана. В основу методики могут быть положены технометрические соотношения реакций окисления и восстановления углеродсодержащих веществ при горении угля, изменение массового расхода газов при повышении их температуры против пластовой и объемное содержание компонентов горючей смеси. Производительность участка по сгоревшему углю рассчитывают по формуле
n |
|
Gуч 0,0144qr (Ci / i ), |
(28) |
i 1 |
|
где qr — массовый расход горючей смеси по продуктивной скважине (стволу), кг/мин; n = 1, 2, 3 — количество углеродсодержащих компонентов в смеси; Сi — объемное содержание i-го компонента в смеси, %; 1— коэффициент, учитывающий вид химической реакции при горении угля и перевод объемного содержания компонентов в массовые, для оксида углерода
CO = 4,67, для углекислого газа CO 2 = 3,67.
Недавно в России (на Камчатке) состоялся запуск Мутновской геотермальной электростанции. В эксплуатацию пущены два энергоблока по 25 МВт, работающие на энергии пара с температурой до 200оС, получаемого из земных недр по двухкилометровой скважине, пробуренной в Мутновское геотермальное месторождение. Обеспечение собственной дешевой электрической и тепловой энергией создало прорыв в энергетике Камчатской области, до этого ежегодно закупающей морские поставки мазута в объеме 900 тыс. т у.т. на дотации из федерального бюджета порядка 45 млн. долл. США в год. Сообщено также, что опыт геотермального энергоснабжения планируется развить на Курилах и в европейской части России как альтернативу традиционной энергетике [186, С.56].
В Карагандинском бассейне и других угольных месторождениях и бассейнах Республики Казахстан геотермальных источников пока не обнаружено. Однако в недрах этих регионов залегают огромные запасы углеродных энергоносителей. Если овладеть технологией их управляемого подземного сжигания и подземного паропроизводства, то можно создать аналогичные камчатскому энергетические комплексы по схеме «вода в недра - пар из недр – электроэнергия – вода в недра». Такой энергокомплекс будет избавлен от необходимости извлечения из недр угля.
10.2 Проведение комплекса работ по созданию и опытно-
236
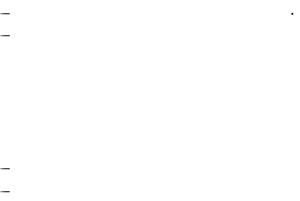
промышленному внедрению технологии использования энергии подземного сжигания пластов
C 1993 г. в Московском государственном горном университете (МГГУ) был проведен цикл научных работ по созданию способа ПСУ в недрах, отличающегося от известной технологии ПГУ более высокими показателями управляемости процесса горения - более высокой степенью отработки запасов, более широким диапазоном регулирования скорости передвижения огневого фронта в недрах, увеличением теплосодержания исходящих газов.
Опытные работы были проведены на полях шахт №1 «Острый» ПО «Селидовуголь» и «Киреевская» ПО «Тулауголь» в 1985-1988 гг., которые позволили установить зависимости передвижения фронта и длину огневого забоя, рациональные режимы подачи воздуха к нему, состав и динамику температуры исходящих газов, степень извлечения запасов угля, разработать технологическую схему огневой отработки оставленных в недрах запасов и целиков угля. Были созданы новые поверхностные комплексы оборудования, позволившие утилизировать тепловую энергию исходящих газов.
На базе указанных промышленных испытаний в 1995 г. была разработана новая технология получения электроэнергии непосредственно на шахтном поле путем подземного сжигания угольного пласта, получения горючих генераторных газов, извлечение метана через поверхностные скважины на этом же шахтном поле, смешение генераторных газов с метаном, получение тепловой энергии от утилизации их тепла и тепла их сжигания, и получения электроэнергии в генераторах комбинированного цикла, используя энергию пара и горючих газов. Технология разработана совместно с научнопроизводственным предприятием «Минерал» (Россия).
По мнению [182, С. 19], данная технология имеет следующие преимущества перед традиционной схемой: шахта (карьер) - ОФ - транспорт - электростанция:
себестоимость выработки 1 кВт ч снижается на 30-50%; удельные капитальные затраты на единицу запасов угля
уменьшаются в 2-3 раза;
эффективность использования геологических запасов угля на шахтном поле возрастает на 30-40%;
исключается выдача пустой породы на поверхность и ее складирование;
исключается обогатительный цикл;
взначительной мере уменьшаются выбросы в атмосферу сернистых
иазотистых соединений, угольной и породной пыли.
Однако дополнительное исследование, проведенное авторами работы [187, С. 58-59], показало, что предложенная МГГУ технологическая схема нагнетально-всасывающего способа ПСУ, позволяющая свести к минимуму потери дутья и продуктов сжигания, обладает одним недостатком. Дело в том, что в этом случае существующие тягодутьевые аппараты не могут обеспечить
237
потребностей технологии ПСУ. Большие резервы повышения тепловой мощности процесса заложены в возможности дожигания горючих компонентов в продуктах ПСУ, не реализуемого при опробованных схемах. Указанные обстоятельства требуют существенной корректировки ранее испытанных схем ПСУ для условий тонких пластов.
По мнению авторов статьи [187], данные недостатки устраняются технологической схемой, позволяющей повысить депрессию тягодутьевого оборудования без неоправданного увеличения производительности и осуществить дожигание горючих газов. Основное отличие новой схемы состоит в использовании эжекционной установки на базе отработавших летный ресурс газотурбинных двигателей с демонтированной силовой турбиной. Эжекционная установка совмещает в себе функции тягодутьевого оборудования и устройства дожигания горючих компонентов.
Предлагаемая схема обеспечивает необходимую потребителям регулируемую мощность (1-3,2 Гкал/ч). Доля энергии от дожигания горючих компонентов и энергия дизтоплива, затраченная на работу эжекторной установки, составляют в балансе тепловой энергии около 50%. Огневой забой предложено разместить в сбойке между наклонными стволами. Первоочередной участок ПСУ рассчитан на отработку в течение 11 лет со средней массовой скоростью сгорания угля Gу = 0,28 кг/с.
Экономическая оценка предложенной технологической схемы ПСУ тонких пластов показала привлекательность инвестиций при процентной ставке до 43%, индекс выгодности предлагаемых решений — от 1,6 до 2,3. Предложенная технологическая схема значительно расширяет возможность подземного сжигания углей, а для регионов, не имеющих альтернативного топлива, является практически единственной [187, С. 59].
Результаты проведенного комплекса работ по созданию и опытнопромышленному внедрению новой технологии получения энергии при подземном сжигании угля позволяют нам сделать важный вывод о перспективах развития Карагандинского бассейна.
10.3Принципы осуществления технологии энергопроизводства при подземном углесжигании в Карагандинском бассейне
Принципиальная схема функционирования энергокомплекса нового поколения может базироваться на [186, С. 56]:
последовательном сжигании нарезаемых в пласте угля столбов (блоков), предварительно изолированных огнестойкими материалами от остального угольного массива;
съеме образующегося в недрах тепла парогенераторами, перемещаемыми по уклонам вслед за огневым фронтом;
выдаче на поверхность по жаростойким трубопроводам пара и трансформации его в электроэнергию на генераторе, передвигающемся по простиранию пласта вслед за последовательно выжигаемыми столбами угля;
238

концентрации электроэнергии от нескольких генераторов, эксплуатирующих свиту угольных пластов, и транспортировании ее по магистральным ЛЭП к энергопотребителям.
На сегодняшний день осуществление технологии энергопроизводства при подземном углесжигании в Карагандинском бассейне видится следующим образом. По падению угольного пласта последовательно проводятся выработки-уклоны на глубину 600-800 м, которые затем сбиваются горизонтальной выработкой - запальным штреком
Ширина нарезанных таким образом столбов составляет 30-60 м и определяется необходимой производительностью парогенераторов, мощностью пласта угля, его калорийностью, температурой горения и т.д. Высота создаваемых выработок соответствует мощности пласта. С целью предотвращения перемещения огневого фронта за пределы блоков почва штрека изолируется огнеупорными материалами (кирпич, бетон, современные негорючие материалы). Вдоль оси каждого уклона по всей их длине возводятся огнестойкие перемычки, разделяющие выработанное пространство на две части. Для повышения безопасности изолирующие сооружения заглубляются в породный массив. Таким образом, в недрах формируются изолированные столбы угля, выступающие в дальнейшем в качестве термогазогенераторов.
Затем на почве уклонов по обе стороны от перемычек монтируются рельсовые дороги для передвижения парогенераторов, представляющих собой цилиндрические котлы на колесах (наподобие железнодорожных цистерн), перемещаемые с поверхностного диспетчерского пункта посредством лебедок. По рельсовым дорогам в уклоны двух первых столбов на уровень запального штрека спускаются парогенераторы и соединяются системой жестких и гибких трубопроводов с электрогенератором (ЭГ) и резервуаром теплоносителя на поверхности. Парогенераторы, трубопроводы, рельсы, канаты и т.д. изготовляются из материалов, выдерживающих образующуюся под землей высокую температуру. Возможна организация контурного съема тепловой энергии сжигаемого угля, когда на первом контуре - в подземном теплообменнике - используются тяжелые жидкости - с температурой кипения около 600 С, отдающие тепло водяному теплоносителю в более безопасной зоне.
С поверхности земли в каждый столб бурятся несколько скважин для подачи воздуха и регулирования процесса сжигания пласта. С целью поддержания высокого температурного режима в зоне нахождения теплообменника уклоны через 100-150 м оборудуются шлюзовыми воротами, управляемыми диспетчером с поверхности. В качестве средств слежения за процессом сжигания угля на несгораемых стенках выработок устанавливаются температурные датчики и другие приборы контроля.
По завершении подготовки нескольких столбов и удалении фронта проходческих работ по простиранию пласта, в столбе запального штрека осуществляют розжиг угольного массива. Контроль за подземным паропроизводством осуществляют в наземном диспетчерском пункте, где с помощью компьютерной программы отслеживают соответствие фактических
239
параметров процесса требуемым. Отслеживают показания температуры в различных точках столбов, контролируют давление и температуру в котлах, современными средствами наблюдения ведут тепловизорную съемку массива и т.п. Оттуда же управляют процессом производства энергии путем регулирования воздухоподачи в различные скважины, передвижения парогенераторов вслед за огневым забоем, перекрытия шлюзовых ворот, регулирования расхода воды и т.д.
По мере выжигания одного столба вводят в действие следующий. При этом на соседнем с запаливаемым столбе все подготовительные работы должны быть завершены, а люди из него должны быть переведены в следующие блоки. Вырабатываемую электрогенератором энергию передают на трансформаторную подстанцию и затем к потребителям. Электрогенератор передвигают в направлении подготавливаемых столбов по простиранию пласта с соответствующим перемонтажем трубопроводов.
При освоении описанной технологии появляется возможность создания на угольном месторождении современного энергетического комплекса с наземно-подземной ТЭС и практически безлюдной технологией получения энергии из недр. Штат такого энергокомплекса включает профессии проходчиков, буровиков, строителей огнестойких перемычек и изоляций, операторов огня и пара, слесарей КИПиА и т.п. Персонал по обслуживанию предлагаемой производственной системы сокращается с численности шахты до численности 2-3 проходческих бригад и бригады буровой установки! Тысячи людей, занятых в настоящее время на профессиях машиниста комбайна, ГРОЗ, электрослесаря и т.п., выводятся из опасных условий труда и высвобождаются для другой созидательной деятельности.
Значит, шахта будущего в Казахстане – уже не система для выдачи углеродного энергоносителя на поверхность, а система для его управляемого преобразования под землей и выдачи на поверхность парообразного энергоносителя, готового для превращения в электроэнергию. Нужно прекратить расходовать огромные средства на добычу угля для энергетики, а пустить часть из них на освоение технологии извлечения тепловой энергии из нетронутых пластов. Сама собой отпадает и необходимость освоения на таких шахтах технологии опережающего удаления метана из угольных пластов как меры повышения безопасности ведения подземных горных работ. Добыча угля как процесс извлечения из недр горной массы существенно сократится и останется для нужд металлургических предприятий, химических заводов, зарубежного рынка.
На начальном этапе реализации предлагаемой технологии расход топлива на единицу электроэнергии, вероятно, будет выше уровня, достигнутого на нынешних угольных ТЭС. Одним из вариантов решения этого вопроса, видимым уже сегодня, может быть перемещение парогенераторов не по фланговым уклонам, а по центральным для двустороннего контакта агрегата с огневым фронтом. Возможно и совместное применение этих схем.
Другим направлением повышения эффективности предлагаемого производства является бурение с поверхности дополнительных скважин и
240