
книги / Оборудование для производства полупроводниковых диодов и триодов
..pdfЛИНИИ ДЛЯ ПРОИЗВОДСТВА ТРАНЗИСТОРОВ ПО ПЛАНАРНОЙ ТЕХНОЛОГИИ
Как уже отмечалось выше, состав обору |
нологического процесса, что облегчает подбор |
||||
дования линии, ее строение, характер межопе |
и комплектование линий имеющимся и серий |
||||
рационного транспорта во многом зависят от |
но выпускаемым оборудованием. |
линии |
|||
технологического процесса, осуществляемого |
Ниже |
приводится |
описание |
||
на линии. |
(рис. 20-1) для сборки приборов типа 2Т301— |
||||
Одним из основных требований, предъяв |
2Т301Ж, изготовляемых по планарной техно |
||||
ляемых к технологическому процессу линии, |
логии. Кроме этих приборов, при незначитель |
||||
является его универсальность, что позволяет |
ной доработке |
оборудования, обусловленной |
|||
при незначительной доработке оборудования |
различными габаритами приборов, на линии |
||||
осуществлять выпуск с линии нескольких ти |
можно организовать выпуск таких приборов, |
||||
пов приборов, т. е. превращать линию в мно |
как П307—309. |
линии сборки происходит сле |
|||
гопредметную. Таким свойством обладает пла |
Работа |
на |
нарная технология, которая широко приме |
дующим |
образом. Кристаллы |
(структуры) |
няется в настоящее время в производстве |
с участка диффузии в кассетах и в герметизи |
||
полупроводниковых диодов и триодов. |
рованной |
таре передаются в |
скафандр за |
|
Планарную |
технологию |
можно |
применять |
грузки |
2 герметизированного |
транспортера. |
|||||||||||||||||
также в сочетании с другими вариантами тех |
Поступление кассет в транспортер и раздача |
|||||||||||||||||||||||
|
□— й — |
0------------ п ---------------- ° --------------п -------------- п |
|
0 |
|
|
^ |
|
||||||||||||||||
|
|
|
а |
|
ш |
в |
|
а |
_ |
|
|
|
” ав1В1ВВВй1В1й01 |
|
||||||||||
|
_ |
• 1Г Ш Н 1Г 1 Г 3 |
|
|
|
т Ш И ш т а |
|
|||||||||||||||||
|
|
|
|
|
|
|
|
|
|
|
|
____________________________ _| |
|
|||||||||||
|
□---------------□---------------п — |
|
10 |
|
|
|
иВЖЖЯ ИиИшИшИ |
|
|
|
||||||||||||||
|
ВВВВВВВВ |
ЕЕ- |
|
|
|
|
|
|
|
|
||||||||||||||
|
|
|
|
|
|
|
|
|
|
|
|
|
|
|
|
|
||||||||
|
|
|
|
|
|
|
|
|
|
|
ш Щ |
|
[ М ] 0 0 0 Ш 0 |
ЕИ0 |
|
|||||||||
|
|
Г7П СЖ] |
|
|
|
|
|
|
|
|
|
|
|
|
|
|
|
|
|
|
|
|
|
|
|
I " |
|
ц |
|
|
|
п~ |
|
I |
ц |
|
|
|
ТГ |
|
|
|
|
|
|
|
|
||
|
№ шш1 |
г п т п л |
|
|
|
го_ 1 |
Гл~1 |
|
|
|
|
|
|
|
|
|
||||||||
|
|
НИ |
|
га га |
га |
|
|
|
|
|
|
т \гРтг т |
т |
|
ш |
|
|
|
||||||
Рис. 20-1. Линия для производства транзисторов по планарной |
технологии. |
|
|
|
|
|
|
|
||||||||||||||||
/ — |
транспортер герметизированный; |
/Я — |
пульт управления |
транспортером; |
2 — скафандр |
загрузки-выгрузки транспортера; |
3 — 1 |
|||||||||||||||||
полуавтомат |
напайки на ножку; |
4 — |
транспортер |
герметизированный; |
4П — |
пульт управления; 5— |
установка |
термокомпрессяи; |
||||||||||||||||
б — |
установка |
разбраковки |
приборов; |
7 — |
печь |
термообработки; |
в — установка |
нанесения |
защитного |
покрытия; |
9 — терморадна- |
|||||||||||||
цнонная печь; 10 — |
установка |
разбраковки |
приборов; I I — |
полуавтомат |
герметизации; |
12 — |
полуавтомат разбраковки |
ножки собран |
||||||||||||||||
ной; |
12П — пульт управления |
к |
полуавтомату |
разбраковки |
ножки |
собранней; 13 — бомба |
опрессовки; |
14 — |
автомат |
контроля |
гер |
|||||||||||||
метичности; 15— автомат циклировання; |
16 — сушильный шкаф; 17 — |
установка |
химического |
никелирования; |
18 — |
монтажный |
стол; |
|||||||||||||||||
19 — |
полуавтомат лужения |
выводов; |
20 — |
классификатор; |
21 — |
установка |
маркировки; |
22 — установка |
проверки |
стабильности |
при |
|||||||||||||
температуре |
120° С; |
22П — |
пульт |
управления к |
установке |
проверки |
стабильности; 23 — |
пульт контроля технологических сред линии; |
||||||||||||||||
24 — |
пульт управления ритмом линии. |
|
|
|
|
|
|
|
|
|
|
|
|
|
|
|
|
|
приборов осуществляются с помощью автома |
азотом, а затем разгружается в скафандр |
||||||||||||||||||||||||||
тически выдвигающегося шлюза. |
|
|
|
полуавтомата. В полуавтомате напайки меха |
|||||||||||||||||||||||
|
Установки, |
объединенные конвейером, при |
низированная |
присоска |
перекладывает |
кри |
|||||||||||||||||||||
соединены к нему с помощью герметичных ре |
сталлы из кассеты на ножки. Пайка |
осуще |
|||||||||||||||||||||||||
зиновых |
амортизаторов. Включение, выключе |
ствляется |
золотом. С полуавтомата |
напайки |
|||||||||||||||||||||||
ние конвейера и задание программы адресной |
ножки с переходами в передвижном контейне |
||||||||||||||||||||||||||
раздачи кассет с обрабатываемыми приборами |
ре |
поступают |
во |
входной скафандр |
второго |
||||||||||||||||||||||
в |
соответствующие |
установки |
производятся |
герметизированного конвейера 4 (также с ад |
|||||||||||||||||||||||
с помощью главного пульта управления |
кон |
ресной раздачей), откуда приборы в ка-ссетах |
|||||||||||||||||||||||||
вейером 1П. Управление адресной раздачей |
поступают |
на |
установки |
термокомпрессионно |
|||||||||||||||||||||||
кассет каждого из двух независимых потоков |
го |
присоединения |
электродных |
алюминиевых |
|||||||||||||||||||||||
может также производиться с помощью пуль |
выводов к кристаллам и траверсам ножек. |
||||||||||||||||||||||||||
тов-дублеров 1 и 4, расположенных во вход |
Подача алюминиевой проволоки с заготови |
||||||||||||||||||||||||||
ных |
(по |
ходу |
технологического |
процесса) |
тельных участков осуществляется в гермети |
||||||||||||||||||||||
установках |
2, |
которые |
одновременно |
выпол |
зированной |
таре |
и |
|
передвижном |
контейне |
|||||||||||||||||
няют роль установок сушки и межоперацион |
ре, который стыкуется со шлюзом установки |
||||||||||||||||||||||||||
ных накопителей приборов. |
|
|
|
|
термокомпрессии 5 и продувается кондици |
||||||||||||||||||||||
|
Каждая установка имеет механизм пере |
онированным |
газом |
|
(в |
данном |
случае |
азо |
|||||||||||||||||||
дачи кассеты |
|
с |
ленты |
конвейера |
в |
соответ |
том). |
|
|
|
|
|
|
|
|
|
|
|
|||||||||
ствующую установку и обратно, который |
вы |
|
Ножки с приваренными_,выводами после |
||||||||||||||||||||||||
полнен в виде качающегося шибера-маятника, |
визуального контроля на установке 6 по |
||||||||||||||||||||||||||
установленного на валу реверсивного двигате |
даются на термообработку в атмосфере кисло |
||||||||||||||||||||||||||
ля. На шибере-маятнике установлен микро |
рода 7, а затем после выборочного контроля |
||||||||||||||||||||||||||
переключатель двигателя, |
который управляет |
по параметрам /ко, /эо и р при помощи пере |
|||||||||||||||||||||||||
ся |
движущейся |
на ленте |
кассетой |
через |
ры |
движного контейнера в кассетах передаются |
|||||||||||||||||||||
чаг, шарнирно закрепленный на шибере. |
|
на установки 8 нанесения защитного покры |
|||||||||||||||||||||||||
|
Механизм |
|
передачи |
работает |
следующим |
тия эмалью КО-97. Защищенные ножки с пе |
|||||||||||||||||||||
образом: по сигналу с пульта управления кон |
реходами сушатся |
в |
терморадиационной |
пе |
|||||||||||||||||||||||
вейером |
|
шибер-маятник |
соответствующей |
чи 9. |
|
|
|
|
|
|
|
|
|
|
|
||||||||||||
установки |
ставится |
в |
исходное |
положение. |
де |
Терморадиационная печь выполнена в ви |
|||||||||||||||||||||
При движении |
кассеты с приборами на ленте |
металлического |
теплоизолированного |
ко |
|||||||||||||||||||||||
конвейера она нажимает рычаг, который взаи |
жуха, образующего рабочий объем, в котором |
||||||||||||||||||||||||||
модействует |
с |
микропереключателем, |
вклю |
расположены |
нагреватели с рефлекторами и |
||||||||||||||||||||||
чается |
электродвигатель |
механизма |
раздачи |
шаговый транспортер. Регулировкой |
нагрева |
||||||||||||||||||||||
и кассета шибером подается на рабочую пло |
телей по высоте печи достигают требуемой |
||||||||||||||||||||||||||
щадку установки. По окончании обработки |
температуры |
сушки. |
Изменением |
|
скорости |
||||||||||||||||||||||
приборов оператор ставит кассету на рабочую |
перемещения |
шагового транспортера |
устанав |
||||||||||||||||||||||||
площадку шлюза и подает сигнал диспетчеру |
ливают временной режим сушки. Вход и вы |
||||||||||||||||||||||||||
пульта |
|
управления |
конвейером. |
Диспетчер |
ход печи выполнены в виде герметизирован |
||||||||||||||||||||||
включает механизм передачи кассеты из соот |
ных скафандров, |
одновременно |
выполняющих |
||||||||||||||||||||||||
ветствующей |
установки, |
и кассета выдается |
роль межоперационных |
накопителей |
прибо |
||||||||||||||||||||||
на ленту конвейера, а шибер-маятник остается |
ров. Скафандры |
сообщаются |
с рабочим |
объ |
|||||||||||||||||||||||
в исходном положении до прихода следующей |
емом печи через окна с крышками. Рабочая |
||||||||||||||||||||||||||
кассеты. |
|
конвейера |
состоит |
из |
отдельных |
атмосфера — очищенный и осушенный до тем |
|||||||||||||||||||||
|
Кожух |
пературы росы —60° С воздух. Из |
выходного |
||||||||||||||||||||||||
секций, что позволяет менять число установок |
скафандра |
терморадиационной |
печи |
приборы |
|||||||||||||||||||||||
(в зависимости от потребности), объединенных |
в |
передвижном |
контейнере |
последовательно |
|||||||||||||||||||||||
конвейером. |
|
|
|
|
|
|
|
|
|
|
транспортируются |
на |
установки |
разбраковки |
|||||||||||||
|
Кассеты с годными кристаллами передают |
по внешнему виду 10 и на полуавтомат гер |
|||||||||||||||||||||||||
ся конвейером на полуавтомат напайки пере |
метизации 11. |
|
|
|
|
|
|
|
|
|
|
||||||||||||||||
ходов на ножки 3, в котором укладка кристал |
|
Таким образом, вся сборка, от напайки |
|||||||||||||||||||||||||
лов на ножки, находящиеся в гнездах карусе |
кристаллов |
до герметизации |
приборов вклю |
||||||||||||||||||||||||
ли, |
производится |
с помощью |
механизирован |
чительно, осуществляется в среде кондициони |
|||||||||||||||||||||||
ной присоски. Ножки приборов из заготови |
рованного, т. е. очищенного от пыли и масла |
||||||||||||||||||||||||||
тельного цеха поступают на полуавтомат на |
воздуха или азота, осушенных до степени, со |
||||||||||||||||||||||||||
пайки в герметизированной таре в передвиж |
ответствующей точке росы (—30°)— (—40°) С, |
||||||||||||||||||||||||||
ном контейнере, который далее стыкуется со |
и с содержанием кислорода не более 0,0005%. |
||||||||||||||||||||||||||
шлюзом |
полуавтомата |
напайки, продувается |
Герметизированные |
приборы |
из полуавтома |
та герметизации удаляются через шлюз и |
и |
контроль |
качества |
технологических |
сред, |
|||||||||||||||||||||
передвижной |
|
контейнер; |
дальнейшая |
транс |
используемых в линии. Контроль ритма произ |
|||||||||||||||||||||
портировка осуществляется вручную в кас |
водится следующим образом: на пульте управ |
|||||||||||||||||||||||||
сетах. После проверки электрических па |
ления для каждого рабочего места установлен |
|||||||||||||||||||||||||
раметров |
на |
|
установке |
12 |
герметизирован |
задатчик ритма, которым задается |
требуемая |
|||||||||||||||||||
ные |
|
транзисторы |
опрессовываются |
|
в |
ге |
производительность. |
Сигналы |
с |
задатчика |
||||||||||||||||
лии на установке 13, затем подвергаются кон |
ритма поступают на счетчики пульта управле |
|||||||||||||||||||||||||
трольным и испытательным операциям соот |
ния и рабочего места. |
|
|
|
|
|
|
|
||||||||||||||||||
ветственно |
на |
полуавтомате |
проверки |
герме |
|
На наиболее характерных узловых рабо |
||||||||||||||||||||
тичности |
14 |
с |
применением |
гелиевого |
тече- |
чих местах линии установлены датчики, с по |
||||||||||||||||||||
искателя, на установках проверки ударопроч |
мощью |
которых |
производится |
качественная |
||||||||||||||||||||||
ности и вибропрочности с контролем коротких |
оценка |
всех изделий |
по принципу |
|
«годен — |
|||||||||||||||||||||
замыканий и обрывов выводов. Затем прибо |
брак». Счетчики установлены на пульте управ |
|||||||||||||||||||||||||
ры подвергаются воздействию трех термоци |
ления и на рабочих местах. |
Таким |
|
образом, |
||||||||||||||||||||||
клов |
при |
крайних |
температурах —60° С и |
производится учет плановой и фактической |
||||||||||||||||||||||
+ 120° С |
на |
полуавтомате |
термоциклирования |
производительности, а также годных изделий |
||||||||||||||||||||||
15. Приборы, не выдержавшие термоциклов, |
с нарастающим итогом. Сравнение показаний |
|||||||||||||||||||||||||
отбраковываются при повторной проверке гер |
счетчиков дает представление о ритме работы |
|||||||||||||||||||||||||
метичности с помощью гелиевого течеискате- |
оборудования. Показания |
счетчиков |
периоди |
|||||||||||||||||||||||
ля. На установке термостарения 22 приборы |
чески передаются |
на |
автоматическую |
печать |
||||||||||||||||||||||
при температуре 120° С выдерживаются |
в те |
с указанием номера установки и текущего вре |
||||||||||||||||||||||||
чение 96 ч. |
|
|
|
|
|
|
готового прибо |
мени. По записям на бланках (по соотноше |
||||||||||||||||||
Антикоррозионная защита |
нию между |
числом |
годных |
и |
бракованных |
|||||||||||||||||||||
ра (никелирование) производится на установ |
изделий на контрольных операциях) оце |
|||||||||||||||||||||||||
ке химического никелирования 17, после чего |
нивается |
состояние |
технологического |
про |
||||||||||||||||||||||
приборы снабжаются «спутниками» для со |
цесса. |
|
|
|
|
|
|
|
|
|
|
|
||||||||||||||
хранности выводов на монтажном стане 18 и |
|
Счетчики плановой и фактической произво |
||||||||||||||||||||||||
поступают на полуавтомат лужения выводов |
дительности, установленные на рабочем месте, |
|||||||||||||||||||||||||
19 |
и |
далее |
на установку проверки |
|
параме |
позволяют |
оператору |
получать |
представление |
|||||||||||||||||
тров 12. Транзисторы классифицируются на |
о ходе выполнения плана на данном техноло |
|||||||||||||||||||||||||
четыре типономинала |
под шифром |
2Т |
и во |
гическом |
оборудовании. |
Пульт управления |
||||||||||||||||||||
семь типономиналов под шифром КТ на полу |
имеет мнемоническую схему, которая характе |
|||||||||||||||||||||||||
автомате классификации 20, после чего при |
ризует |
состояние установки на |
данное |
время |
||||||||||||||||||||||
боры маркируются на полуавтомате 21. На |
(т. е. работает она или нет), а также телефон |
|||||||||||||||||||||||||
полуавтомате проверки стабильности обратных |
ную диспетчерскую -связь с рабочими местами, |
|||||||||||||||||||||||||
токов |
коллектора 22 при |
Т—130+5° С отбра |
оборудованными пультом оператора, на кото |
|||||||||||||||||||||||
ковываются приборы под шифром 2Т. Затем |
ром установлены счетчики плановой и факти |
|||||||||||||||||||||||||
еще раз |
проверяются |
все классификационные |
ческой производительности, кнопки вызова ди |
|||||||||||||||||||||||
параметры на классификаторе 20, и приборы |
спетчера, микрофон-телефон. |
|
|
|
|
|
||||||||||||||||||||
передаются в ОТК, а затем на упаковку в по |
|
На щите пульта установлены приборы, кон |
||||||||||||||||||||||||
лиэтиленовую пленку. |
|
|
|
|
|
|
тролирующие состояние защитных и техноло |
|||||||||||||||||||
В состав |
комплексно-механизированной ли |
гических сред (содержание кислорода в азо |
||||||||||||||||||||||||
нии входит пульт управления 23, с помощью |
те, влажность газов, давление водопроводной |
|||||||||||||||||||||||||
которого осуществляются |
управление |
линией |
воды). |
|
|
|
|
|
|
|
|
|
|
|
||||||||||||
Г Л А В А Д В А Д Ц А Т Ь П Е Р В X Л |
|
|
|
|
|
|
|
|
|
|
|
|
|
|
|
|
||||||||||
ОСНОВНЫЕ НАПРАВЛЕНИЯ МЕХАНИЗАЦИИ |
|
|
|
|
|
|
|
|
|
|
|
|||||||||||||||
И АВТОМАТИЗАЦИИ ПРОИЗВОДСТВА |
|
|
|
|
|
|
|
|
|
|
|
|
|
|||||||||||||
ПОЛУПРОВОДНИКОВЫХ ПРИБОРОВ |
|
|
|
|
|
|
|
|
|
|
|
|
|
|||||||||||||
21-1. ОСНОВНЫЕ ТЕХНОЛОГИЧЕСКИЕ ЗАДАЧИ |
водникового производства, для которого характерно при |
|||||||||||||||||||||||||
И |
ПРИНЦИПЫ МЕХАНИЗАЦИИ |
|
|
|
менение большого количества специального технологи |
|||||||||||||||||||||
И АВТОМАТИЗАЦИИ |
|
|
|
|
|
|
ческого |
оборудования. Обусловлено |
это |
|
чрезвычайно |
|||||||||||||||
|
|
|
|
|
|
широкой |
номенклатурой |
технологических |
процессов, |
|||||||||||||||||
|
|
|
|
|
|
|
|
|
|
|
|
|
|
|||||||||||||
Полупроводниковое |
машиностроение, |
создающее |
применяемых |
в |
полупроводниковой |
промышленности, |
||||||||||||||||||||
современные машины, комплексно-механизированные и |
необходимостью |
их |
поддержания |
и |
воспроизведения |
|||||||||||||||||||||
автоматизированные линии |
является базой |
|
полупро |
с |
высокой |
точностью. |
Необычайно |
высока |
точность |
изготовления и сборки приборов при миниатюрных раз мерах детален. Ювелирные приемы обработки сочетают ся с высоким уровнем механизации и автоматизации производства, необходимым для обеспечения массового выпуска полупроводниковых приборов. Имеется также ряд других особенностей полупроводникового производ ства, накладывающих свой отпечаток на характер полу проводникового машиностроения.
В настоящее время парк специального технологи ческого и контрольно-измерительного оборудования в полупроводниковом производстве составляет десятки тысяч единиц установок, машин, стендов и агрегатов. Непрерывно повышается качественный уровень приме
няемого оборудования, изменяется |
структура парка |
в сторону роста прогрессивных групп |
оборудования — |
прецизионного, автоматизированного, |
с применением |
программного управления и специальных методов обра ботки.
Главным принципом, определяющим развитие полу проводникового производства, является механизация и автоматизация всех производственных процессов. Ме ханизация и автоматизация должны охватить не только основные и вспомогательные процессы, но и организа цию и управление производством.
Для определения наиболее выгодных, наиболее эффективных путей развития механизации и автомати зации необходимо (Л. 10]: 1) установить и обосновать
закономерности |
построения |
технологических процессов: |
||
2) |
создать |
наивыгоднейшие |
конструкции оборудования |
|
и |
оснастки; |
3) |
разработать |
основы оптимального про |
странственного размещения процессов и оборудования; 4) выбрать наилучшие системы межоперационных транспортных устройств.
Полупроводниковое производство, как отмечалось, требует большого числа различных видов технологиче ского оборудования, оснастки и инструмента. Обычно процесс изготовления каждого прибора состоит из де сятков и даже сотен отдельных операций. Так, для изготовления мезапланарных диодов требуется осущест вить более 120 операций с использованием около 80 ви дов оборудования. С увеличением количества разнотип ного оборудования усложняется задача механизации и автоматизации производства. Особая трудность за ключается в том, что, кроме массовых приборов, вы пускаемых миллионами и десятками миллионов штук в год, имеется большое количество приборов, выпускае
мых сериями, |
производство которых также должно |
|
быть механизировано. |
|
|
Проблема механизации и автоматизации технологи |
||
ческих процессов полупроводникового |
производства |
|
упрощается в |
случае уменьшения числа |
типоразмеров |
и общего количества необходимого оборудования. Для достижения этой цели необходимо соблюдать опреде ленные принципы при конструировании приборов, выбо ре метода производства, проектировании технологиче ских процессов, при выборе оборудования и оснастки, а также при разработке или выборе средств межопе рационного транспорта.
При конструировании новых полупроводниковых приборов следует стремиться к тому, чтобы снизить до минимума число типоразмеров, конструкций приборов и их элементов. Необходима максимальная стандартиза ция и унификация деталей, узлов и размеров приборов. Конструкции деталей должны быть технологичными, т. е. формы деталей должны позволять изготовлять их на механизированном и автоматизированном оборудо вании. Так, например, создание диодов и триодов с кон сольными (балочными) выводами способствовало раз работке высокопроизводительных линий для их произ водства и организации массового выпуска этих прибо ров. Производство таких диодов и триодов в сочетании с планарной технологией их изготовления позволяет вы-
Рис. 21-1. Диод с балочными вы
пускать приборы без корпуса, имеющие жесткую кон
струкцию |
и |
переход, защищенный |
двуокисью |
кремния |
и экранизированный слоем металла. |
|
|
||
Диод |
с |
консольными выводами |
(рис. 21-1) |
состоит |
из небольшого кристалла кремния, в который проведе на диффузия, прикрепленных к нему двух относительно массивных золотых выводов. Выводы создаются мето дом гальванопластики.
Исходным материалом служит эпитаксиальная пла стина кремния л-типа, из которой можно изготовить более 1 000 диодов. Сначала пластины окисляются, за тем с помощью диффузии через отверстия в окисном слое создаются слои материала р- и п-типов. После за вершения процессов диффузии в слое окисла образуют ся отверстия в местах размещения омических контак тов. В качестве материала для омических контактов используют тонкий слой благородного металла (плати ны, палладия, серебра) или молибдена. Далее на пла стину наносится тонкий слой металла, который имеет хорошее сцепление с ее поверхностью (например, хро ма или татана); при этом часть двуокиси кремния пре вращается в кремний. Последующим нанесением на пластину толстого слоя благородного металла завер шается подготовка поверхности, необходимой для про ведения гальванопластики.
Отграничение областей для образования золотых выводов производится методом фотолитографии. На области, не защищенные фоторезистом, наносятся два слоя золота, каждый толщиной 10— 13 мкм, которые и служат выводами диода. После этого с верхней пло скости удаляются фоторезист и не защищенный золо том металл. Разделение пластины на отдельные диоды производится при наложении маски на ее обратную сторону вытравливанием кремния между маскирован ными областями.
При автоматизированном изготовлении диодов используется групповая обработка; при этом возможно почти любое расположение выводов, любая форма кри сталла и перехода. Незначительная длина консольных выводов исключает их деформацию в процессе автома тической обработки.
Разработанные методы позволяют производить бы струю переналадку описанной линии на другой тип при бора путем замены фотолитографических масок.
Методы производства выбираются с учетом сле дующих основных принципов (Л. 10]:
1)организация массового производства по принци пу строгой поточности, являющейся основой высокоэф фективной комплексной механизации и автоматизации производственных процессов;
2)построение в мелкосерийном и серийном произ водствах групповых потоков на основе классификации деталей, типизации технологических процессов, унифи кации и стандартизации применяемой оснастки и инструмента;
3)укрупнение объемов выпуска изделий, облегчаю щее внедрение поточных методов работы благодаря со кращению числа типоразмеров изгоговляемых деталей, их унификации и стандартизации, а также специализа ции полупроводниковых заводов.
При проектировании технологических процессов про изводства полупроводниковых приборов определяющим является метод получения перехода, в зависимости от которого обычно строится весь процесс. Однако во всех случаях целесообразно придерживаться следующих общих принципов, обеспечивающих необходимые усло
вия для механизации |
и автоматизации |
производства: |
1) максимальное |
сокращение числа |
разнообразных |
операций путем научно обоснованного построения опти мальных процессов. Этот принцип в последние годы нашел широкое применение при разработке полупровод никовых приборов и их производстве. Создан ряд уни фицированных технологических процессов для выпуска многих групп разнотипных приборов;
2)построение одинаковых (типовых) технологиче ских процессов для однотипных приборов, выпуск ко торых дублируется несколькими заводами. Использова ние этого принципа при производстве массовых прибо ров позволяет почти вдвое сократить номенклатуру при меняема оборудования;
3)максимальное применение методов групповой технологии для обработки одновременно десятков и сотен изделий. Так, методами планарной технологии возможно одновременно на одной пластине обрабаты вать несколько сот диодных или транзисторных струк
тур;
4) получение полупроводниковых пластин после вы резки из' слитков с наименьшими припусками на после дующую обработку и получение баллонов и ножек с наименьшим разбросом по форме и геометрическим размерам;
5) механизация и автоматизация операций загрузперегрузки, выгрузки и транспортирования.
21-2. ОСНОВЫ КОМПЛЕКСНОЙ МЕХАНИЗАЦИИ И АВТОМАТИЗАЦИИ ПРОИЗВОДСТВА
Переход к комплексной механизации и автоматиза ции производства полупроводниковых приборов требует решения ряда новых технических и организационных проблем. Методы и технологические принципы мелко серийного изготовления приборов с широким примене нием ручного труда, как правило, не могут быть использованы при создании комплексных линий. Пере работка этих методов, однако, может привести и часто приводит к созданию принципиально новой технологии. Требования к стабильности, надежности работы и ре монтопригодности машины, находящейся в составе ме ханизированного комплекса, значительно повышаются. Особые требования предъявляются к единству конст руктивного решения элементов м.ашнн, входящих в ли нию, расположения вводов энергетики, органов управ ления, рабочих мест и т. д.
Особенно важное значение при осуществлении ком плексной механизации имеет тщательное технико-эко номическое обоснование выбранного варианта, учиты
вающее оптимальный уровень механизации, наиболее рациональную структуру линии, повышение выхода год ных изделий и обеспечение достаточной универсально сти линии и преемственности конструктивных решений.
Эти, как и некоторые другие вопросы, связанные с переходом к комплексной механизации производства, характерны не только для полупроводниковой промыш ленности (Л. 1]. Однако специфика полупроводниковой технологии обусловливает и здесь появление дополни тельных требований. Так, проведение многих операций в герметизированных объемах в условиях контролируе мой газовой среды требует создания новых принципов межоперациоииой передачи, разработки герметизиро ванной тары, шлюзов, специальных транспортеров, на копителей и загрузочно-разгрузочных устройств, пред назначенных специально для этих условий.
В связи с тем, что в процессе производства слож ных приборов количество годных изделий часто суще ственно меньше количества заготовок и полуфабрика тов, поступающих на линию (причем соотношение этих количеств — процент выхода годных изделий — не всег да стабильно), очень сложно обеспечить синхронную работу линии при рациональной загрузке оборудования. Проектирование расположенных в начале линии машин с «завышенной» производительностью, как правило, значительно усложняет их, а часто бывает и невозмож но технически. Это обстоятельство приводит к необхо димости создания систем расчета производительности линий, устройств задания и контроля ритма и т. д.
Особенно сложным является создание достаточно универсальных линий, позволяющих при незначительной переналадке выпускать большое количество типов при боров (многономенклатурных линий). Необходимость создания таких линий диктуется прежде всего быстры ми темпами развития полупроводникового производства; узкоспециализированная линия, предназначенная для выпуска только одного типа прибора, может быстро морально устареть при замене его в производстве но вым прибором. Накопленный опыт подтверждает воз можность разработки многономенклатуриых линий для выпуска различных типов приборов.
Для обеспечения успешного проведения комплекс ной механизации производства полупроводниковых при боров необходимо обеспечение ряда важных условий. Одним из главных условий является проведение широ кой технологической нормализации. Работы по созда нию поточно-механизированных и комплексных линий, технологических комплексов оборудования для произ водства различных групп массовых типов приборов должны проводиться одновременно с созданием типовой технологии нх изготовления. На базе нормализованных операций и типовых технологических процессов следует создавать типажи шнрокоуииверсалыюго оборудования, из которого можно комплектовать в дальнейшем поточ ные и комплексно-механизированные линии.
Важное значение имеет конструктивная унифика ция полупроводникового оборудования. Такая унифи кация должна основываться прежде всего на единых требованиях к компоновке оборудования, встраиваемого в линию, с целью обеспечения единства конструктивных решений. Одновременно должны создаваться типовые элементы комплексной механизации: загрузочные устрой ства, транспортеры, накопители и т. д. Одним из наи более прогрессивных направлений конструктивной уни фикации является агрегатирование, при котором маши на компонуется из отдельных функциональных узлов широкого применения.
Технологические процессы полупроводникового про изводства весьма трудоемки и в то же время требуют весьма тщательного их проведения и повторяемости условий выполнения операции. Поэтому одна из глав ных задач заключается в исключении субъективного
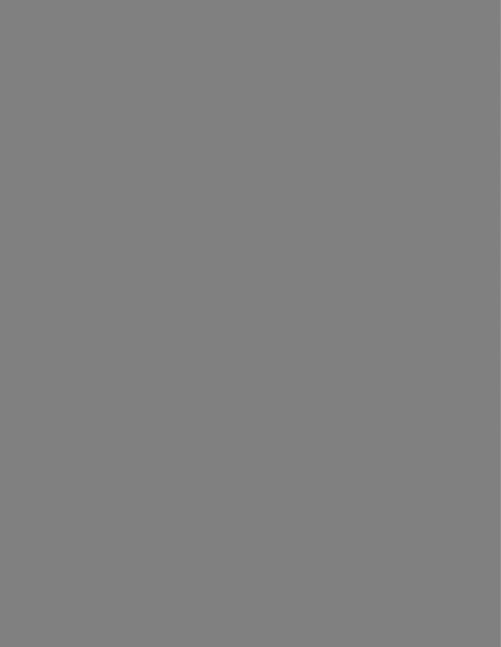
Рис. 21-3. Укрупненная схема последовательности вы полнения операций при ленточной сборке.
боров с небольшим размером по высоте. При этом мо жет применяться почти одно и то же оборудование и одни и те же технологические приемы. Этот метод сравнительно просто решает многие проблемы ориента ции деталей и манипулирования с ними, в то время как в случае других методов необходимы либо широ кое применение ручной сборки, либо механизации с использованием сложного, дорогого и быстро уста ревающего оборудования.
Широко применяется метод сборки на коротких отрезках ленты, которые транспортируются в магази нах-накопителях. Применяется также оборудование с использованием длинных отрезков ленты и магнитных барабанов в качестве накопителей. Лента и барабан из готовляются из ковара, что исключает возникновение механических напряжений при нагревании и охлажде нии в процессе термообработки из-за различия в коэф фициентах температурного расширения. Существенно, что ковар обладает магнитными свойствами. Лента удерживается на барабане только благодаря его намагничиванию. При этом отпадает необходимость в удерживающих и съемных устройствах, которые мо гут повредить приборы. Лента легко наматывается и
сматывается с |
барабана, она |
не может сойти с |
него |
и не проскальзывает по его поверхности. |
|
||
Весьма перспективным направлением механизации и |
|||
автоматизации |
производства |
полупроводниковых |
при |
боров является использование автоматических роторных линий (АРЛ). Опыт применения роторных линий в ря де отраслей промышленности показывает, что наиболее рационально их использование для изготовления мало габаритных изделий с применением таких технологиче ских операций и переходов, для осуществления которых достаточно сообщить инструменту возвратно-поступа тельное и вращательное движения, или в случае, когда Хехнологическая обработка производится перемещением
рабочей среды (нагрев, окраска, напыление и т. п.)< в направлении непрерывно движущегося потока дета лей. Наименее целесообразно применение АРЛ при. обработке резанием [Л. 16].
Применительно к полупроводниковой промышленно сти целесообразно создание АРЛ в первую очередь для ряда заготовительных процессов: производства штампо ванных деталей, производства изделий прессованием и спеканием из пластмасс и керамики, при изготовлении деталей из стекла. Возможно создание АРЛ для ряда операций окончательной сборки полупроводниковых приборов (монтаж, свертывание, заливка) и их упаковки. Автоматические роторные линии могут найти примене ние для выполнения термических и технохимических операций, таких, как нагрев, отжиг, сушка, промывка, обезжиривание, гальванические и химические покрытия и т. п., а также для некоторых видов контрольных операций по измерению геометрических размеров и электрических параметров отдельных деталей или гото вых приборов.
Автоматические роторные линии в полупроводн вом производстве позволяют осуществить [Л. 16]:
1) совмещение во времени транспортирования инструментального блока, представляющего собой авто номный комплекс (приспособление, инструмент, деталь), с обработкой детали, что гарантирует независимость транспортной и технологической скоростей;
2)достаточно простое конструктивное решение за дачи сохранения одинаковой производительности на операциях с различной длительностью технологических циклов;
3)последовательное действие узлов многоинстру ментальной части системы, благодаря чему обеспечи вается непрерывное функционирование рабочей зоны машины и оказываются достаточными энергетические ресурсы привода из расчета на один-два одновременно работающих комплекта инструмента;
4)передачу деталей на обработку в многоннструментальную часть системы единым потоком одним кон структивно несложным питающим устройством.
Внедрение комплексно-механизированных и автомат тизированных линий дает значительный технический и экономический эффект. Обеспечивается выполнение тех нологических операций в заданном ритме при их совме щении во времени, что приводит к сокращению продол жительности технологического цикла и исключению межоперациоиного пролеживания деталей. Повышается стабильность технологического процесса. Создаются
условия для более совершенной организации работ, со ответствующей массовому поточному производству и требованиям научной организации труда. Одновременно, обеспечивается также повышение культуры производ ства и улучшение условий труда, особенно на химиче ских и других вредных операциях.
Комплексная механизация позволяет значительноувеличить производственные мощности предприятий, снизить трудоемкость и себестоимость приборов, повы сить выход годных изделий. В качестве примера ука жем, что внедрение комплексно-механизированной ли нии для производства выпрямительных диодов среднеймощности позволило предприятию увеличить производ ственные мощности в 3 раза, трудоемкость изготовле ния диодов снизить более чем на 40%, а себестои мость— почти на 35%. выход годных изделий при этом вырос более чем на 10%.
Большое значение для повышения эффективности использования комплексно-механизированных и автома тизированных линий имеет учет ряда факторов, непо средственно влияющих на уровень их эксплуатации. На практике имеют место случаи, когда линии эксплуати руются с низким коэффициентом использования из-за отсутствия четкой и рациональной организации их рабо
ты. Простои по организационно-техническим причинам могут достигать 70% от общего количества простоев линии. При проектировании, а особенно при внедрении и эксплуатации линии должен быть продуман и решен комплекс вопросов, охватывающий весь процесс произ водства, начиная от заготовок и исходных материалов и кончая получением готовой продукции.
На работу линии непосредственно влияет качество исходных материалов, заготовок и детален. Опыт по казывает, что для комплексно-механизированных и автоматизированных линии всегда требуются заготовки и детали более высокой точности, а материалы более стабильного качества. При механизации сборочных про цессов нельзя рассчитывать на применение заготовок и детален, используемых при ручной сборке. Механизация сборки требует более стабильных размеров, форм и ка чества исходных деталей, что нередко приводит к не обходимости повышения культуры заготовительных производств.
Более высокие требования предъявляет комплекс ная механизация и автоматизация также к качеству вспомогательных материалов, химикатов и защитных сред, к степени их чистоты и стабильности состава.
Правильная организация эксплуатации линий долж на предусматривать бесперебойное обеспечение их инструментом и оснасткой, спутниками и технологиче ской или межоперационной тарой. Это требует в свою очередь повышения организационно-технического уровня инструментальных служб предприятия, решения вопро сов хранения и замены инструмента и оснастки, пред варительной настройки и контроля качества изделий после смены инструмента.
Как правило, внедрение комплексно-механизирован ных линий существенно повышает требования к энерге тике, к стабильности состава и степени очистки газов и воздуха, к стабильности напряжения в электрических сетях и т. д.
Особое значение имеют обеспечение четкого режима работы линий и поддержание оборудования в работо способном состоянии. Кроме графиков сменности и инструкций по текущему обслуживанию линии, должна быть разработана система быстрой замены потерявших точность или вышедших из строя узлов и частей машин в процессе работы. Для этого необходимо иметь соот ветствующий фонд запасных частей и узлов и конкрет ный план ремонтов, разработанный применительно к данной линии.
При внедрении и эксплуатации линий возникают и такие вопросы, как обеспечение линии контрольно-изме рительными приборами и аппаратурой и организация их своевременной поверки, транспортирование и подача на линию заготовок и деталей, контроль и учет продук ции II др.
В связи с повышением требований к уровню обслу живания, наладки и ремонта оборудования, к контролю технологии и качества изделий особое внимание должно быть уделено подготовке и обучению операторов, на ладчиков, технологов и контролеров, а также рабочих ремонтных и инструментальных служб. Как показывает опыт эксплуатации линий, имеющихся в промышленно сти, недостаточный уровень подготовки кадров может привести к снижению эффекта от внедрения линий из-за частых простоев оборудования и низкого выхода годных изделий.
Основные направления мероприятий по повышению эффективности использования специального технологи ческого оборудования и комплексно-механизированных линий: максимальное повышение интенсивности исполь зования рабочих элементов машин и линий путем повы шения производительности; повышение уровня унифи кации различных узлов и деталей машин и линий; сни
жение ремонтных расходов; внедрение технически обо снованных норм обслуживания; снижение удельных ка питальных вложений на выпуск единицы изделия.
21-3. НАУЧНЫЕ ОСНОВЫ МЕТОДОВ
СОЗДАНИЯ СРЕДСТВ МЕХАНИЗАЦИИ И АВТОМАТИЗАЦИИ ПРОИЗВОДСТВА
Успешные результаты в проведении работ по меха низации и автоматизации производственных процессов в полупроводниковой промышленности могут быть до стигнуты прн правильной организации проектирования и изготовления оборудования, выборе соответствующих методов оценки параметров перспективного оборудова ния, при правильном определении реального эффекта, получаемого от внедрения оборудования и комплексно механизированных линий.
В связи со значительным усложнением технологиче ских процессов производства полупроводниковых при боров и соответственно средств их механизации и авто матизации, как правило, разработке машин и комплекс но-механизированных линий должно предшествовать проектирование процессов производства приборов. Этой цели служит теория проектирования процессов произ водства многокомпонентных машин и устройств, разра ботанная П. II. Мссяцевым. В соответствии с этой тео рией прн проектировании процессов производства необ ходимо проанализировать факторы, влияющие на дан ный процесс. Далее должны быть установлены опти мальные соотношения для проектируемого процесса производства и проведена оценка его эффективности.
Одно из условий правильного проектирования за
ключается в получении процессов с одинаковой вос |
|||
производимостью— однотипных процессов, |
причем |
ва |
|
жен не только выбор |
последовательности |
операций, |
но |
и порядок проведения |
каждой операции |
и подготовки |
к ней. В связи с большим числом операций, используе мых в современных процессах производства, и сложной структурой этих процессов выявление однотипности является весьма трудоемкой задачей. Особая тщатель ность необходима при обосновании выбора оптимально го варианта процесса.
Прн проектировании процессов производства долж на быть учтена возможность построения параллельнопоследовательного сборочного процесса, обеспечивающе го минимум его «длины». Следует помнить при этом, что для выпуска одного и того же количества продук ции при одной и той же скорости процесса могут быть использованы разные варианты технологического про цесса.
Существенное влияние па проектирование оказы вает полнота проработки всех этапов процесса произ водства. При выборе исходных данных для проектиро вания процесса производства следует учитывать дан ные, связанные с освоенностью прибора, наличием про грессивного оборудования, а также с ограничением мес та и времени развертывания производства.
Определение оптимального варианта процесса про изводства сводится к нахождению условного экстрему ма функции от многих переменных известными способа ми; при этом исходные данные при определенных допу щениях позволяют произвести упрощение процесса на хождения оптимального варианта.
Весьма важным условием создания оборудования и линий для механизации и автоматизации производ ства является отработанность методов и средств опера ционного контроля всех факторов, влияющих на каче ство изделий. Разработку оборудования для механиза ции и автоматизации любой операции или процесса возможно проводить только в том случае, если опре делены все факторы, влияющие на качество изделий,
Рис. 21-4. Схема структуры размерно-параметрического ряда и типажа оборудования и их взаимосвязей.
установлены конкретные значения параметров процес сов н диапазоны их допустимых изменении, разработа ны методы, средства п периодичность контроля состоя
ния технологии. |
полупроводникового машинострое |
|||
|
Эффективность |
|||
ния |
может |
быть |
повышена путем |
совершенствова |
ния |
машин |
или порядка разработки |
нового оборудо |
вания. Как известно, проектирование оборудования при учете потребностей только одного предприятия или вы пуска только одного типа прибора имеет ряд сущест венных недостатков. Изолированное проектирование отдельных машин очень часто приводит к тому, что машины, созданные для одной и той же цели, имеют различное конструктивное оформление и не обладают необходимой взаимной унификацией. Это в свою оче редь сопряжено с крупными потерями при их производ стве и эксплуатации. Поэтому при разработке полупро водникового оборудования широко применяется извест ный и в других отраслях машиностроения и приборо строения метод создания размерно-параметрических ря дов и типажей, в основе которого лежит конструктив ная и технологическая унификация имеющегося и разрабатываемого оборудования и определение такой его минимальной номенклатуры, которая позволила бы при наименьших затратах обеспечить максимальное удовлетворение потребности предприятий в этом обо
рудовании.
Большую роль при построении рядов и типажей имеет обоснованный выбор основных параметров ма шин. В качестве основных выбираются параметры, наи более полно выражающие технологические и эксплуа тационные показатели машин. Номенклатура основных параметров должна быть минимальной, а параметры — относительно стабильными, т. е. они не должны изме няться при создании конструктивных модификаций и технических усовершенствованиях машин. Далее, основ ные параметры не должны зависеть от таких часто ме няющихся факторов, как технология изготовления ма шины, применяемые материалы и т. п.
Один из основных параметров выбирается в каче стве главного, он предопределяет технологическое и функциональное назначение типа оборудования и в то же время не ограничивает дальнейшего его конструк тивного совершенствования. Так, например, главным параметром прессов для герметизации полупроводнико
вых приборов методом холодной сварки является номи нальное усилие давления пресса; в качестве главного параметра установок химического травления прини мается полезная емкость ванн травления; для электро печей сопротивления — объем рабочей зоны или мощность и т. д.
Численные значения главного параметра образуют ряд, который называется параметрическим. Параметри ческий ряд, дополненный геометрическими размерами и другими значениями основных пармаетров, называется размерно-параметрическим рядом оборудования.
Под типом понимают группу машин одного назна чения, сходных по методу выполнения технологических операций, принципу действия, конструктивной схеме и т. д. Типоразмер — это представитель размерно-пара метрического ряда машин с определенными численными значениями его основных параметров. Конкретное кон структивное исполнение изделия определенного типо размера называют моделью.
Модель называется базовой, если при конструктив ной разработке модели учитываются различные условия ее использования, и соответственно она снабжается различными механизмами и устройствами, наличие ко торых определяется конкретными условиями эксплуата ции. Базовые модели являются основой размерно-пара метрических рядов.
Разновидности модели с некоторыми изменениями в конструктивном оформлении, не затрагивающими основных параметров, технологического процесса и принципиального конструктивного решения, называются модификациями. Модификации разрабатываются с ис пользованием тех же узлов и механизмов, что и базо вая, обычно наиболее универсальная модель, и предна значены для лучшего и более экономичного обеспечения требований, предъявляемых к машинам данного типо размера конкретными условиями производства. Моди фикации, как правило, менее универсальны, чем базо вая модель, но нередко более автоматизированы приме нительно к конкретным условиям эксплуатации. Иногда модификации, созданные па основе одного типоразмера, называют «семейством» машин.
Типаж машин включает совокупность существую щих или подлежащих разработке машин, представляю щую минимально возможную экономически обоснован ную их номенклатуру, необходимую для полного удо влетворения потребностей отрасли. Все основные моди фикации машин находят отражение в типаже. Таким образом, типаж содержит значительно большее количе ство различных машин, чем размерно-параметрический ряд. Схема структуры размерно-параметрического ряда и типажа и их взаимосвязей представлена на рис. 21-4.
Очевидно, что для планирования производства по лупроводникового оборудования недостаточно знать ряды параметров и размерно-параметрические ряды ма шин; необходимы типажи по всем основным операциям производства полупроводниковых приборов или по основным группам оборудования.
Сущность методики состоит в определении диапазо на значений основных параметров и разделении его на
некоторое число (ряд) |
значений — на параметрический |
ряд. При определении |
густоты (частоты) ряда рекомен |
дуется обычно руководствоваться стандартом на ряды предпочтительных чисел [Л. 8,31]. Однако статистические данные показывают, что конкретные значения парамет ров оборудования во многих случаях расходятся со зна чениями, рекомендуемыми стандартом. Методы опреде ления параметров (Л. 40] весьма трудоемки, опираются, как правило, только на экономическую оценку и не дают ответа на вопрос о динамике изменения этих па раметров и об определении значений параметров пер спективного оборудования.
При определении значений параметров перспектив ного технологического оборудования и при краткосроч ном прогнозировании его развития (на 4—5 лет) можно применять следующую методику. Определение парамет ров производится с учетом специфики технологического оборудования полупроводникового производства. Так, например, оборудование связано в большие производ
ственные комплексы единством |
обрабатываемого |
изде |
л и я — полупроводникового прибора. Это требует |
прове |
|
дения тщательной межрядовой |
и межтипажной |
увязки |
значении основных параметров оборудования.
Далее, для полупроводникового производства ха рактерно наличие технологического брака на многих операциях, определяемого выходом годных изделий. Величина брака может колебаться в значительных пре делах. Поэтому для получения требуемого выпуска год ных приборов иногда приходится на начальных опера циях запускать комплекты заготовок в количестве, зна чительно превышающем количество годных приборов (соотношение этих количеств называется «коэффициен том запуска»). Очевидно, что указанное обстоятельство также усложняет определение численных значений па раметров, в особенности тех из них, которые прямо или косвенно связаны с производительностью.
Наконец, важной задачей является повышение мо рального срока службы оборудования в условиях час той сменяемости объектов производства и необходимо сти улучшения использования средств, отпускаемых на новые разработки и изготовление оборудования.
При определении номенклатуры параметров обору дования, по которым можно прогнозировать его разви тие, всегда следует учитывать, что технологическое оборудование служит для производства продукции. По этому в качестве главного параметра должна прини маться производительность технологического оборудо вания (или пропускная способность контрольно-измери тельного и испытательного оборудования) наряду с некоторыми основными параметрами, определяющими технологические возможности оборудования. Однако для большинства видов оборудования производитель ность не задается непосредственно кинематикой стан ков, а зависит от формы и размеров конкретных изде лий и технологических режимов их обработки. Напри мер, для станков разрезки монокристаллических слит ков на пластины производительность зависит от вида полупроводникового материала (германий или крем ний), диаметра слитка и толщины отрезаемых пластин;
для электротермических установок |
(печей вплавления |
и дпффузии) производительность |
определяется геоме |
трическими размерами рабочей зоны и продолжитель ностью технологического цикла и т. д. Поэтому для каждого конкретного вида оборудования производи тельность выражается через минимум основных техни ческих характеристик (параметров).
При оценке параметров перспективного технологи ческого оборудования недостаточно учитывать только их абсолютные значения. В ряде случаев при некотором улучшении одного параметра вновь разрабатываемого оборудования, например увеличении длины рабочей зо ны печи, новая модель может значительно уступать
существующему оборудованию по другим |
параметрам |
|||
|
Рис. 21-5. Схема про |
|||
|
гнозирования |
мето |
||
|
дом |
экстраполяции |
||
|
кривой. |
|
|
|
|
Л—/» — базовый |
период: |
||
I |
/г—/э—перспективный пе- |
|||
риод; |
Р\, |
Р2— известные |
||
-*• значения параметра; Ру— |
||||
*3 |
перспективное |
значение |
||
|
параметра. |
|
|
Рис. 21-6. Типичная логистическая кривая.
или превосходить его по стоимости, занимаемой пло щади и т. д. Кроме того, на трудоемкость и стоимость разработки и изготовления оборудования в значитель ной мере влияют конкретные условия места, времени, уровня организации работ, что затрудняет сравнение и анализ оборудования, разработанного или изготовлен ного различными предприятиями.
Поэтому в качестве критериев технической эффек тивности технологического оборудования наиболее при менимы удельные характеристики, т. е. соотношения основных параметров и размеров машин. Эти соотно шения обладают определенной статистической устойчи востью независимо от конструктивных особенностей ма шин, спроектированных в разное время различными организациями в различных условиях. Обработав зна чения отношений основных параметров к весу, зани маемой площади, стоимости и трудоемкости методами математической статистики [Л. 3], можно получить удельные характеристики для оценки уровня экономи ческой эффективности.
Прогнозирование осуществляется классическим ме тодом экстраполяции полученных кривых (рис. 21-5). Поскольку решается задача в основном краткосрочного прогноза, то точность прогнозирования может быть вполне удовлетворительной. Кривые, отражающие дина
мику |
процессов, |
в данном случае будут сходными |
с так |
называемой |
логической кривой — кривой роста |
(рис. 21-6). Такие процессы характеризуются некоторым
критическим временем 1Крт, после |
которого вступают |
|
в действие ограничивающие факторы и темп роста пара |
||
метра Р постепенно замедляется |
по |
мере приближения |
к предельному значению Рарсд |
[Л. |
7]. |
Поскольку при краткосрочном прогнозировании бе рутся только отдельные короткие участки кривых, то на этих участках изменение их может быть описано линейным законом. Расчеты при выборе оптимального варианта в случае одновременного изменения несколь ких переменных могут производиться методами линей ного программирования с точно рассчитываемой сте пенью погрешности [Л. 42].
При прогнозировании технического прогресса в области технологического оборудования постоянно следует иметь в виду тенденции развития изделий, для выпуска которых предназначено оборудование. В ряде случаев, когда выпускаемое изделие снимается с про изводства и заменяется новым, некоторые виды техно логического оборудования не могут применяться. В свя зи с этим прекращается их совершенствование и изго товление, хотя значения их параметров, возможно, не
достигли не только Я п рсд, но и Я „ р п т |
(рис. 2 1 - 6 ) . |
||
Изложенная методика оценки значений основных |
|||
параметров |
позволяет |
осуществлять |
прогнозирование |
технического |
прогресса |
технологического оборудования. |
С помощью данной методики возможно прогнозирова ние потребности в оборудовании при известном прогно-