
книги из ГПНТБ / Шнееров, Я. А. Полуспокойная сталь
.pdf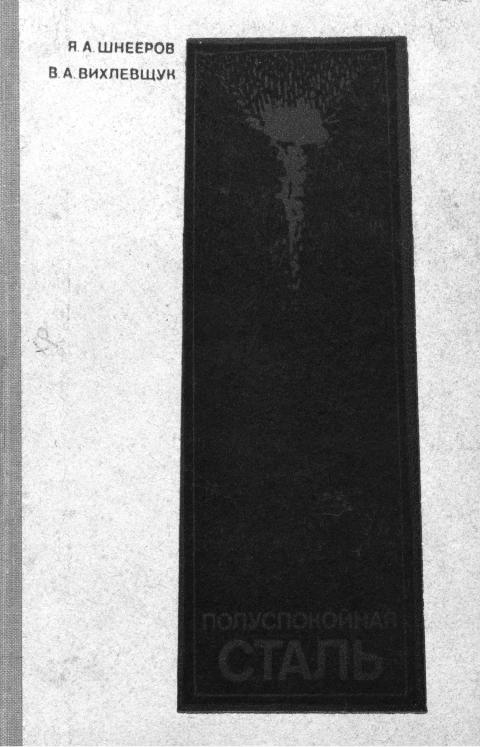
Я. А. ШНЕЕРОВ, В. А. ВИХЛЕВЩУК
Полуспокойная С Т А Л Ь
Москва «МЕТАЛЛУРГИЯ» 1973
УДК |
669.141.241.3 |
|
|
! |
научи |
• 1 |
? |
<>w-.;. |
•-• • |
I |
|
|
|
• - |
i |
УДК 669.141.241.3 |
|
|
Полуспокойная |
сталь. |
Ш н е е р о в Я. А., В и х л е щ у к В. А. |
М., «Металлургия», 1973, 368 с. |
||
Изложены |
материалы |
исследований по разработке и внедрению |
рациональной технологии выплавки, раскисления и разливки полу спокойной стали. Приведены результаты изучения условий формиро вания и качества слитка. Представлены результаты исследований фи зико-механических и служебных свойств углеродистой полуспокой ной стали в сравнении со спокойной, а также работ по изысканию новых марок полуспокойной стали с повышенным содержанием мар ганца и микролегированием. Даны рекомендации по использованию проката из углеродистых и низколегированных полуспокойпых сталей вместо спокойных в конструкциях, изделиях и машинах. Показана технико-экономическая эффективность производства и применения полуспокойных сталей вместо спокойных.
Книга рассчитана на инженерно-технических работников пред приятий, научно-исследовательских и проектных организаций черной металлургии, машиностроения и строительства. Ил. 133. Табл. 132. Список лит.: 349 назв.
Издательство «Металлургия», 1973.
Ш 3102—180 43—74 040(01)—73
ВВЕДЕНИЕ
В результате технического прогресса, обусловившего непрерыв ное повышение требований к свойствам стали массового применения, в частности, к ее хладостойкости, на металлургических заводах СССР
к концу пятидесятых годов значительно увеличилась доля спокойной стали в общей выплавке при одновременном снижении доли кипящей стали.
Наряду с этим увеличение производительности сталеплавильных агрегатов и обжимных станов сопровождалось увеличением массы слитков, что вызывало повышение неоднородности их химического состава и ухудшение макроструктуры, особенно проявляющихся в слитке кипящей стали. Это неизбежно приводило к увеличению го ловной обрези при прокатке слитков, необходимости использования в ряде случаев металла не по назначению, повышению неоднородно сти свойств готового проката, что в свою очередь также способство вало снижению доли кипящих сталей.
Растущие потребности в прокате черных металлов вызывают не обходимость максимальной экономии металла на пути от слитка к готовому прокату и его удешевления, что находится в противоре
чии с |
тенденцией |
увеличения |
доли спокойной |
стали. |
С |
увеличением |
выплавки |
спокойной стали |
значительно усложни |
лась работа на участках подготовки составов с изложницами и раз ливки стали, в результате чего на многих металлургических заводах уже исчерпаны возможности дальнейшего увеличения ее производ ства. Более того, повышение доли спокойной стали сдерживает уве личение общего производства стали.
Известно, что, кроме полностью раскисленной спокойной и кипя щей сталей, возможен ряд промежуточных или переходных структур, образование которых определяется, в основном, интенсивностью и длительностью газовыделения из стали при ее затвердевании в из ложнице.
Из промежуточных структур значительное практическое приме нение получила полуспокойная сталь, раскисляемая в необходимой степени в печи, ковше или При наполнении изложницы, а также заку поренная кипящая сталь, интенсивность выделения газов из которой регулируется механическим или химическим закупориванием голов ной части слитка в конце или после наполнения изложницы ме таллом.
Стали этих видов разливают в уширенные книзу сквозные из ложницы без утепления, подготовка которых к разливке и разливка в них стали значительно менее трудоемки и более экономичны, чем при использовании уширенных кверху изложниц с утеплением для
разливки спокойных сталей. В связи с этим замена спокойных |
сталей |
1 |
3 |
полуспокойными позволяет увеличить пропускную способность участ ков подготовки составов и разливочных пролетов, а применение тех нологии закупоривания кипящих сталей не вносит практических из менений в организацию работ на этих участках или даже облегчает ее (в условиях химического закупоривания, когда исключается при менение крышек).
При производстве углеродистых и низколегированных |
полуспо |
|||||||
койных сталей вместо спокойных увеличивается на 8—10% |
выход |
|||||||
годного проката из слитков, снижается в 2—5 раз |
расход |
ферроси |
||||||
лиция и в 5 раз и более — алюминия |
на раскисление |
металла, умень- |
||||||
|
|
шается |
на 30—40% |
расход из |
||||
|
|
ложниц, снижается |
|
(примерно |
||||
|
|
в два раза) |
трудоемкость под |
|||||
|
|
готовки разливочных |
составов. |
|||||
|
|
Себестоимость |
(и цена) |
прока |
||||
|
|
та из полуспокойных сталей на |
||||||
|
|
2—9 руб/т |
и более |
(в |
зависи |
|||
|
|
мости |
от марки) ниже, |
чем из |
||||
|
|
спокойных |
с |
аналогичными |
||||
|
|
свойствами. |
|
|
|
|
|
|
|
|
Наряду |
с этим |
применение |
||||
|
|
полуспокойных |
сталей |
вместо |
||||
|
|
спокойных позволяет не только |
||||||
|
|
сохранить, |
но |
в ряде |
случаев |
|||
|
|
(при |
легировании) |
|
повысить |
|||
|
|
надежность |
конструкций и ма |
|||||
|
|
шин и снизить их массу при по |
||||||
|
|
нижении или без повышения их |
||||||
|
|
стоимости. |
|
|
|
|
|
|
Рис. 1. Объем |
производства полу |
Основным |
преимуществом |
|||||
спокойной |
стали в СССР |
полуспокойной |
стали |
по срав |
||||
|
|
нению |
с |
кипящей |
|
является |
||
|
|
улучшение |
|
механических |
свойств, главным образом, повышение однородности и хладостойкости. В некоторых случаях замена кипящей стали полуспокойной при водит к увеличению выхода годного металла.
Однако в связи с увеличением (примерно вдвое) трудоемкости зачистки промежуточного профиля из слитков полуспокойной стали, отлитых сифонным способом, по сравнению с кипящей, а также вследствие увеличения расхода раскислителей такая замена не всег да целесообразна и возможна. Рациональным способом улучшения качества слитков кипящей стали (особенно крупных) является заку поривание, которое значительно уменьшает химическую неоднород ность и улучшает его структуру, что способствует повышению одно родности состава и свойств прокатной продукции. Благодаря умень шению размеров пузырей, слитки закупоренной кипящей стали более равномерно прогреваются и меньше оплавляются в колодцах. В ре зультате раскат имеет лучшую поверхность, чем раскат из слитков обычной кипящей стали, и трудоемкость зачистки снижается. Таким образом, замена кипящей стали полуспокойной целесообразна только в тех случаях, когда задача получения требуемых свойств готовой продукции не может быть решена путем закупоривания кипящей стали.
В i960 г. в СССР было произведено около 0,8 млн. т полуспо койной стали, что составило всего около 1,4% от общейвыплавки стали
4
Т а б л и ц а 1. |
Производство |
стали |
разных |
видов, |
|||
|
на |
заводах МЧМ |
СССР, % |
|
|
||
|
У г л е р о д и с т ая |
сталь |
|
|
|
||
|
|
|
|
кипящая |
|
Н и з к о |
|
|
|
|
|
|
|
|
|
Год |
|
п о л у - |
|
в |
том |
чи |
легиро |
спокой |
|
ванная |
|||||
всего |
ная |
спокой - |
всего |
сле |
х и |
сталь |
|
|
|
ная |
мически |
|
з а к у п о ренная
Легиро ванная сталь
1960 |
84,6 |
39,8 |
1,4 |
43,4 |
0,5 |
6,8 |
8,6 |
1965 |
83,2 |
40,0 |
7,6 |
35,6 |
13,5 |
8,1 |
8,7 |
1970 |
81,2 |
39,8 |
10,4 |
31,0 |
18,3 |
10,4 |
8,4 |
на предприятиях черной металлургии. Рациональная технология ее производства не была разработана, так как не были установлены закономерные связи между параметрами технологии, структурой слитка, качеством стали и свойствами готового проката, а также не был разработан способ контроля технологии производства полуспо койной стали, обеспечивающий получение требуемой структуры слит ка. Был весьма ограничен и сортамент марок полуспокойной стали.
Недостаточная изученность физико-механических и служебных свойств полуспокойной стали не позволила без проведения исследо ваний определить возможные области ее применения, установить не обходимую технологию ее производства и рациональный химический состав. Вследствие этого во многих отраслях народного хозяйства отсутствовали конкретные указания по применению полуспокойных сталей в конструкциях, машинах и изделиях.
Объем производства полуспокойных сталей в СССР значительно увеличился (рис. 1) и в 1970 г. превысил 11,0 млн. т. Однако доля полуспокойной стали в общем балансе потребления металлопроката в народном хозяйстве СССР еще недостаточна и может быть значи тельно увеличена (табл. 1).
Вышеприведенные данные показывают, что благодаря освоению и широкому внедрению полуспокойной стали вместо спокойной доля последней в общем объеме производства стали на металлургиче ских предприятиях в 1960—1970 гг. не увеличилась, несмотря на по вышение требований к свойствам металла и отказ от использования проката из кипящей стали.
Исследования по разработке рациональной технологии произ водства, улучшению свойств, созданию новых марок полуспокойных сталей и определению сферы их применения, а также работы по внед
рению |
полуспокойных сталей |
в |
производство |
металлургических за |
||
водов |
и металлопотребляющих |
|
отраслей народного хозяйства |
были |
||
начаты |
в 1959 г. и проводились Украинским |
научно-исследователь |
||||
ским |
институтом |
металлов |
и |
Институтом |
черной металлургии |
|
(г. Днепропетровск) |
совместно с металлургическими заводами |
«Азов- |
сталь», Коммунарским, Криворожским, Макеевским, им. Петровского с участием ведущих институтов отраслей потребления—ЦНИИ строи тельных конструкций, Н И И бетона и железобетона, Всесоюзного на учно-исследовательского института сельскохозяйственного машино строения. В дальнейшем к этим работам были привлечены Институт
5
электросварки им. Е. О. Патопа АН УССР, Ц Н И И технологии ма шиностроения, НИИ химического машиностроения, ВНИИ по строи
тельству магистральных |
трубопроводов, Донецкий |
угольный инсти |
|||||
тут и др. Работы |
по разработке |
рациональной |
технологии производ |
||||
ства полуспокойной стали проводились также |
Научно-исследователь |
||||||
ским |
институтом |
металлургии |
(г. |
Челябинск) |
Магнитогорским |
||
и Кузнецким металлургическими |
комбинатами. |
|
|
||||
В |
настоящее |
время |
полуспокойная |
сталь |
в СССР производится |
по ГОСТ 380—71, 1050—60* и ряду технических условий для тол
стого |
(4—50 мм) и тонкого (0,2—3,9 |
мм) листа, фасонного |
(с тол |
|||
щиной |
полки до 25 мм) и сортового |
(размером до 120 мм) проката, |
||||
промышленных |
рельсов, |
катанки, шахтной |
крепи, мелющих |
шаров |
||
и других назначений. Освоена технология производства около 30 ма |
||||||
рок |
углеродистой и |
низколегированной |
полуспокойной |
стали |
||
с содержанием |
углерода |
0,05—0,9 и марганца 0,25—1,7%. Некоторые |
стали содержат ванадий (0,05—0,18%), ниобий (0,02—0,04%) и азот
(0,015—0,030%). |
|
|
|
|
|
|
Рациональные |
области |
применения полуспокойных |
сталей вмес |
|
то |
спокойных определены |
в рекомендациях Всесоюзного |
совещания |
||
по |
полуспокойным |
сталям |
(1963 г.), Научного Совета |
по |
проблеме |
«Новые процессы сварки и сварные конструкции» Госкомитета Со вета Министров СССР по науке и технике (1966 г.) и Всесоюзного семинара «Состояние и перспективы применения полуспокойпых ста лей» (1969 г.).
В конце 1971 г. указанные рекомендации по использованию полу спокойной стали вместо спокойной рассмотрены и одобрены Государ ственным Комитетом Совета Министров СССР по науке и технике в качестве обязательных для всех министерств и ведомств, потребляю
щих |
или контролирующих применение металлопроката. |
|
||
|
Расширение |
производства полуспокойной |
стали вместо |
спокой |
ной |
в настоящее |
время является одним из |
основных и |
наиболее |
технически подготовленных мероприятий по экономии металла мас сового назначения при производстве проката из слитка.
|
|
Г л а в а 1 |
|
|
ПРОИЗВОДСТВО И ПРИМЕНЕНИЕ |
||
ПОЛУСПОКОЙНОЙ |
СТАЛИ В СССР И ЗА РУБЕЖОМ |
||
|
Полуспокойную |
бессемеровскую рельсовую сталь |
|
на |
отечественных заводах выплавляли |
еще до револю |
|
ции |
[1]; производство ее сохранялось |
на Енакиевском |
|
металлургическом |
заводе до Великой |
Отечественной |
войны. Сталь раскисляли ферромарганцем и небольшим количеством алюминия. Во время разливки зеркало ме талла в изложнице заливали водой.
Однако только в середине пятидесятых—начале шес тидесятых годов на ряде металлургических заводов приступили к разработке технологии и широкому освое нию производства мало- и среднеуглеродистых полуспо койных сталей [3—17].
На заводе «Азовсталь» с 1955 г. было организовано производство слабораскисленной мартеновской полу спокойной стали Ст. 5 для шахтной стойки, а с 1958 г.— также стали М45 для рельсов узкой колеи. Раскисление этих сталей производили только ферромарганцем в ков ше [2, 5, 10, 11]. Сталь при разливке (сифонной) вела себя, как перераскисленная кипящая — вяло кипела во время наполнения изложниц и образовывала рослую со «свищами» и наплывами головную часть. Тем не менее головная обрезь при прокатке слитков такой стали на блюминге составила 4—6% (для слитков спокойной ста ли 14 —15%). В дальнейшем [18] эти стали начали рас кислять 45%-ным ферросилицием (1 кг/т) и алюминием (80—120 г/т) в ковше. В 1960—1963 гг. на этом заводе была разработана и освоена также технология произ водства стали Ст. Зпс с раскислением ферросилицием
иалюминием в ковше для крупных фасонных профилей
[5].
Впоследние годы для раскисления полуспокойной стали в ковше на заводе применяют только 45%-ный
ферросилиций |
(1,4—1,6 кг/т |
для стали Ст. |
Зпс; 1,2— |
|||
1,4 кг/т для |
стали Ст, 4пс |
и 0,9—1,1 кг/т |
для |
стали |
||
Ст. 5пс и М45пс). |
|
|
|
|||
На Кузнецком металлургическом комбинате в 1959 г. |
||||||
было освоено |
производство |
мартеновской |
полуспокой |
|||
ной стали |
марок |
Ст. 5пс и Ст. бпс для шахтной |
стойки |
|||
и рельсов |
узкой |
колеи. Раскисление производили |
в ков- |
7
ше 45%-ным ферросилицием |
(1 кг/т) |
и алюминием |
(50 г/т). Головная обрезь при |
прокатке |
слитков полу |
спокойной стали на блюминге составляла 4—6% против 14 — 15% для спокойной стали [4, 5, 10, I I ] . К 1964 г. на комбинате были дополнительно освоены полуспокойные^стали 08пс, Ст. Зпс и Ст. 4пс с раскислением в ков ше по такой же технологии (1 —1,5 кг/т 45%-ного ферро силиция и 150 г/т алюминия) для толстого листа, фа сонного и сортового проката [19]. С 1968 г. полуспокой ные стали всех марок выплавляют с систематическим
дораскислением |
головной |
части слитка |
алюминием при |
||||||
разливке сверху; |
расход |
алюминия |
в ковш |
при |
этом |
||||
снижен [20]. |
|
|
|
|
|
|
|
|
|
На Енакиевском металлургическом заводе в 1958— |
|||||||||
1959 гг. было |
освоено |
производство |
бессемеровской по |
||||||
луспокойной |
стали БСт. 5пс для арматуры |
периодичес |
|||||||
кого |
профиля |
и БСт. бпс для рудничных |
рельсов |
типа |
|||||
Р18 |
и Р24 [3, 5, 10, 11]. Обе стали |
раскисляли в |
ковше |
||||||
жидким ферромарганцем, |
а сталь БСт 5пс — еще 45%- |
||||||||
ным |
ферросилицием |
(2,5 |
кг/т). Во |
время |
наполнения |
изложницы (разливка сверху) осуществлялась коррек тировка степени раскисленное™ алюминием (до 80 г/т). В настоящее время на заводе полуспокойные стали ма рок Ст.2—Ст.бпс выплавляют в основном в конвер терном цехе. Раскисление производят в ковше ферро марганцем (3,9—4,6 кг/т), 45%-ным ферросилицием (1,0—1,5 кг/т) и алюминием (0,05 кг/т). Из полуспокой ной стали производят толстый лист, фасонный и сорто вой прокат.
На Ждановском заводе им. Ильича в 1959 г. освоено производство толстолистовой (9—32 мм) мартеновской полуспокойной судовой стали со степенью раскислен ное™ выше нормальной. Раскисление стали производили в ковше 75%-ным ферросилицием и алюминием [5, 10, 12]. В настоящее время на заводе производят полуспо койную сталь марок Ст. 2пс—Ст. 5пс для тонкого и тол стого листа. Сталь выплавляют в большегрузных мар теновских печах и кислородных конвертерах. Раскисле ние производят в ковше45%-и 75%-ным ферросилицием (из расчета получения 0,07—0,11% Si в готовом метал ле) и алюминием.
В 1961 г. на Магнитогорском металлургическом комбинате начато производство полуспокойной стали марок МСт. 1пс—МСт. бпс для фланцевых профилей,
8
кругов (диаметром до 80 мм) и листов |
(толщиной до |
20 мм) и марок 08—20пс — для тонкого |
листа и ленты |
[21]. Сталь раскисляли ферросилицием в ковше из рас чета получения содержания кремния в готовом металле 0,07—0,12% (впоследствии эти нормы были уточнены: 0,05-0,10%).
На заводе им. Петровского полуспокойную сталь на чали выплавлять в конце 1961 г. [22]. К 1964 г. была освоена технология производства мартеновской (МСт.
Зпс) |
и |
конвертерной |
(КСт. |
Зпс, |
КСт. |
5пс, |
К20пс, |
КЛ 53пс, |
КНпс, КТпс |
и КПТпс) сталей для швеллеров, |
|||||
балок, уголков, лемешной полосы, рудничных |
рельсов |
||||||
РЗЗ, фасонного профиля для обода |
автомобиля |
ГАЗ-51 |
|||||
и катанки. Сталь раскисляют |
45%-ным |
ферросилицием |
|||||
и алюминием в ковше. |
|
|
|
|
|
||
Головная обрезь при прокатке слитков полуспокой |
|||||||
ной |
стали составляет |
3—5% |
(для |
спокойной |
14,5%). |
В этот же период на заводе были начаты работы по освоению технологии производства полуспокойной стали Св. 08пс и Св. 08Апс с содержанием кремния до 0,07% для сварочной проволоки вместо кипящей стали анало гичных марок, для которой из-за высокой химической неоднородности около 30% заготовок использовалось на менее ответственные назначения. Опыт работы завода показал, что все заготовки из слитка полуспокойной стали указанных марок могут быть использованы по прямому назначению.
На Макеевском и Криворожском металлургических заводах [5, 10, 11, 23] в 1959—1963 гг. были проведены работы по разработке норм химического состава и ос воению рациональной технологии производства полу спокойной стали Ст. 5пс в арматуре периодического профиля диаметром 10—40 мм для железобетонных конструкций. В дальнейшем на этих заводах была внед рена также сталь Ст.Зпс для фасонного и сортового проката.
|
Производство толстого |
(8—40 мм) листа из полуспо |
|||||||
койной стали Ст.Зпс было освоено |
в 1961 —1963 |
гг. на |
|||||||
Коммунарском металлургическом заводе |
[11, 23]. Сталь |
||||||||
раскисляли в ковше вначале 45%-ным |
ферросилицием |
||||||||
(2 |
кг/т) |
и |
алюминием |
(200—250 |
г/т), затем |
толь |
|||
ко |
45%-ным |
ферросилицием |
(3,5—3,8 кг/т). В |
дальней |
|||||
шем на этом заводе сортамент |
марок и проката |
из полу |
|||||||
спокойной |
стали был значительно |
расширен; |
в |
1968 г. |
9