
Методические указания
.pdf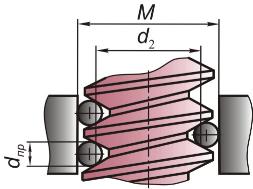
3. Поместить две проволочки во впадины резьбы со стороны микрометрического винта и одну проволочку — со стороны пятки (рис. 27). Нужно следить, чтобы проволочки касались резьбы доведенными поверхностями. Измерить расстояние М в трех сечениях, перпендикулярных оси изделия.
Рисунок 27. Схема измерения среднего диаметра
4. Вычислить средний диаметр резьбы:
d2 =M −3dпр +0,866P ,
где dпр — диаметр проволочек.
5. Построить схему расположения полей допусков по среднему диаметру (рис. 28). Для этого по ГОСТ 24705 – 81 “Резьба метрическая. Основные размеры” или по формуле:
D2 = D – 0,649519053P,
где D — наружный диаметр гайки, определить средний диаметр гайки. По ГОСТ 16093 – 81 “Резьба метрическая. Допуски” (приложение 5) определить допуск на средний диаметр гайки. По ГОСТ 24997 – 81 “Калибры для резьбы. Допуски” (приложение 6) определить допуск на изготовление и износ резьбового проходного калибра-пробки.
31
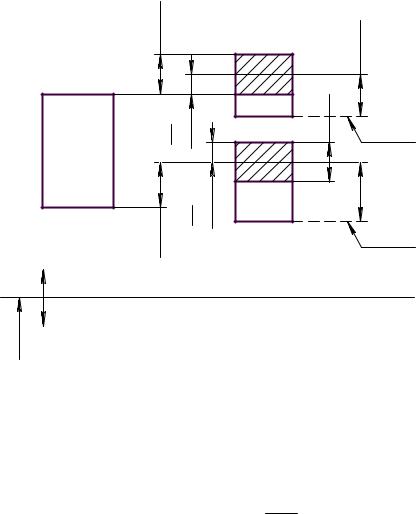
|
=14PLT |
|
|
ÍÅ |
|
W=15NG |
+268 |
|
|
|
|
||
|
|
|
|
|
|
|
TD2 |
=7 |
|
ÏÐ |
TPL=14 |
Предел |
|
TPL |
2 |
|
||||
7G |
|
|
|
|
|
износа |
|
|
|
|
|
|
|
|
|
=7 |
|
|
|
|
+32 |
ZPL=16 |
TPL |
2 |
|
|
Предел |
|
|
|
||||
ìêì |
|
|
|
|
|
износа |
+ |
|
|
|
|
|
0 |
0 |
|
|
|
|
|
|
- |
|
|
|
|
|
|
D2=13,026 ìì |
|
|
|
|
|
|
Рисунок 28. Схема расположения полей допусков по среднему диаметру гайки и резьбового калибра-пробки
6. Подсчитать исполнительный размер проходного калибра-пробки по среднему диаметру.
d2 =(D2 +EID2 +ZPL +TPL2 )−TPL
7.Дать заключение о годности калибра.
32
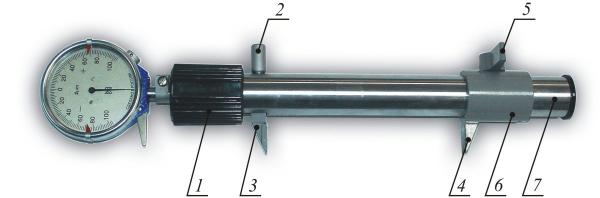
КОНТРОЛЬ ЦИЛИНДРИЧЕСКИХ ЗУБЧАТЫХ КОЛЕС
РАБОТА №9
ИЗМЕРЕНИЕ ДЛИНЫ ОБЩЕЙ НОРМАЛИ ЗУБЧАТОГО КОЛЕСА НОРМАЛЕМЕРОМ
Точность зубчатых колес (ГОСТ 1643 – 81) задается степенями точности по нормам кинематической точности, плавности работы и контакта зубьев, а требования к боковому зазору – видом сопряжения и видом допуска на боковой зазор. В чертежах зубчатых колес их точность может быть обозначена, например, 8-B (ГОСТ 1643 – 81) или при комбинировании разных степеней точности – 8-7-7-Ba.
Для зубчатых колес автомобильного и тракторного машиностроения обычно устанавливаются следующие параметры контроля:
по нормам кинематической точности (комплекс параметров):
Fir" — колебание измерительного межосевого расстояния за оборот колеса; FvWr — колебание длины общей нормали на одном зубчатом колесе;
по плавности работы fir" — колебание межосевого расстояния на одном зубе;
по контакту зубьев — пятно контакта (%);
по боковому зазору и его допуску EWmr — отклонение средней длины общей нормали от номинального значения.
Параметры Fir" , fir" и пятно контакта для зубчатых колес 7 степени точности и
грубее могут быть измерены на межцентромере (КПД–300, КПД–400, МЦ–400,
МЦ–400Э, МЦ–160М, МЦ–50, БВ–5077), а FvWr , EWmr — нормалемером.
Нормалемер (рис. 29) представляет собой трубку 7, на которой установлена разрезная втулка 6 с неподвижной измерительной губкой 4 и корпус 1 с подвижной измерительной губкой 3. Перемещения губки 3 передаются на индикатор через рычаг с i = 2 : 1, что обеспечивает цену деления прибора 0,005 мм.
Рисунок 29. Нормалемер
33

Нажатие на арретир 2 позволяет отводить измерительную губку 3 на 1-2 мм. Разрезную втулку 6 можно переместить по штанге при помощи флажка 5, поворачивая его в сторону перемещения. Нормалемер настраивают по концевым мерам длины.
Концевые меры длины являются особо точным измерительным инструментом, применяемым в промышленности для контроля размеров, для проверки и градуировки мер, измерительных приборов и инструментов, для проверки калибров, для установления правильных размеров при изготовлении инструментов, приспособлений и штампов, а также для особо точных разметочных работ и наладки станков.
Концевые плоскопараллельные меры длины представляют собой прямоуголь-
ные стальные (или твердосплавные) плитки, размеры которых определяются расстоянием между двумя рабочими плоскостями при температуре 20ºC. Рабочие плоскости плитки — самые чистые. Характерной особенностью концевых мер длины является их притираемость друг к другу измерительными поверхностями. Притираемость дает возможность из одного набора мер составлять комбинации размеров.
Приступая к работе, следует предварительно рассчитать, какие меры надо взять для данного блока. Количество концевых мер длины в блоке должно быть минимальным, так как погрешность блока складывается из погрешностей отдельных мер. Притирку мер в блок надо проводить в определенной последовательности: к мерам больших размеров последовательно притирают меры меньших размеров, причем меньшую меру накладывают на край большей. Затем зигзагообразными движениями верхнюю меру двигают вдоль длинного ребра нижней меры до совпадения плоскостей обеих мер. Размер блока определяется как сумма размеров составляющих его концевых мер.
Порядок выполнения работы
1. Проставить размеры на эскизе зубчатого колеса и определить его данные. а) Измерить штангенциркулем наружный диаметр колеса da и ширину вен-
ца.
б) Подсчитать число зубьев z.
в) Подсчитать модуль m = zd+a2 и округлить до ближайшего стандартного
(приложение 7).
г) Подсчитать диаметр делительной окружности d = m·z.
д) По заданной точности, модулю и диаметру определить по таблицам ГОСТ
1643 – 81 (приложение 8, табл. 8.1, 8.2, 8.3) Fi" , fi" , FvW , пятно контакта в %.
е) Подсчитать число зубьев, охватываемых губками нормалемера при измерении длины общей нормали, округлив его до ближайшего целого:
n = 0,11·z + 0,5.
34
ж) Подсчитать длину общей нормали:
W = [1,476(2n – 1) + z·0,01387]m.
з) Определить допустимые отклонения длины общей нормали по таблицам ГОСТ 1643 – 81:
EWmsI — слагаемое I (приложение 8, табл. 8.4); EWmsII — слагаемое II
(приложение 8, табл. 8.5)— определяется в зависимости от радиального биения зубчатого венца Fr (приложение 8, табл. 8.1); TWm — допуск на среднюю длину
общей нормали (приложение 8, табл. 8.6). Наименьшее отклонение средней длины общей нормали:
EWms =EWmsI +EWmsII .
Наибольшее отклонение средней длины общей нормали:
(EWms +TWm )
Все полученные из таблиц и расчетов данные записать в соответствующие графы журнала лабораторных работ.
2. Измерить колебания длины общей нормали и отклонения длины общей нормали от номинального ее значения. Вставить индикатор в гнездо корпуса 1 так, чтобы малая стрелка стала на цифре 1. Закрепить винтом. Собрать блок концевых мер, равный номинальному значению длины общей нормали W, подсчитанному ранее. Поместить его между губками 3 и 4 нормалемера, для чего переместить разрезную втулку 6 по трубке с помощью флажка 5. Создать натяг в дватри оборота (малая стрелка должна быть около цифр 3-4), установить стрелку индикатора на 0.
Заметить при этом положение малой черной стрелки индикатора. Записать в журнал отклонения стрелки при последовательном измерении длины общей нормали на всех зубьях проверяемого колеса. Направление и знак отклонений определить по смещению (к большим или меньшим значениям) малой стрелки относительно ее положения при настройке. Колебание длины общей нормали FvWr оп-
ределить как разность между наибольшим и наименьшим отклонениями прибора. Определить отклонение длины общей нормали как среднее арифметическое отклонение прибора. Действительная средняя длина общей нормали Wmr опреде-
лится как сумма размера блока плиток и среднего отклонения. Сравнить его с предельными размерами Wmax и Wmin длины общей нормали и дать заключение
о годности. Дать заключение о годности зубчатого колеса в целом и заполнить все графы выводов.
35
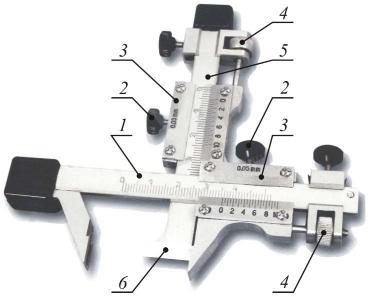
РАБОТА №10
ИЗМЕРЕНИЕ ТОЛЩИНЫ ЗУБА ПО ПОСТОЯННОЙ ХОРДЕ ШТАНГЕНЗУБОМЕРОМ
Наличие бокового зазора в зубчатой передаче — одно из важнейших требований для ее работоспособности. Величина бокового зазора в передаче зависит от толщины зубьев зубчатых колес. В свою очередь, требуемая толщина зубьев достигается соответствующей установкой обрабатывающего инструмента относительно оси заготовки.
Рисунок 30. Штангензубомер
Для проверки толщины зуба в мелкосерийном и единичном производстве у зубчатых колес 9–12 степеней точности обычно используют штангензубомеры кромочные (рис. 30), определяющие толщину зуба по постоянной хорде Sc (рис.
31).
Постоянной хордой Sc называется хорда между точками касания исходного
контура с профилем зуба. Положение и длина этой хорды зависят только от модуля m зубчатого колеса и для некорригированного зубчатого колеса с α = 20º:
Sc =1,387m ; hc =0,7476m .
Штангензубомер кромочный (см. рис. 30) состоит из вертикальной 5 и горизонтальной 1 штанг, по которым перемещаются рамки с нониусами 3, устройствами для микроподачи нониуса 4 и стопорными винтами 2. К рамке нониуса вертикальной штанги прикреплена опорная планка 6.
36
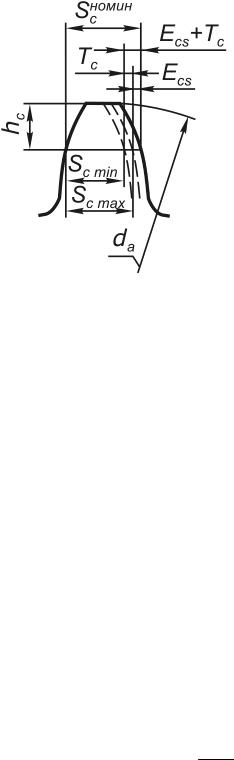
Рисунок 31. Определение толщины зуба по постоянной хорде
Шкала на горизонтальной штанге служит для измерения толщины зуба, на вертикальной – для измерения этой толщины на определенном расстоянии от окружности выступов. Показания на шкалах штангензубомера читаются так же, как и на обычном штангенциркуле.
Технические характеристики штангензубомера |
|
Диапазон модулей контролируемых колес, мм .......................................... |
1…18 |
Диапазон измерений, мм: |
|
по горизонтальной шкале .................................................................. |
0…33 |
по вертикальной шкале ...................................................................... |
0…23 |
Цена деления, мм ............................................................................................ |
0,02 |
Порядок выполнения работы |
|
1. Измерить штангенциркулем наружный диаметр da |
выданного зубчатого |
колеса, ширину колеса и диаметр посадочного отверстия.
2.Подсчитать число зубьев z.
3.Подсчитать модуль m зубчатого колеса m = zd+a2 и округлить результат до
стандартного значения по ГОСТ 9563 – 60 “Колеса зубчатые. Модули” (приложение 7).
4. Подсчитать по формулам или определить по справочнику номинальные значения толщины зуба по постоянной хорде Sc и высоту зуба до постоянной
хорды hc .
5. По ГОСТ 1643 – 81 “Передачи зубчатые цилиндрические. Допуски” определить:
37
− Радиальное биение зубчатого венца относительно оси вращения колеса Fr
(приложение 8, табл. 8.1);
− Наименьшее (верхнее) отклонение толщины зуба Ecs (приложение 8, табл.
8.4);
− Допуск на толщину зуба по постоянной хорде Tc (приложение 8, табл.
8.6);
− Подсчитать наибольшее (нижнее) отклонение толщины зуба как Ecs +Tc (см. рис. 31). Значение Ecs взять по модулю.
6. Подсчитать предельные значения толщины зуба по постоянной хорде (см.
рис. 31):
Sc max =Sc −Ecs ; Sc min =Sc −(Ecs +Tc ) .
7. Замерить штангензубомером толщину зуба по постоянной хорде на пяти расположенных рядом зубьях колеса.
Для этого на вертикальной штанге 5 (см. рис. 30) установить значение высоты зуба до постоянной хорды hc и закрепить рамку нониуса в этом положении
стопорным винтом 2.
Опорную планку 6 установить на наружный диаметр колеса и измерить толщину зуба Scдейств.
8. Сравнить результаты измерения с предельными значениями толщины зуба
Sc max и Sc min .
При Sc max ≥ Scдейств ≥ Sc min требуемый боковой зазор в передаче будет обеспечен, зубчатое колесо годно.
38
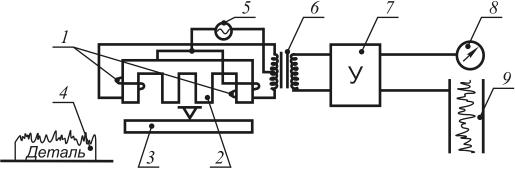
КОНТРОЛЬ ШЕРОХОВАТОСТИ ПОВЕРХНОСТИ
Шероховатостью поверхности называют совокупность неровностей с относительно малыми шагами, образующих рельеф поверхности детали и рассматриваемых в пределах базовой длины.
Количественно шероховатость поверхности по ГОСТ 2789 – 73 может быть оценена одним из шести параметров: Rz , Ra , Rmax , S, Sm , tp . Параметр Rz — это высота неровностей по десяти точкам (среднее расстояние между находящимися в пределах базовой длины пятью высшими точками выступов и пятью низшими точками впадин).
РАБОТА №11
ОПРЕДЕЛЕНИЕ ПАРАМЕТРОВ ШЕРОХОВАТОСТИ ПО ПРОФИЛОГРАММЕ
Принцип работы профилографа-профилометра модели 201 основан на ощупывании исследуемой поверхности алмазной иглой и преобразовании колебаний иглы в измерения напряжения индуктивным методом.
Алмазная игла 4 (рис. 32) перемещается по поверхности детали. Ее колебания с помощью датчика, состоящего из сердечника 2, катушек 1, коромысла 3, преобразуются в колебания напряжения на выходе трансформатора 6. При проходе колебаний через усилитель 7 они фиксируются показывающим устройством 8 или записываются с некоторым увеличением на профилограмме с помощью записывающего устройства 9.
Рисунок 32. Схема прибора
Вертикальное увеличение Vy профилограммы зависит от коэффициента уси-
ления усилителя, изменяется в пределах от 1000x до 20000x и выбирается наибольшим допустимым для данной ширины бумажной ленты.
Горизонтальное увеличение профилограммы Vx зависит от соотношения скоростей перемещения датчика со щупом Vдпо измеряемой поверхности и бумажной ленты Vл в записывающем устройстве:
39
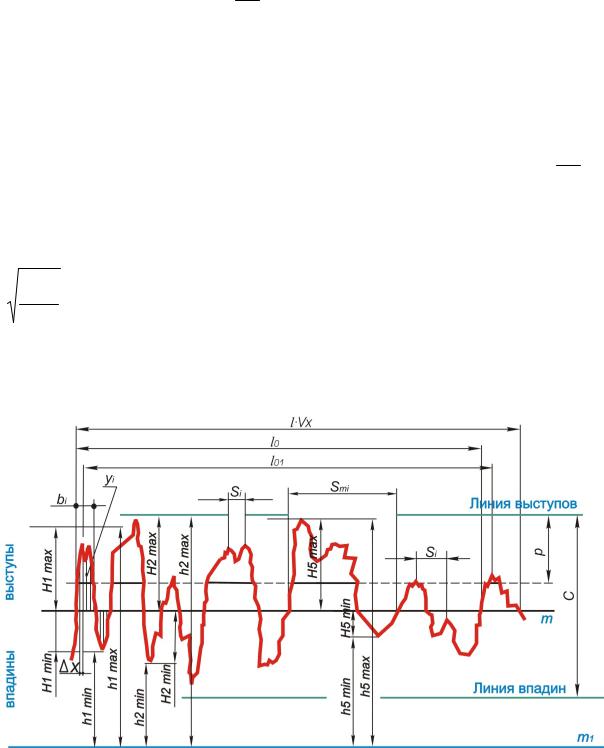
Vх =Vл (от 2x до 4000x ).
Vд
Vx выбирается так, чтобы угол наклона боковых сторон профиля был не бо-
лее 80º (рис. 33).
Порядок обработки профилограммы
1. Определение горизонтального увеличения Vx . Из соотношения Vл опре-
Vд
деляем Vx .
2. Определение положения средней линии m на участке базовой длины l. Точное положение средней линии находится по способу наименьших квадратов,
т.е. ∑nyi2 min на базовой длине (рис. 33). Средняя линия также может быть
проведена “на глаз”, по равенству площадей неровностей над и под линией в пределах базовой длины. На выданной профилограмме провести среднюю линию “на глаз”.
Рисунок 33. Профилограмма
3. Выбор участка измерения. Для надежности оценки параметра измерения обычно проводят последовательно на нескольких базовых длинах и затем находят среднее значение параметра. В целях сокращения трудоемкости работы измерения производим для одной базовой длины.
40