
книги из ГПНТБ / Молочников Н.В. Создание нового прокатного и другого металлургического оборудования доклад по творческим работам и изобретениям, представленным вместо диссертации на соискание ученой степени доктора технических наук
.pdf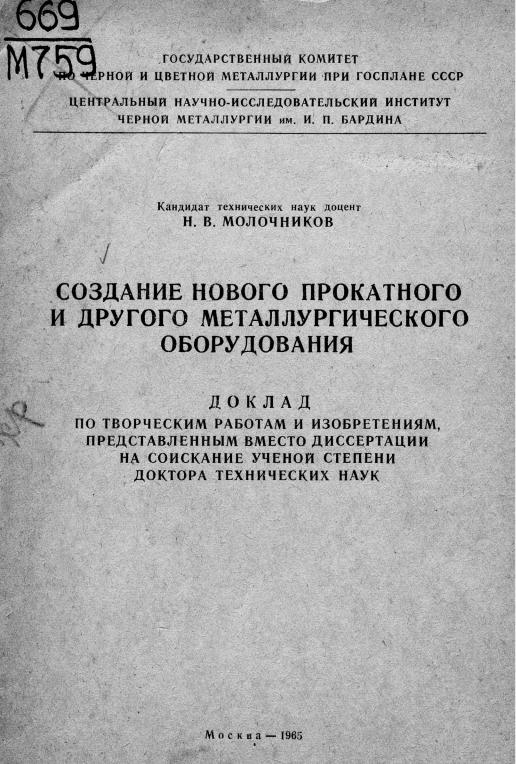
ГОСУДАРСТВЕННЫЙ КОМИТЕТ ПО ЧЕРНОЙ И ЦВЕТНОЙ МЕТАЛЛУРГИИ ПРИ ГОСПЛАНЕ СССР
ЦЕНТРАЛЬНЫЙ НАУЧНО-ИССЛЕДОВАТЕЛЬСКИЙ ИНСТИТУТ ЧЕРНОЙ МЕТАЛЛУРГИИ им\. И, П. БАРДИНА
Кандидат технических наук доцент
н. в. молочников
СОЗДАНИЕ НОВОГО ПРОКАТНОГО И ДРУГОГО МЕТАЛЛУРГИЧЕСКОГО ОБОРУДОВАНИЯ
Д О К Л А Д
ПО ТВОРЧЕСКИМ РАБОТАМ И ИЗОБРЕТЕНИЯМ, ПРЕДСТАВЛЕННЫМ ВМЕСТО ДИССЕРТАЦИИ НА СОИСКАНИЕ УЧЕНОЙ СТЕПЕНИ
ДОКТОРА ТЕХНИЧЕСКИХ НАУК
М о с к в а — 1965
|
И ч |
|
г***"? |
rC'J, ПУБЛИЧНАЯ |
|
ИАУЧ HО-7E XКHЧE СКXЯ |
|
___БИБЛИОТЕКА 'УССР |
|
Ш rt |
с щ _ |
|
ТЖз |
ВВЕДЕНИЕ
Представленные к защите творческие работы и изобретения от носятся к созданию нового прокатного и другого оборудования для заводов черной металлургии и отражают основные результаты мно голетней (с 1924 по 1964 г.) деятельности автора в области метал лургического машиностроения.
Работы охватывают круг вопросов, связанных с созданием но вого механического оборудования для прокатного, доменного и ста леплавильного производств, оборудования для проведения научных исследований в черной металлургии, а также оборудования для но вых металлургических процессов.
На содержании работ отразились общие условия становления и развития народного хозяйства СССР, в частности, черной метал лургии и тяжелого машиностроения, а также уровень мировой техники в этих отраслях в различные периоды.
Представляемые к защите работы широко внедрены или внед ряются на металлургических предприятиях Советского Союза и нашли применение за рубежом.
В настоящем докладе дан обзор основных работ, выполненных под руководством и при непосредственном участии автора на Уралмашзаводе, в бывшем Центральном конструкторском бюро металлургического машиностроения, в Гипромезе и во ВНИИМЕТМАШ"е.
Доклад имеет приложение в двух томах.
В первом томе содержатся фотографии некоторых машин и агрегатов из числа внедренных и внедряемых в промышленность.
Во втором томе содержатся фотографии авторских свидетельств на внедренные и внедряемые оригинальные машины и механизмы, а также фотокопии печатных работ по созданию отдельных машин-
I.ОБОРУДОВАНИЕ ДЛЯ ПРОКАТНОГО
ИТРУБОПРОКАТНОГО ПРОИЗВОДСТВ
I. Агрегат для прокатки толстостенных труб повышенной
точности
В1947 г. во исполнение приказа Министра черной металлургии
вГипромезе был разработан технический проект оборудования агрегата для прокатки толстостенных труб повышенной точности на Первоуральском Новотрубном заводе. Эти трубы, требующие ме ханической обработки, предназначались в основном для производ ства подшипников качения, а также для автотракторных деталей, паропроводов, коллекторов высокого давления и изделий специаль ного назначения.
Отличительная технологическая особенность этого агрегата, обеспечивающая повышенную точность прокатки, состоит в том, что раскатка гильзы производится на длинной оправке в трехвал ковом стане косой прокатки.
Валки этого стана имеют особую калибровку: два конуса сое динены в середине крутым гребнем, с помощью которого и выпол няется основное обжатие при прокатке. Высота гребня находится в пределах от 6 до 16 мм и тем больше, чем больше толщина стен ки трубы. Передний конус захватывает трубу, а задний раскаты вает ее после обжатия гребнем.
Сначала вновь создаваемый агрегат предназначался для про катки труб диаметром от 40 до 160 мм с толщиной стенки до 50 мм из подшипниковой стали ШХ15, а также углеродистой стали с пре делом прочности до 100 кг!мм2, среднелегированных и высоколе гированных сталей, включая нержавеющие стали типа 18—8 и дру гие.
Вместе с тем при конструировании стана и всех механизмов агрегата предусматривалась возможность прокатки труб из тех же марок сталей диаметром до 200 мм, целесообразность прокатки которых на этом же агрегате начала выявляться уже в начале его проектирования. В связи с этим в сортамент были дополнительно включены трубы диаметром от 160 до 200 мм.
До пуска нового агрегата с трехвалковым раскатным станом толстостенные трубы изготовлялись в СССР на агрегатах Штифеля, шведским способом и на агрегатах Эргардта-Петерса.
4
"Основным недостатком труб, получаемых на упомянутых агре гатах, было то, что они имели большую разностенность и оваль ность. В связи с этим приходилось прокатывать трубы с большими припусками на механическую обработку, что приводило к весьма большому расходу легированного металла, доходившему до 1,8 4- 2,1 т на одну тонну готовых обточенных труб.
Радикальное решение вопроса прокатки труб повышенной точ ности давал процесс, в котором гильза после прошивного стана раскатывается на длинной оправке в трехвалковом стане косой прокатки с валками специальной калибровки.
Как известно, первый экспериментальный трехвалковый рас катный стан был установлен в 1933—34 гг. на заводе фирмы Тим кен в Вустере (США). На этом же заводе в 1935 г. был введен в
эксплуатацию производственный агрегат, на котором прокатыва лись трубы диаметром от 1 3/4 до 3" при толщине стенки от 2,5 до
25 мм.
Позднее на одной линии с малым станом был установлен второй стан для прокатки труб диаметром от 3 до 6".
Других агрегатов с трехвалковым раскатным станом в США в то время не было. Это объяснялось тем, что фирма Тимкен, владев шая патентом, приобретенным ею у изобретателя Ассела, не раз решала строить такие станы в США.
Перед второй мировой войной машиностроительная фирма Меер приобрела лицензию на использование способа Ассела для трубо прокатных агрегатов во всем мире. На одном из них производи лись трубы диаметром 34 4- 36 мм при толщине стенки 2-^-5 мм,, а
на другом — трубы диаметром 46-^58 |
мм при |
толщине стенки |
||
2 —5 мм. И только третий |
агрегат предназначался для |
производ |
||
ства подшипниковых труб |
диаметром |
150 4- 200 |
мм при |
толщине |
стенки до 50 мм. Однако этот агрегат к тому времени не был укомп лектован прошивным станом и печью для нагрева трубных загото вок.
По отчетным данным инженеров Василенко С. Е. и П. Г. Емель яненко о поездке в США, а также по данным фирмы Меер предель ные отклонения от номинального наружного диаметра труб, прока тываемых на агрегате с трехвалковым прокатным станом, не пре вышают ± 0,5%, а по толщине стенки ±'5% , в то время как при
.других, упомянутых выше способах прокатки, отклонения от номи нального наружного диаметра составляют около 1%, а по толщине стенки ±!12,5%. Таким образом, имелись основания ожидать, что точность прокатки труб на агрегатах с трехвалковым станом бу дет превосходить в 2 4- 2,5 раза точность прокатки труб, получае мых на агрегатах Штифеля и других упомянутых станах. В дальнейЩем это подтвердилось эксплуатацией агрегата, разработан ного для Первоуральского Новотрубного завода.
Резкое уменьшение разностенности и овальности труб при про- <катке их на агрегате с трехвалковым станом позволило значитель
5
но снизить припуск на механическую обработку подшипниковых труб. Коэффициент расхода дорогостоящего легированного метал ла снизился с 1,8 -4- 2,1 до 1,4 тна тонну готовых обточенных труб, что дает большую экономию металла.
Вторым преимуществом применения трехвалкового раскатного стана является простота перехода на прокатку труб других разме ров. Изменение внутреннего диаметра труб осуществляется подбо ром оправки соответствующего диаметра, введение которой в ра боту не требует перенастройки стана. Для получения необходимой толщины стенки и наружного диаметра трубы при данном диамет ре оправки необходимо только установить рабочие валки на соот ветствующем расстоянии от оси прокатки, что осуществляется спе циальными механизмами с минимальной затратой времени. Пере валка валков производится лишь при значительном изменении тол щины стенки и наружного диаметра трубы.
В зависимости от диаметра прокатываемых труб диаметр вал ков раскатного стана принимается равным: для труб с наружным диаметром 40-1- ПО мм в преде’лах 240 v 350 мм, для труб диамет ром 80 v 200 мм — 470 4- 490 мм. Большой диапазон размеров труб, прокатываемых при одном и том же диаметре валков, позво ляет приурочить перевалку валков к остановке стана для текущего ремонта.
К моменту начала проектирования агрегата Гипромез распола гал разрозненными фотографиями и общими видами некоторых узлов американских станов, а также предложением фирмы Этна Стандарт на поставку стана СССР.
Тщательное изучение этих материалов привело к выводу, что существовавшие в то время за границей агрегаты, имевшие в сво ем составе трехвалковые раскатные станы, по своей конструкции и компоновке оборудования не соответствовали уровню техники послевоенного времени и не смогли быть признаны удовлетвори тельными. В Гипромезе были разработаны новая оригинальная конструкция и компоновка оборудования агрегата. Рабочее проек тирование и изготовление агрегата осуществлялись Электростальтяжмашзаводом.
Этот агрегат явился первым отечественным трубопрокатным агрегатом для прокатки толстостенных труб повышенной точности. Следует отметить, что по своему техническому уровню агрегат и теперь в основном соответствует современным требованиям.
К числу оригинальных решений по агрегату прежде всего сле дует отнести разработанную систему задачи гильз и оправок в трехвалковый раскатный стан, которая позволила уменьшить про должительность холостого хода стана с 25 до 3,5 секунды и, следо вательно, значительно повысить его производительность. Сущность этой системы состоит в том, что гильза и оправка подаются в же лоб раскатного стана одновременно и притом тогда, когда еще рас катка предыдущей гильзы не закончена. В то время как заканчи-
6
мается процесс раскатки предыдущей гильзы, другая оправка втал кивается в последующую гильзу и вместе с нею поступает в валки раскатного стана вслед за предыдущей оправкой.
Чтобы осуществить идею последовательной задачи гильз в рас катный стан с предельно малым промежутком между гильзами, привод стана отнесен от валков назад по направлению оси про катки на расстояние, равное сумме длин оправки и гильзы, и еще на 4 м, необходимых для размещения механизмов самого стана и упора для задержки гильзы во время вталкивания в нее оправки.
В новом расположении механизмов агрегата оправкоизвлекатель приближен к раскатному стану, а ванна для охлаждения оправок вынесена за привод стана, что сокращает расстояние меж ду раскатным и прошивным станами и создает прямой поток опра вок. По пути следования оправок к раскатному стану установлена машина для смазки оправок.
К числу оригинальных конструктивных решений отдельных ма шин и механизмов следует, например, отнести: пружинное с под вижной опорой уравновешивание рабочих валков раскатного и трехвалкового калибровочного станов; индивидуальные электри ческие приводы для механизмов установки рабочих валков; регу лирование угла прокатки в широком диапазоне (3 7 9°); извлекатель оправок с электромеханическим захватом и реечным приво дом, позволяющим извлекать оправки с большими скоростями (при рабочем ходе 86 м1мин, при обратном ходе 170 м/мин).
В целях унификации и сокращения сроков изготовления агрега та были использованы отдельные машины, разработанные в ЦКБММ для типовых трубопрокатных агрегатов 250 и 140. В част ности, были применены рабочие клети прошивного и пятиклетевого калибровочного станов.
Новые конструктивные и компоновочные решения агрегата по зволили полностью автоматизировать работу его оборудования. Производительность агрегата в 1,5 4-1,7 раза превышает достиг нутую зарубежными агрегатами аналогичного назначения.
2. Правильные машины для правки труб и круглых прутков
До создания отечественной ротационной правильной машины с гиперболоидными валками на наших заводах применялись пра вильные машины системы Абрамсон с двумя длинными приводны ми валками и тремя или пятью холостыми роликами. Основной не достаток этих машин — необходимость применения проводок для удержания выправляемого металла от смещения с осевой линии правки. Это смещение обусловливается односторонним приложе нием окружных сил, действующих со стороны приводных валков. Другим недостатком машин системы Абрамсона является распо ложение всех правильных валков в горизонтальной плоскости и
вытекающая отсюда необходимость в применении рольгангов с пе ременным уровнем.
В основу правильных машин, разработанных в 1946—47 гг. в. ЦКБММ и Гипромезе под руководством и при участии автора, по ложены схемы, в которых каждые две пары верхних и нижних вал ков имеют привод, что исключает необходимость в применении, проводок ввиду взаимного уравновешивания окружных сил, дейст вующих со стороны двух пар приводных валков. Принятые схемы обеспечивают более точную правку металла.
Уровень положения рольгангов постоянный, нижние валки рас положены в одной вертикальной плоскости с верхними и не имеют регулировки по высоте. В зависимости от диаметра трубы или за готовки регулируются только верхние валки и один средний ниж ний для создания необходимой величины прогиба заготовки.
До сих пор эти машины считаются наиболее совершенными. Они построены в большом количестве для правки труб и сплошных круглых заготовок различных размеров. В настоящее время маши ны работают на всех трубопрокатных и других отечественных за водах и за рубежом.
Машины правят трубы диаметром 400 мм со скоростью 0,3 — 1,3 м!сек. Скорость правки машинами меньших размеров достигает
2.5м/сек.
3.Типовые трубопрокатные агрегаты 140, 250 и 400
В1946—47 гг. Центральным конструкторским бюро металлур гического машиностроения под общим руководством А. И. Целикова впервые в СССР были разработаны трубопрокатные агрегаты 140, 250 и 400 для прокатки труб повышенной точности. Схема рас положения оборудования и технологические процессы во всех агре гатах одинаковы.
Агрегат 400 предназначен для прокатки труб диаметром от 130! до 426 мм, длиной до 15,5 ж и толщиной стенки от 5 до 40 мм. В со став его входят две кольцевые нагревательные печи с вращающим ся подом, два прошивных стана, методическая нагревательная печь перед автоматическим станом, автоматический стан, семиклетевой стан для горячей калибровки труб, два правильных стана, трех клетевой стан для холодной калибровки труб, холодильники и инспекционные столы.
Применение двух прошивных станов и подогрев гильз перед автоматическим станом обеспечивает возможность прокатки тон костенных труб из легированных и нержавеющих сталей.
Трубопрокатный агрегат 140 предназначен для прокатки труб диаметром от 38 до 140 мм, длиной до 11,5 ж и толщиной стенки от 3.5 до 20 мм. После редукционного стана можно получать трубы длиной 15,5 ж.
Агрегат имеет одну кольцевую печь, прошивной стан, автома тический стан, два раскатных стана, пятиклетевой стан для горя- 8
чей калибровки труб, подогревательную печь перед редукционным
станом, двадцатиклетевой стан, |
холодильники, правильные станы |
и инспекционный стол. |
отличается от агрегата 140 по со |
Трубопрокатный агрегат 250 |
ставу оборудования лишь отсутствием редукционного стана и его подогревательной печи. Станы и отдельные механизмы обоих агре гатов аналогичны, а автоматический и раскатный станы унифици рованы. Трубопрокатные агрегаты 140, 250 и 400 имеют следующие особенности в сравнении с аналогичными импортными агрегатами 5 1/2" (Этна Стандарт) и 13 3/8" (Шлеман), установленными в
СССР в послевоенные годы:
а) все станины прокатных станов выполнены значительно более жесткими;
б) для опор валков всех станов (кроме автоматического стана 400) применены подшипники качения;
в) впервые применены центрователи на задних столах прошив ных и прокатных станов для центрирования стержня и гильзы — трубы по оси прокатки;
г) на вспомогательных механизмах применены вместо пневма тических электрические приводы, что, помимо повышения надежно сти работы агрегатов, значительно облегчает возможность их авто матизации;
д) проведена максимальная унификация отдельных узлов, ме ханизмов и даже целых станов (нацример, унификация автомати ческих и раскатных станов агрегатов 140 и 250).
Перечисленные основные особенности конструкции агрегатов 140, 250 и 400 обусловливают следующие их преимущества перед упомянутыми выше импортными станами:
а) более высокая скорость прокатки на прошивных станах (на 75%) и автоматических станах (на 50%);
б) возможность прокатывать трубы повышенной точности с уменьшенными против ГОСТа плюсовыми допусками с соответ ствующей экономией металла;
в) возможность перехода на полную автоматизацию агрегатов; г) уменьшение количества запасных частей и расхода валков. Агрегаты, изготовленные Уралмашзаводом, смонтированы и введены в эксплуатацию в период 1947—54 гг. на Руставском ме таллургическом заводе (агрегаты 140 и 400) и на Азербайджан
ском трубопрокатном заводе (агрегаты 140 и 250).
4. Блюминг 1000
После окончания Великой Отечественной войны в июле 1^45 г. правительство СССР, учитывая перспективы дальнейшего развития черной металлургии, приняло решение о строительстве блюмингов для новых металлургических заводов.
Выполнение технического проекта типовых блюмингов было возложено на Центральное конструкторское бюро металлургичес-
9