
книги / Справочник по производству хлора, каустической соды и основных хлорпродуктов
..pdfРис. 11-45. Технологическая схема получения перхлората калия обменным раз ложением перхлората натрия с хлористым калием:
/ — приемник растворов |
NaClCb; 2 — каскад |
перхлоратных электролизеров; |
3 — сборник |
рас |
||||
творов |
NaClO^; 4 — первый кристаллизатор |
КСЮ4; 5, |
7, 12 — центрифуги; |
6 — выпарной |
ап |
|||
парат |
для |
маточников |
первой кристаллизации; 8 , 9 |
— растворители |
соответственно КС1 и |
|||
КСЮ<; |
10 — фильтр |
раствора КСЮЧ; / / — второй |
кристаллизатор |
КСЮ4; 13 — сушка. |
Оодстбэ хлорато
Рис. 11-46. Технологическая схема получения перхлората аммония обменным разложением перхлората натрия с аммиаком и соляной кислотой:
1 — бак для приема |
NaCIO* из |
цеха электролиза; |
2 — аппарат |
для |
очистки |
раствора от |
||
хроматов и тяжелых |
металлов; |
3 —аппарат для |
очистки |
раствора |
от хлоратов; 4 — реак |
|||
тор; 5 — кристаллизатор; б —центрифуга кристаллов |
NH4CIO4; |
7 — выпарной |
аппарат для |
|||||
маточных растворов; |
д — центрифуга кристаллов |
NaCl; |
9 — растворитель; |
10 — второй |
||||
|
|
кристаллизатор. |
|
|
|
|
|
61
11-18. Примерные расходные коэффициенты на производство
1 т перхлората аммония:
Перхлорат натрия, кг . |
1050—1100 |
|
Аммиак, к г ............................ |
. |
145—152 |
Соляная кислота |
(32%), к г ................... |
1000—1050 |
Побочный продукт |
(поваренная соль), кг |
500 |
П.ОКИСЛИТЕЛЬНО-ОТБЕЛИВАЮЩИЕ ПРОДУКТЫ
Кнеорганическим хлорсодержащим окислительно-отбеливаю щим продуктам относятся хлорная известь, гипохлориты щелочных
нщелочноземельных металлов, двуокись хлора и хлорит натрия. Во многих странах производство хлорной извести прекращено
почти полностью. В СССР сохранилось производство значитель ного количества хлорной извести в цехах, оборудованных аппара тами Бакмана.
ЕМ9. Основные нормы технологического режима в производстве хлорной извести в аппаратах Бакмана:
Съем с одного аппарата, |
т/сут . . . |
8,5—9,5 |
Содержание в обожженной извести, % |
90—95 |
|
СаО, не менее . . |
. |
|
СаСОз, не более . . |
2—5 |
|
Содержание в пушонке, % |
86-94 |
|
Са(ОН)2 . . |
. |
|
Н20 .... |
|
0,5—3 |
Содержание С12 в абгазах, мг/л |
5—10 |
|
после аппарата, не более. . . . |
||
после санитарной очистки, неболее . |
0,5. |
Выпускаемая хлорная известь содержит 35 и 32% активного хлора, для бытовых нужд выпускается продукт с содержанием 28% активного хлора.
11-20. Примерные расходные |
коэффициенты на производство |
|
1 т хлорной извести (содержание активного хлора 35%): |
||
Известь обожженная (100% СаО), т . |
0,51—0,52 |
|
Хлоргаз (100%), т ................................................... |
. |
0,37—0,38 |
Электроэнергия, кВт-ч |
20—30 |
|
Пар |
|
0,10-0,15 |
Гкал . |
|
|
ГДж . |
|
0,42—0,63 |
Вода, м3 |
|
18—20 |
Стабильная хлорная известь, содержащая не более 2% влаги, производится хлорированием пушонки в аппаратах с кипящим слоем. Съем продукта с одного такого аппарата до 30 т/сут.
Гипохлорит кальция (ГПК) производится в виде нейтральной (НГ) соли, содержащей 50—80% активного хлора, и в виде основ ных солей (двутретьосновной — ДТС и двойной — ДС), содержа щих соответственно 50—60 и 39—43% активного хлора.
62
Предложены и используются различные производственные схе мы получения гипохлорита кальция.
На рис. II-47 приведена схема производства НГ по известково му методу с отжимом массы кристаллов от маточника на прессах
Рис. 11-47. Схема производства нейтрального гипохлорита кальция (НГ) по известковому методу.
под давлением 150 кгс/см2 ( ~ 15 МПа). Необходимость такого пресса обусловлена трудностью отделения кристаллов от маточ ника с высоким содержанием СаС12 путем фильтрования.
11-21. Примерные расходные коэффициенты на производство I т нейтрального (71—73% активного хлора) и основного (61—63% активного хлора) гипохлорита кальция
по известковому методу:
|
Нейтральная |
Основная соль |
|
соль |
|
Хлор (1 0 0 % ), т . |
1 ,2 |
1,1 |
СаО (96—98%), т |
1 ,2 |
1,1 |
Пар |
5 - 6 |
|
Гкал . |
5 — 6 |
|
ГДж |
2 1 - 2 5 |
2 1 - 2 5 |
Чтобы избежать трудностей, связанных с высокой концентра цией СаС12 в маточнике, применяют безотходный известково-кау стический метод производства, при котором можно перерабаты вать фильтрат с получением дополнительно к основному продукту НГ низкопроцентного воднорастворимого гипохлорита кальция (рис. П-48).
На производство 1 т НГ расходуется 1,25 т С12, 1,4 т СаО и 0,6—0,7 т NaOH; в качестве побочных продуктов получают 0,6— 0,7 т низкопроцентного гипохлорита кальция НПГ (содержание 28—30% активного хлора) и около 0,22 т поваренной соли
63
КСЮд |
|
Рис. 11-51. Схема производства двутретьосновной |
соли гипохлорита кальция |
(ДТС). |
|
5—2644 |
65 |
Если требуется получить нейтральный гипохлорит с малым
содержанием нерастворимых в |
воде примесей, применяют схе |
му с высаливанием (рис. II-49) |
или с выпаркой осветленных рас |
творов НГ в вакууме (рис. II-50). В этих схемах при хлорировании получают растворы Са(СЮ) 2 и все нерастворимые примеси от деляются при осветлении хлорированных растворов Са(ОН)2.
Для менее квалифицированных потребителей производят более дешевые продукты ДТС и ДС.
сь
Рис. II-52. С хем а производства двойной соли гипохлорита кальция (Д С ).
На рис. 11-51 показана схема производства ДТС с переработ кой фильтратов до получения бертолетовой соли и концентрирован ных растворов хлористого кальция, а на рис. II-52—схема произ водства ДС.
Для получения гипохлорита кальция, содержащего 40—45% активного хлора, может быть использована схема без производст венных отходов (рис. II-53).
Рис. П-53. У прощ енная схема производства гипохлорита кальция (ГГ1К) по
известково-каустическому м етоду.
На производство 1 т ДТС расходуется 1,6 т обожженной извести и 1 , 5 т хлора, в качестве побочных продуктов выделяют 0 , 1 т бер толетовой соли и 1 , 8 т хлористого кальция.
66
11-22. Примерные расходны е коэффициенты
на производство |
1 т двойной |
соли |
гипохлорита |
кальция |
||
|
(содер ж ан и е 39— 43% |
активного хлора): |
|
|||
И звесть |
обож ж ен н ая |
(100% С аО ), |
т |
1,7 |
||
Х лоргаз |
(100% ), |
т ........................ |
|
|
0 ,7 5 |
|
Кислота |
соляная |
(31% -ная), |
т |
|
1 ,25 |
|
Топливный газ, м3 . . |
. |
|
|
350 |
||
Электроэнергия, |
кВ т-ч . |
|
|
800 |
||
П ар |
|
|
|
|
|
|
Гкал |
|
|
|
|
|
3 ,0 |
Г Д ж |
|
|
|
|
|
12,5 |
В ода, м3 |
|
|
|
|
|
500 |
Технологическая схема производства нейтрального ГПК извест ково-каустическим методом без стадий обжига известняка и гаше ния извести приведена на рис. 11-54.
Рис. 11-54. Технологическая схема производства нейтрального ГПК по извест- ково-каустическому методу:
I — бак для |
приготовления |
раствора |
NaOH; 2, 7 — смесители хлора |
с воздухом; |
3 — хлора |
|||||||||
тор каустической |
соды; 4 — емкость |
для |
NaCIO; |
5 — центрифуга |
для |
отделения |
NaCl; |
|||||||
6 — аппарат |
для |
приготовления |
известково-каустической |
смеси; 8 — хлоратор |
известково- |
|||||||||
каустической |
смеси; |
5 — сборник отхлорированной |
смеси; |
10 — барабанный вакуум-фильтр; |
||||||||||
II — распылительная |
сушилка; |
12 — циклоны; 13 — шиек-холодильиик; |
И — бункер |
для |
||||||||||
низкопроцентного |
ГПК; 15 — ленточный |
транспортер; |
16 —смеситель |
пасты |
с ретуром; |
|||||||||
17 —«питатель; 18 — секционная |
фонтанирующая сушилка; |
15 — циклоны |
для улавливания |
|||||||||||
НГ; 20 — дезинтегратор; 2 / — ленточный транспортер; |
22 — ковшевой |
элеватор; |
23 — шиек- |
|||||||||||
|
|
|
холодильннк; 24 — бункер нейтрального гипохлорита. |
|
|
|
||||||||
Двуокись |
хлора |
получают |
восстановлением |
хлората |
натрия, |
в меньшей степени используют процесс восстановления хлората кальция.
б* |
67 |
/ —бак |
исходного |
хлорнд-хлоратного |
раствора; |
2 — бак |
концентрированной |
соляной кислоты; 3 — фильтры; |
4 |
—теплообменники; 5 — |
|||||||||||||||||
каскад |
реакторов; |
6 —приемник |
отработанного |
хлорид-хлоратного |
раствора; 7 — выпарной |
аппарат; |
8 — барометрический |
конденсатор; |
|||||||||||||||||
9 — выносной |
теплообменник; |
10 — сборник |
упаренной |
пульпы; |
11— центрифуга; |
/2 — приемник |
маточника; 13 — абсорбер — раз- |
||||||||||||||||||
делитель |
смеси |
СЮ2 |
н |
С12; |
14 — приемник |
раствора |
СЮ?; |
15 — подогреватель раствора CIO*; |
76' — охладитель воды; |
17 — при |
|||||||||||||||
емник |
для |
десорбированной |
воды; 18 — десорбер; |
19 — колонна |
дополнительной |
очистки |
от |
CL; |
20 — бак |
циркулирующего |
раствора |
||||||||||||||
NaClOj—NaCl; |
21 — колонна |
для |
получения |
хлорита натрия; |
|
22 — теплообменник; 23 — напорный |
бак раствора |
NaOH; |
24 — напорный |
||||||||||||||||
бак |
НаОа; |
25 — приемник |
раствора |
NaC102; |
26 — напорный бак |
раствора |
NaClO-; |
27 — распылительная |
сушилка; |
28— циклон; |
29— напорный |
||||||||||||||
бак |
NaOH; |
30 — холодильник |
раствора |
гипохлорита |
натрия; |
31 — колонна для |
получения |
;ч1 ПОХлорита |
натрия; |
32 — сборник |
раствора |
||||||||||||||
|
|
|
|
|
NaClO; |
— колонна |
санитарной очистки газов; |
34 — аппарат для разложения следов хлора. |
|
|
|
В качестве восстановителей применяют преимущественно хло ристый водород или двуокись серы. При восстановлении хлората натрия хлористым водородом образующийся NaCl можно исполь зовать для получения хлората натрия, такое производство будет безотходным.
При использовании двуокиси серы в качестве восстановителя получают кислый сульфат натрия, как отход производства.
Хлорит натрия (NaC102) получают поглощением двуокиси хло ра щелочью в присутствии восстановителя (Н20 2, Zn и др.).
На рис. 11-55 приведена технологическая схема получения дву окиси хлора восстановлением хлората натрия хлористым водоро дом, разделения смеси С12 и СЮ2 и получения хлорита натрия
сиспользованием в качестве восстановителя перекиси водорода.
Внародном хозяйстве широко используются растворы гипо хлорита натрия, содержащие 95— 185 г/л активного хлора и ги похлорита кальция, содержащего 85— ПО г/л активного хлора. Эти растворы получают хлорированием растворов NaOH или известко вого молока. Могут быть также использованы фильтраты от произ водства гипохлорита кальция.
На производство 1 т раствора гипохлорита натрия (185 г/л активного хлора) расходуется 0,162 т хлора и 0,19 т каустической соды.
12. ХЛОРИДЫ
Промышленностью в больших количествах производятся хлори ды алюминия, кремния, железа, цинка, фосфора и др.
Рис. |
Н-56. |
Технологическая |
схем а производства |
хлористого |
алюминия: |
|||
1 — склад |
каолина; 2 —бункер |
для глинозема; 3 — бегуны; |
4 — брикетная |
машина; 5 — су |
||||
шилка; |
6 — печь |
прокаливания; |
7 — печь хлорирования; |
S — холодильник; |
9 ~ шламоотде- |
|||
лнтель; |
10— разлагатель шлама; И, |
14 — конденсаторы; |
12, 15 — ловушки; 13 --сублима |
|||||
|
|
|
тор; 16 — камера для разложения отходящих газов. |
|
Хлористый алюминий получают хлорированием каолина в при сутствии глинозема (рис. 11-56). Разрабатываются также способы получения хлористого алюминия хлорированием металлического алюминия.
69
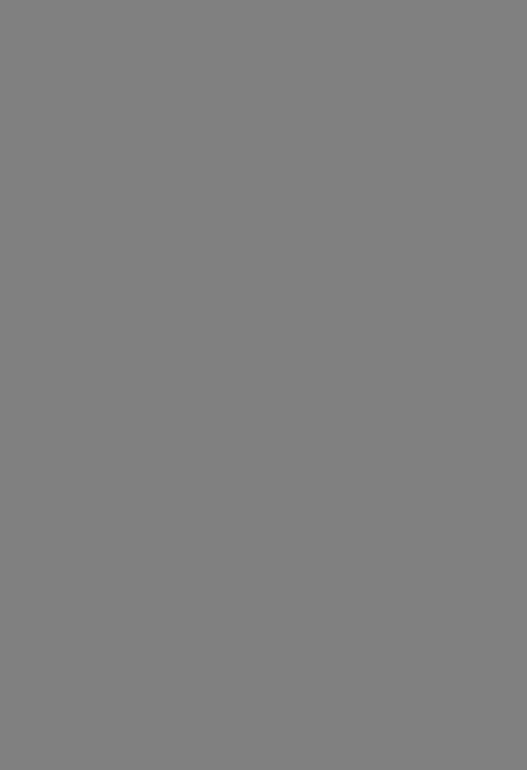