
книги / Плазменные технологии в сварочном производстве. Ч
.2.pdfили полностью скалывается. В результате ресурс работы термо химического катода определяется числом включений (не превы шает 60-120), а также рядом других факторов. К ним относятся: чистота меди обоймы, плотность контакта вставки и обоймы, особенности конструктивного исполнения катода, ток дуги, чис тота воздуха и его расход, температура и расход воды или возду ха, охлаждающих катод. Кроме того, материал катодных вставок (цирконий, гафний) является дефицитным и дорогим.
В настоящее время ведутся работы по исследованию
ипрактическому использованию ВПР с применением плазмо тронов с «холодным» электродом. Плазмотрон имеет полый внутренний медный электрод и сопловой электрод (см. рис. 33). Дуга в рабочем режиме горит между внутренним электродом
иразрезаемым металлом. Плазмообразующий воздух подается
вразрядную камеру через тангенциальные отверстия в завихрителе. Вихревая подача плазмообразующего воздуха обусловли вает создание в камере газового циклона, который интенсивно перемещает опорное пятно дуги по внутренней поверхности электрода, не допуская локального нагрева и расплавления. Этой же цели служит соленоид, который охватывает медный полый электрод. При работе плазмотрона на обратной полярно сти скорость эрозии электрода снижается. Использование плаз мотронов с полым медным электродом позволяет повысить мощность режущей дуги увеличить количество включений дуги без разрушения электрода.
Кнедостаткам такого способа плазменной резки металлов можно отнести необходимость использования источников пита
ния сварочного тока с напряжением холостого хода |
« 500 В. |
Рабочее напряжение при резке составляет порядка С/д « 300 В. Плазмотроны с полым электродом, из-за наличия соленоида, имеют повышенные габариты и массу. Это усложняет оборудо вание, снижает условия электробезопасности работ, при этом исключается возможность использования этого способа для руч ной резки металлов.
В настоящее время ограниченное применение находит плазменная резка металлов плазмотронами с вольфрамовым ка тодом и комбинированной подачей газов (рис. 35). Известен
71
способ плазменно-дуговой резки металлов в активных окисли тельных средах (например в воздухе) плазмотронами с исполь зованием вольфрамового электрода, защищенного в зоне актив ного пятна дуги инертным газом. Для этого цилиндрический, заостренный вольфрамовый электрод располагают в специаль ном внутреннем сопле плазмотрона, в которое подается инерт ный газ, например, аргон или азот.
аб
Рис. 35. Схема плазмотронов для плазменной рез ки с комбинированной подачей газов: а - с внут ренним формирующим соплом; б - с внутренним защитным соплом; / - катодный узел, 2 - вольф рамовый катод, 3 - изолятор, 4 - формирующее внутреннее сопло, 5 - наконечник, 6 - подача плазмообразующего защитного газа, 7 - подача окислительного газа в наконечник, 8 - защитное внутреннеесопло, 9- подача плазмообразующего
окислительного газа
Окислительный газ, например воздух, подается во внешнее стабилизирующее сопло (наконечник). Резка производится на прямой полярности. Такой способ резки металлов обеспечивает высокую стойкость катода в работе при большом количестве включений сжатой дуги. Напряжение холостого хода источника питания не превышает. [/хх« 250...300 В, а рабочее напряжение на дуге Ua « 110... 140 В. Однако у этого способа резки есть не
72
достаток: для надежной работы плазмотрона (для качественной защиты вольфрамового катода) требуются большие расходы ар гона QAT > 20...40 л/мин, что резко повышает стоимость погон ного метра реза.
Резка плазмой, стабилизированной водой и воздушно водяной плазмой значительно усложняет оборудование и повы шает его стоимость, поэтому объем применения этих способов не велик.
Резка узкоструйной плазмой по качеству и скорости при ближается к лазерной резке. Однако она применяется только для металла малых толщин и имеет высокую стоимость.
4.5. Требования к источникам питания для плазменной резки
Существенное влияние на процессы, происходящие при ВПР, оказывают электрические параметры системы источник тока - дуга. Схема замещения цепи источник - дуга представ лена на рис. 36, а, а статические вольт-амперные характеристи ки режущей дуги (ВАХд) и источника (ВАХ„) - на рис. 36, б. Семейство ВАХД (кривые 1-3) можно условно разделить на три характерных участка: падающий (ток дуги до 50 А), независи мый (ток 50-400 А) и возрастающий (ток более 500 А).
дуга (а) и семейство статических ВАХД(кривые 1-3) и ВАХИ (кривые 4 - 9) (б)
Наклон ВАХД зависит от степени сжатия столба дуги, а на пряжение на дуге определяется размерами камеры плазмотрона и параметра режима (состав и расход плазмообразующей среды, скорость резки, длина открытого и режущего участков столба
73
дуги). В зависимости от схемных решений неуправляемого вы прямителя естественная ВАХИ(см. рис. 36, б) может быть крутопа дающей (кривая 4) и пологопадающей (кривые 5, 6), а при введе нии обратных связей в управляемый выпрямитель ступенчатой (кривые 7-9). Ключевой проблемой системы источник - дуга является ее устойчивость. При рассмотрении устойчивости дуги возмущающим параметром будет изменение напряжения дуги, возникающее при изменении определяющих его величин: длины дуги, расхода газа и др. Реакцией на это возмущение является изменение тока, определяемое переходом на другую ВАХД. Ско рость переходного процесса определяется скоростью изменения напряжения и инерционностью системы источник - дуга. Кри тические условия статической и динамической устойчивости сис темы особенно проявляются на падающем участке ВАХЛ, напри мер, при запуске дежурной дуги, ток которой ограничен допус тимой нагрузкой на сопло, а возможность повышения напряже ния холостого хода ограничена условиями электробезопасности. Кроме того, в случае чрезмерной пологости ВАХ„ (кривая 6 на рис. 36, б) в неуправляемых выпрямителях при ограничении напряжения холостого хода не более 300 В технологическая ус тойчивость дуги становится критической и существенно ухуд шаются режущие свойства дуги. При этом при ручной резке вследствие колебания длины дуги наблюдаются значительные изменения тока дуги, приводящие к резкому ухудшению качества поверхности кромок реза (образованию рисок). При ручной и машинной резке металла большой толщины с погружением ду ги в глубь металла происходит уменьшение тока дуги и ее проре зающей способности.
В управляемых тиристорных выпрямителях введением от рицательной обратной связи по току достигается ВАХ„, изобра женная кривой 7 (см. рис. 36, б), т.е. обеспечивается стабиль ность тока дуги при колебаниях ее длины, расхода рабочего газа и напряжения питающей сети. Еще более высокие техно логические свойства режущей дуги наблюдаются при введении дополнительной обратной связи положительной по напряже нию дуги. В этом случае ВАХ„ (кривая 8) отличается возраста
74
нием тока дуги при увеличении длины режущего участка, что обеспечивает высокое качество кромок реза и повышение про резающей способности дуги.
Идеальной ВАХИс учетом требований всех факторов устой чивости системы и высокого КПД источника является кривая 9 (рис. 36, б). Такая характеристика обеспечивается комбинацией двух выпрямителей - с рабочим участком ВАХ„, описываемым
кривой 8, |
и маломощного вольтодобавочного с участком ВАХ„, |
соответствующим кривой 4. |
|
Представленные в сжатом виде закономерности послужили |
|
основой |
для разработки современных источников питания |
для плазменной резки. |
Крутопадающие внешние статические характеристики могут быть обеспечены следующими типами источников питания: вы прямителями, управляемыми дросселями насыщения, тиристор ными выпрямителями с обратной связью по току, источниками питания на базе индуктивно-емкостных преобразователей и тран зисторными источниками питания. В отдельных случаях мо!ут использоваться сварочные генераторы.
Выпрямители с дросселями насыщения широко применя ются для плазменной обработки. Они обладают хорошими ре гулировочными характеристиками, просты в обслуживании и надежны в работе. Их недостатками являются низкий cos (р, значительные габаритные размеры и масса. Не вполне удовле творительны и динамические характеристики дросселей насы щения, поэтому появляются броски тока при возбуждении дуги в источнике питания для плазменной резки. Используемое в этих источниках питания начальное ограничение тока подмагничивания дросселя насыщения все же не позволяет полно стью избавиться от бросков тока.
Надежным серийным оборудованием для воздушно плазменной резки являются установки УПР-201, АПР-401, АПР-402 и АПР-403.
Источники питания с дросселями насыщения постепенно вытесняются более экономичными, компактными и легкими ти ристорными выпрямителями. Тиристорные выпрямители, напри мер, установок «Киев-5» и «Киев-6», в которых для получения
75
крутопадающих внешних статических характеристик исполь зуется обратная связь по току нагрузки, в настоящее время наиболее соответствуют требованиям, предъявляемым к источ никам питания для плазменной обработки. В источниках пита ния этого типа достаточно просто реализуются режимы плавно го увеличения и уменьшения тока, импульсные режимы, что значительно расширяет и улучшает технологические возможно сти выпрямителей. К числу их недостатков можно отнести большую величину пульсаций при глубоком регулировании. Уменьшение пульсаций за счет увеличения индуктивности сглаживающего дросселя приводит к ухудшению условий зажи гания дуги.
В момент возбуждения дуги, когда сигнал обратной связи отсутствует, тиристорный выпрямитель фактически является нерегулируемым выпрямителем с жесткими характеристиками. Увеличение угла открывания тиристоров при возбуждении дуги приводит к снижению напряжения холостого хода и уменьше нию вероятности возбуждения дуги.
Источники питания на базе индуктивно-емкостных преобра зователей можно отнести к сравнительно новым типам. Несмотря на то, что индуктивно-емкостные преобразователи имеют верти кальные характеристики, соответствующие требованиям плаз менной технологии, они не получили широкого распространения из-за сложности регулирования тока. Практически ток в индук тивно-емкостном преобразователе может регулироваться только изменением питающего напряжения. Область применения индук тивно-емкостных преобразователей ограничивается плазменной резкой, которая может производиться при 2-3 фиксированных значениях токов.
Несмотря на указанный недостаток, а также на необходи мость применения в индуктивно-емкостных преобразователях силовых конденсаторов и дросселей, эти источники питания весьма перспективны.
Транзисторные источники питания имеют высокие техни ческие характеристики. Поскольку транзистор является полно стью управляемым полупроводниковым прибором и к тому же имеет высокие частотные параметры, транзисторные источники питания позволяют получить любую форму статической харак
76
теристики, идеально сглаженный ток и прекрасные динамиче ские свойства. Однако они сравнительно дороги, имеют низкий КПД и ограниченную мощность из-за небольшой мощности рассеяния транзисторов.
4.6. Технология плазменной резки
Для того чтобы осуществить плазменную разделительную резку металла, необходимо расплавить определенный объем ма териала вдоль предполагаемой линии реза и удалить его из по лости реза скоростным потоком плазмы.
Для выплавления зоны металла вдоль линии реза нужно подвести определенное количество теплоты. Это количество поступает в металл из столба сжатой дуги и носит название эф фективной тепловой мощности дуги q„. Требуемая величина q„ (Вт), зависит от многих параметров и определяется по формуле
Яи = VMCTnn -Г0) +<7)4,19,
где vp - скорость резки, см/с; F - площадь поперечного сечения зоны выплавляемого металла, см2; р - плотность разрезаемого металла, г/см3; с - теплоемкость металла, Дж/(г*°С); Гпп - темпе ратура плавления металла, °С; Г0 - температура металла до на чала реза, °С; q - скрытая теплота плавления металла, °С.
Здесь произведение vPFp определяет массу выплавляемого металла за единицу времени и имеет размерность г/с.
Эффективная тепловая мощность qHдля заданной толщины металла имеет определенное числовое значение, ниже которого процесс резки невозможен.
Расплавленный металл, образующийся на лобовой поверх ности реза, удаляется скоростным потоком плазмы сжатой дуги. Скорость потока плазмы возрастает с увеличением расхода плазмообразующего газа и тока и быстро уменьшается с увели чением диаметра сопла. Она может достигать примерно 800 м/с при токе 250 А.
Скорость течения расплава зависит от скорости потока плаз мы на границе раздела фаз, т. е. на границе жидкий металл - по ток плазмы. Так, например, при резке металла толщиной 5-20 мм со скоростью 0,75-6 м/мин и ширине реза 3-6 мм скорость тече ния расплавленного металла 20-40 м/с.
77
Плазменная резка позволяет с высокой скоростью произво дить раскрой любых металлов толщиной до 50-60 мм (рис. 37). С дальнейшим ростом толщины разрезаемых металлов скорость резко снижается.
К м/мин 5
4
3
2
I
0
Рис. 37. Скорость ВПР малоуглеродистых и низколегированных сталей: а - плазмотронами с воздушным охлаждением при использовании установок «Киев-5» (rfc = 2,2 мм; / - /д = 100... 120 А; 2 - /д ® 120... 140 А; 3 - 1а= 140... 160 А); б - плазмотронами с водяным охлаждением, качественная резка при 1а = 200 A, dc - = 2 мм (4); /д = 300 A, dQ=3 мм (5); /д = 400 A, dQ= 4 мм (б); кисло
родная резка (7)
При плазменной резке поверхность реза претерпевает структурные изменения, которые наблюдаются в основном в литом участке зоны термического влияния у кромок реза. Для уменьшения толщины литого участка необходимо повы шать напряжение на дуге и скорость потока плазмы.
Это может быть достигнуто при увеличении расхода плаз мообразующего газа, использовании сопел малого диаметра с повышенной длиной канала, применении рабочего газа с по вышенным содержанием кислорода. Толщина литого участка ниже у верхней кромки, чем в нижней части реза.
78
При плазменной резке кроме насыщения поверхности реза газами и изменения твердости металла наблюдаются и дефекты формы кромок.
Плазменная резка алюминия и его сплавов выполняется с использованием в качестве плазмообразующего газа сжатого воздуха или кислорода. Скорость резки алюминиевых сплавов в среде кислорода уменьшается на 10-12 %.
При осуществлении плазменной резки титана и его сплавов необходимо обеспечивать специальные технологические меро приятия с целью получения поверхности реза, не требующей последующей механической обработки, которая предполагает высокую трудоемкость. Трудности механической обработки воз никают вследствие интенсивного окисления и газонасыщения поверхностных слоев металла. В результате такие элементы, как азот, кислород и водород, проникая в металл, образуют твердые растворы внедрения, обладающие повышенной твердостью, низ кой пластичностью и ударной вязкостью. Эти особенности титана и его сплавов обусловливают ведение процесса резки с возможно большой скоростью для обеспечения его минимальной длитель ности. Если по каким-либо причинам это невозможно обеспечить, следует место реза защищать дополнительно инертным газом или осуществлять резку в среде инертного газа.
Титан толщиной 5 мм можно резать при следующих пара метрах: диаметр канала сопла 1,4 мм, ток 100 А, расход воздуха 13,5 л/мин, напряжение 95 В и скорость резки 2,6 м/мин. При этих параметрах режима средняя ширина реза 1,6 мм.
Скорость резки различных металлов и качество кромок мо гут быть повышены при использовании водоинъекционной плазменной резки.
При водоинъекционной резке плазмообразующий газ тан генциально подается в пространство между электродом и со плом (рис. 38). Вода в дугу вводится радиально с помощью дополнительного сопла. Она охлаждает сопло и способствует идеальному сжатию плазмы. Температура плазмы может дос тигать 50 000 К. Несмотря на такую высокую температуру, испаряется не более 10 % воды. Оставшиеся 90 % выходят из сопла в виде струи конической формы. Эта струя при над водной эксплуатации охлаждает поверхность детали и препятствует образованию оксидов на поверхности реза.
79
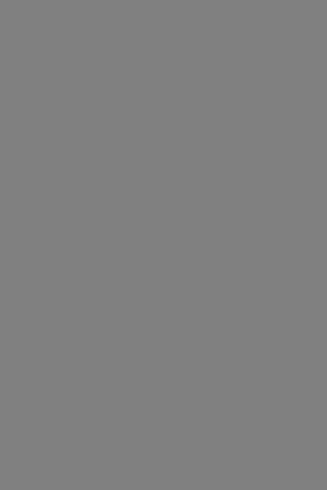