
книги из ГПНТБ / Кузьминов С.А. Сварочные деформации судовых корпусных конструкций
.pdf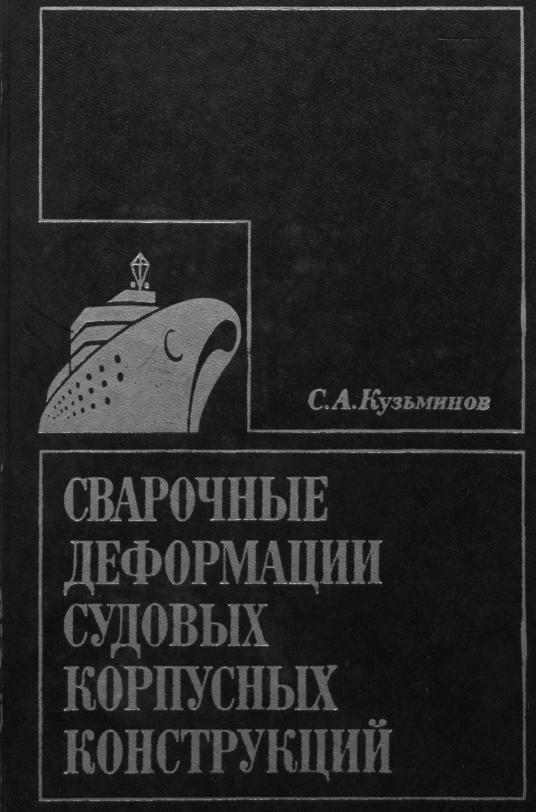
С.А.Кузьминов
СВАРОЧНЫЕ
ДЕФОРМАЦИИ
ездовых
КОРПУСНЫХ
КОНСТРУКЦИЙ
КОНТРОЛЬНЫЙ ЭКЗЕМПЛЯР
ИЗДАТЕЛЬСТВО «СУДОСТРОЕНИЕ»
ЛЕНИНГРАД
1974
УДК 629. 12.011:621.791.019 К89
АН |
|
Гос. публичная |
f |
|
||
научко-твхничес:--чр 4 |
|
|||||
|
библиотека •' |
' |
|
•' 1 |
|
|
|
ЭКЗЕМГ?.1 |
• |
> ' |
|
|
|
|
|
|
|
"А ' ! |
|
|
|
|
Развитие сварного судостроения (разработка новых типов судов, |
||||
|
внедрение новых материалов и новых |
методов сварки) потребовало |
||||
|
от судостроителей решения ряда сложных вопросов по уменьшению |
|||||
|
сварочных деформаций и повышению точности изготовления корпус |
|||||
|
ных конструкций. Поэтому возникла необходимость вооружить про |
|||||
|
ектантов и технологов методикой расчетного определения ожидае |
|||||
|
мых |
сварочных деформаций и комплексом мероприятий по борьбе |
||||
|
с ними. Разработке указанных вопросов посвящается настоящая книга, |
|||||
|
состоящая из 8 глав и |
приложения |
справочного характера. |
|||
|
|
В конце каждой главы даны примеры расчета соответствующих |
||||
|
сварочных деформаций. |
|
|
|||
|
|
В приложении приведены справочные материалы,. необходимые |
||||
|
для расчета ожидаемых сварочных деформаций, а также даны таблицы |
|||||
|
сравнения расчетных и замеренных значений сварочных деформаций. |
|||||
|
|
Илл. 165. Табл. |
22. |
Литерат. 123 |
назв. |
|
|
Рецензенты: д. т. н. Д. И. |
Навроцкий, к. т. |
н. К- М. Гатовский |
Научный редактор к. т. н. И. М. Жданов
31804-041 К 048(01)—74 25—74
© Издательство «Судостроение», 1974 г.
УСЛОВНЫЕ ОБОЗНАЧЕНИЯ
L — длина, см; |
|
|
|
|
|
|
|
|
|
|
||
В — ширина, |
см; |
|
|
|
|
|
|
|
|
|
|
|
б — толщина, |
см; |
|
|
|
|
|
|
|
|
|
|
|
F — площадь поперечного сечения, см2, |
поперечного |
сече |
||||||||||
J — центральный |
момент |
инерции |
площади |
|||||||||
ния, |
см4; |
|
|
|
|
|
|
|
|
|
|
|
ст — напряжение, кгс/см2 (Н/м2); |
|
|
|
|
||||||||
ат — предел текучести, |
кгс/см2 |
(Н/м2); |
|
|
|
|
||||||
Е — модуль нормальной упругости, кгс/см2 (Н/м2); |
|
|
||||||||||
(.1 — коэффициент Пуассона; |
|
|
|
|
|
|
|
|||||
е — относительная деформация; |
|
|
|
|
|
|||||||
R — радиус, см; |
|
|
|
|
|
|
|
|
|
|
||
С — кривизна, 1/см; |
|
|
|
|
|
|
|
|
|
|||
К — катет шва таврового или углового соединения, см; |
|
|
||||||||||
/ св — сила сварочного тока, |
А; |
|
|
|
|
|
|
|||||
t/д — напряжение сварочной дуги, В; |
|
|
|
|
||||||||
Уев — скорость сварки |
(скорость |
перемещения дуги вдоль сваривае |
||||||||||
мого соединения), см/с; |
г/А- ч; |
|
|
|
|
|||||||
ан — коэффициент наплавки, |
|
|
сварочной |
|||||||||
rj — эффективный к. п. д. процесса нагрева конструкции |
||||||||||||
дугой; |
энергия |
нагрева |
свариваемых |
элементов |
при |
на |
||||||
qn — погонная |
||||||||||||
плавке одного валика (прохода), |
кал/см2 |
(Дж/м2); |
|
см3; |
||||||||
V — объем |
продольного укорочения |
сварного |
соединения, |
|||||||||
W — объем |
поперечного укорочения |
сварного |
соединения, |
см3; |
||||||||
v — погонный объем |
продольного укорочения |
(объем продольного |
||||||||||
укорочения сварного соединения, Приходящийся на единицу |
||||||||||||
длины шва), см2; |
|
|
|
|
|
(объем поперечного |
||||||
w — погонный |
объем |
поперечного укорочения |
||||||||||
укорочения сварного соединения, приходящийся на единицу |
||||||||||||
длины шва), см2; |
|
|
|
укорочения конструкций по осям, |
||||||||
ДL, ДВ — продольные и |
поперечные |
|||||||||||
проходящим через центр тяжести сечений конструкции, |
см; |
|||||||||||
<Pj, Ц>ь — угол |
поворота |
одного |
конца конструкции |
относительно |
дру |
|||||||
гого, |
рад; |
|
|
смещение |
|
точек |
сечения |
конструкции |
(«+» |
|||
Sj — горизонтальное |
|
|||||||||||
к середине конструкции, |
«—» от середины конструкции), см; |
|||||||||||
fi — вертикальное |
смещение |
точек |
сечения |
конструкции |
(«+» |
|||||||
вверх, «—» вниз), |
см; |
|
|
|
|
|
|
|
Р— угловая деформация (местный угол изгиба полотнища, вызы ваемый приваркой набора или сваркой стыковых соединений
листов), рад;
/— стрелка прогиба, см; Тпл — температура плавления материала, °С;
Т0 — температура, при которой материал теряет упругие свой ства, °С;
ТПр — максимально допустимая температура нагрева при правке, °С; Тб. пр — рекомендуемая температура нагрева при безударной правке, °С ;
1» |
3 |
|
h — коэффициент |
теплопроводности, кал/см-с-град; (Дж/см |
сХ |
|||
|
|
Хград); |
|
|
|
|
|
с — удельная теплоемкость, кал/г-град; (кДж/кг-град); |
|
||||
|
у — плотность, г/см3; |
|
|
|
||
|
а 0 — коэффициент |
теплоотдачи, кал/см3-с-град; (Дж/м2-с-град); |
||||
|
а — коэффициент |
линейного расширения, 1/град; |
|
|||
|
0 — коэффициент нагрева (коэффициент пропорциональности между |
|||||
|
|
погонной энергией и площадью поперечного сечения наплав |
||||
|
|
ленного металла), кал/см3; (Дж/м3); |
|
|
||
|
су — коэффициент тепловой деформации, см3/кал; |
(м3/Дж); |
|
|||
|
а= — |
— коэффициент |
температуропроводности, см2/с; |
|
||
|
су |
|
|
|
|
|
|
суо |
— коэффициент |
температуроотдачи для пластин (листов), 1/с; |
|||
__ |
1450 |
— коэффициент, |
учитывающий |
влияние свойств материала |
на |
|
Р ~ |
Тшсу |
прогрев свариваемых элементов; |
|
|
||
|
|
|
|
|||
X = 2а„ — относительная |
теплоотдача с |
поверхности |
свариваемых |
эле- |
||
|
Ао |
ментов, 1/см2; |
|
|
|
|
|
|
|
|
|
||
s = 100----------коэффициент, |
учитывающий |
влияние свойств материала |
на |
|||
|
суг8 |
|
|
|
|
|
угловые деформации.
ВВЕДЕНИЕ
Электрическая дуговая сварка в настоящее время является основным технологическим процессом соединения судовых корпус ных конструкций.
Переход от клепаного судостроения к сварному позволил [50], [58]:
упростить конструкцию судна (ликвидация соединений вна хлестку, различного рода накладок, книц, заклепок и т. п.);
снизить вес корпуса судна в среднем на 20% при сохранении требуемой прочности;
удешевить постройку корпуса благодаря упрощению техноло гии, большей автоматизации процессов изготовления и ликвидации таких операций, как фланжировка, наметка, сверление и развертка отверстий, клепка, чеканка и т. д.;
изготовлять корпус судна секционным и блочным методами при сборке секций и блоков в закрытых отепленных цехах;
уменьшить стапельный период постройки благодаря переносу большей части работ в цехи.
Однако технологический процесс сварки имеет и свои недостатки, основным из которых является деформация конструкций, т. е. изменение их размеров и формы в процессе сварки.
Опыт постройки сварных судов показывает, что деформации узлов и секций, возникающие в процессе сварки, значительно ослож няют сборку и сварку корпусов.
При стыковании деформированных секций затрачивается много рабочего времени на подгоночные и прирубочные работы [50]. Иногда весь экономический эффект от применения сварки взамен клепки поглощается затратами на правку сварных конструкций. При этом следует отметить, что особенно затруднена правка объемных (дни щевых) секций. Иногда деформации корпусных конструкций (днище вых секций, секций надстроек и др.) достигают такой величины, что выправить их становится невозможно, и готовые конструкции бракуются.
Кроме того, сварочные деформации часто приводят к снижению прочности корпусных конструкций из-за потери устойчивости флор, выпучивания листов настила и переборок.
5
Степень снижения прочности и увеличения трудоемкости изго товления конструкций зависит от величины возникающих сварочных деформаций, которая, в свою очередь, зависит от конструктивного оформления изделия и технологии его изготовления.
Для того чтобы проектируемая конструкция и технология ее изготовления были оптимальными, с точки зрения получения мини мальных сварочных деформаций, необходимо знать законы возник новения и развития сварочных деформаций и уметь определять величины ожидаемых деформаций еще в стадии проектирования конструкции и разработки технологии ее изготовления.
Проектирование сварных конструкций и разработка технологии их изготовления должны вестись одновременно, исходя из обеспе чения требуемой технологической прочности, необходимой точности (минимальных сварочных деформаций) и работоспособности кон струкции.
Выполняя в процессе проектирования конструкции расчет ожи даемых сварочных деформаций для различных конструктивных и технологических вариантов, проектировщик может выбрать опти мальный вариант конструкции и технологии ее изготовления с точки зрения получения минимальных деформаций. В частных случаях может оказаться, что конструктивными и технологическими прие мами невозможно (или невыгодно) обеспечить получение конструкций в требуемых допусках, тогда ожидаемые сварочные деформации, определенные расчетом, необходимо компенсировать соответствую щим изменением размеров деталей и обратным выгибом конструкции при сборке.
На производстве иногда применяется способ опытного опреде ления и компенсации деформаций секций. На основании замеров деформаций изготовленных ранее секций изменяют форму постели и размеры заготовок для последующих секций. Однако этот способ можно применять только для одинаковых секций, изготовляемых по одинаковой технологии. Для различных секций или для одинаковых секций, но изготовляемых по разным технологическим процессам, деформация получается различной, и указанный способ неприменим.
Все сказанное выше потребовало создания теоретических основ и разработки расчетного метода определения ожидаемых сварочных деформаций судовых конструкций, а также разработки мероприятий по их уменьшению и компенсации.
Начало разработки расчетных способов определения ожидаемых сварочных деформаций (перемещений) относится к 30-м годам XX в. Первые научные разработки и обобщения в области расчетного опре деления сварочных деформаций опубликованы в работах советских ученых Г. А. Николаева [56], Н. О. Окерблома [59], [60], В. П. Во логдина [8], [9], Е. О. Патона [82] и др. Деформации конструк ции определяли методами сопротивления материалов как жесткой балки на основе гипотезы плоских сечений в зависимости от фиктив ной силы (нагрузки). Величину фиктивной силы подбирали таким образом, чтобы вызванные ею деформации (перемещения) были равны действительным деформациям от сварки.
6
В дальнейшем для определения остаточных сварочных деформа ций нежестких конструкций и конструкций, для которых не приме нима гипотеза плоских сечений, были предложены решения термо механических задач с использованием аппарата теории упругости. Эти решения изложены в работах В. И. Васильева (6], Г. Б. Талыпова [94], В. С. Игнатьевой [21 ], И. П. Трочуна [100] и др. Однако решения, основанные на методе фиктивных сил, имели существен ный недостаток, заключающийся в приближенном эмпирическом задании величины фиктивной силы. Величину фиктивной силы (на грузки) устанавливали либо на основании частных опытов, либо выбирали на основе довольно грубых допущений: одновременность заварки шва по всей длине, пренебрежение теплоотдачей и др., что снижало ценность этих решений, так как результаты расчетов часто не совпадали с данными фактических замеров.
Еще в 30-х годах было установлено [56], что фиктивная сила при определении продольных деформаций конструкций должна равняться сумме напряжений, действующих в так называемой ак тивной зоне, где в процессе концентрированного нагрева и после дующего остывания образовались остаточные пластические дефор мации. Но определение этой суммы вызывает большие затруднения, так как она, в свою очередь, зависит от величины остаточных пла стических деформаций зоны сварного соединения и величины иско мых деформаций (перемещений) конструкций.
С целью упрощения расчетов позже было предложено [31], 158], [65] определять деформации (перемещения) конструкций непосредственно в зависимости от величины остаточных пластиче ских деформаций зоны сварных соединений.
Разработанная к этому времени Н. Н. Рыкалиным теория распро странения тепла при сварке [89], [90] позволила найти зависимости остаточных пластических деформаций укорочения сварных соеди нений от режимов сварки.
Графоаналитические методы [23], [31], [58], [61], [64] рас смотрения температурных деформаций в процессе нагрева и осты вания позволили уточнить определение продольных деформаций. Метод плавной интерполяции [31] позволил уточнить определение поперечных пластических деформаций.
Указанные методы позволили решить ряд задач по определению остаточных деформаций конкретных конструкций с использова нием соответствующих методов строительной механики [7], [10], [14], [20], [26], [38], [40], [43], [49], [69], [70], [100].
В 1968 г. в МВТУ им. Баумана под руководством Г. А. Никола ева и В. А. Винокурова был разработан метод одновременного определения продольных и поперечных сварочных деформаций и напряжений на цифровых вычислительных машинах с использо ванием теории распространения тепла при сварке, а также законов и уравнений теории упругости и теории пластического течения [7]. Этот метод позволяет определять как временные, так и оста точные напряжения и деформации в случае наплавки валика на лист.
7
В развитие этого метода в Институте электросварки имени Е. О. Патона под руководством В. И. Махненко разработаны числен ные методы определения напряжений в процессе сварки различных соединений. Эти методы позволяют с помощью ЭВМ определять эпюры сварочных напряжений в любой момент времени, в любых сечениях листа конечной толщины. При этом учитываются влияния формы источника, предварительного подогрева, структурных пре вращений и внешней нагрузки.
В настоящей работе приведены теоретические обоснования и установлены зависимости продольных и поперечных пластических деформаций укорочения сварных соединений от режима и условий сварки, а также выведены формулы для определения общих и мест ных деформаций (перемещений) типовых судовых корпусных кон струкций с использованием теории распространения тепла при сварке и строительной механики. При расчетах деформаций наибо лее сложных конструкций рекомендуется применять электронновычислительные машины.
Разработанные методы расчета ожидаемых сварочных деформа ций выполнены применительно к металлическим конструкциям, изготовляемым из судостроительных корпусных сталей, алюминие вых и титановых сплавов. Расчетные формулы могут быть исполь зованы также для определения сварочных деформаций других метал лических конструкций.
Кроме этого, в работе приводятся рекомендации и мероприятия по уменьшению и компенсации сварочных деформаций, а также указания по правке основных судовых корпусных конструкций.
Глава I
ОСНОВЫ РАСЧЕТА И КЛАССИФИКАЦИЯ СВАРОЧНЫХ ДЕФОРМАЦИЙ КОРПУСНЫХ КОНСТРУКЦИЙ
§ 1
Образование и развитие пластических деформаций в сварном соединении
Тепловые процессы в металле при сварке плавлением протекают под действием тепла дуги (или другого источника) и в условиях быстро изменяющейся температуры. Пределы изменения темпера туры весьма широки: от минус 30—40° С при сварке на морозе до температуры испарения металла (+3000° С). Тепло от более нагре тых точек тела вследствие теплопроводности переходит к менее нагретым, и температура их выравнивается. Одновременно вслед ствие теплоотдачи с поверхности свариваемых элементов темпера тура течек непрерывно уменьшается до температуры окружающей среды [89].
|
Изменение температуры точек тела за некоторый промежуток |
|||||||||||
времени |
t—10 вызывает |
в этих точках температурные деформации |
||||||||||
во |
всех |
направлениях, |
равные |
|
|
|
|
|
|
|||
|
|
|
|
ет (х, У, г) = атТ (х, |
у, |
z), |
|
(1) |
||||
где |
|
ет (х, у, |
z) — относительная |
температурная |
деформация |
|||||||
|
|
|
|
точки тела с координатами (х, у, z) в каком- |
||||||||
|
|
Т (х, у, |
z) |
либо направлении; |
|
z, |
t0) — изменение тем |
|||||
|
|
= Т (х, у, z, |
t) — Т (х, у, |
|||||||||
|
|
|
|
пературы |
точки тела |
с |
координатами х, у, г |
|||||
|
Т (х, г/, г, |
t) |
за время t—i0, °С; |
тела в момент |
времени |
|||||||
|
— температура точки |
|||||||||||
|
Т (х, у, z, |
|
t, |
°С; |
|
|
|
|
|
в начальный |
||
|
t0) — температура этой же точки тела |
|||||||||||
|
|
|
|
момент времени t0, °С; |
|
расширения |
||||||
|
|
|
сст — средний |
коэффициент |
линейного |
|||||||
|
|
|
|
в интервале температур Т (t):— Т (t0), 1/град. |
||||||||
вая |
Температурные деформации будут протекать свободно (не вызы |
|||||||||||
внутренних напряжений) |
при |
условии, |
если тело |
свободно, |
а температурные деформации отдельных его точек, определяемые выражением (1), постоянны или имеют постоянный градиент (т. е. изменяются в каком-либо направлении по линейному закону).
Иначе говоря, если при нагреве температура точек тела изме няется на одинаковую величину (равномерный нагрев) или изме-
9