
книги из ГПНТБ / Силенок, С. Г. Механическое оборудование предприятий строительной индустрии учеб. для студентов вузов
.pdf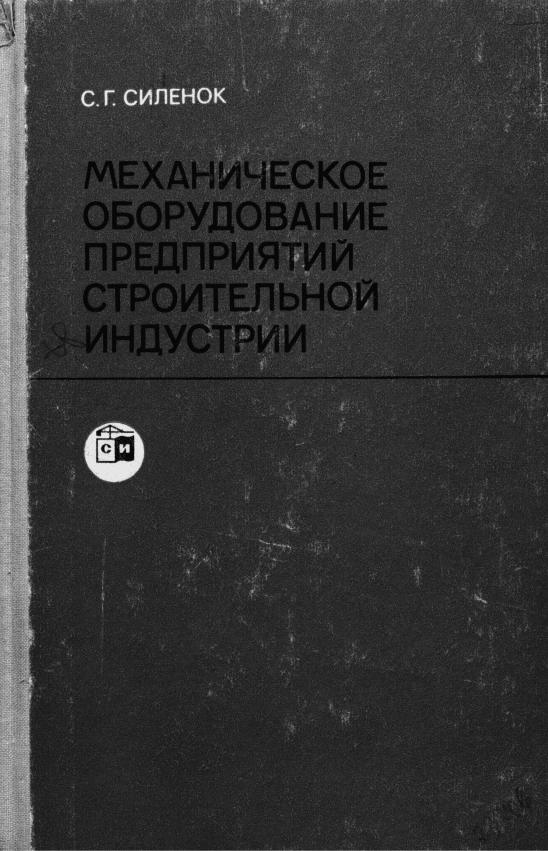
С. Г. С И Л Е Н О К
МЕХАНИЧЕСКОЕ ОБОРУДОВАНИЕ ПРЕДПРИЯТИЙ С Т Р О И Т Е Л Ь Н О Й ИНДУСТРИИ
Допущено Министерством высшего |
и |
среднего |
специального |
образо |
||
вания СССР в |
качестве учебника |
для |
студентов |
вузов, |
обучающихся |
|
по специальности |
«Автоматизация |
и комплексная |
механизация |
строи |
||
тельства» |
|
|
|
|
|
|
М О С К В А
СС Т Р О Й И З Д А Т 1 9 7 3
У Д К 691.002.5(075.8)
|
Силенок |
С. Г. Механическое |
оборудование |
||
|
предприятий |
строительной индустрии. Учебник для |
|||
У, |
вузов. М„ Стройиздат, 1973. 374 с. с ил. |
||||
В учебнике рассмотрено механическое обору |
|||||
|
|||||
|
дование предприятий строительной индустрии для |
||||
|
производства |
цемента, извести и гипса, бетона и |
|||
|
растворов, железобетонных |
изделий, керамических |
|||
|
изделий, строительных изделий на основе пласт |
||||
|
масс. Приведены конструкции машин и установок, |
||||
|
принципы их действия, основные расчеты, а также |
||||
|
схемы компоновок оборудования отдельных линий |
||||
|
и предприятий в целом. |
|
|
||
|
Учебник предназначен для студентов вузов, |
||||
|
обучающихся |
по специальности |
«Автоматизация |
||
|
и комплексная механизация |
строительства». |
|||
|
Табл. 9, |
рис. 170, список лит.: 27 назв. |
Рецензенты: кафедра «Машины и оборудова ние заводов строительных материалов» ВЗИСИ и канд. техн. наук Б. В. Клушанцев, инж. Ю. С. Гризак, канд. техн. наук К. М. Королев, инж. А. А, Сусников, д-р техн. наук И. А. Булавин,
© Стройиздат, 1973 г.
ПРЕДИСЛОВИЕ
Намечая пути ускорения научно-технического прогресса страны,
Директивы |
X X I V съезда |
КПСС |
по |
пятилетнему |
плану развития |
|
народного |
хозяйства |
СССР на 1971 —1975 гг. |
предусматривают |
|||
повышение |
технического |
уровня |
предприятий |
промышленности |
||
строительных материалов, |
ускорение |
механизации и автоматиза |
||||
ции производственных |
процессов. |
|
|
|
Настоящий учебник предназначен для студентов вузов, спе циализирующихся в области автоматизации предприятий строитель ной индустрии (строительных материалов и изделий).
Вучебнике рассмотрено механическое оборудование и прин ципы его действия, приведены расчеты основных машин и устано вок, а также схемы компоновки оборудования комплексных тех нологических линий и предприятий в целом. Эти сведения позволят студентам приобрести определенные навыки самостоятельной инже нерной разработки конструкций оборудования, производства рас четов и компоновок установок и технологических линий. Для отдельных видов оборудования (например, для дробильных машин, помольных установок, вращающихся печей, холодильников) изло жены основы их автоматизации.
Вкниге обобщен опыт создания, наладки и эксплуатации в про изводственных условиях наиболее прогрессивных и перспективных, подлежащих автоматизации машин и установок. В учебнике рас смотрено оборудование только наиболее развитых и ведущих от раслей— нерудных строительных материалов,'вяжущих (цемента, извести и гипса), бетонов и растворов, изделий на основе вяжущих (железобетонных, силикатных, гипсовых и асбестоцементных), ке рамических и полимерных строительных изделий.
Курс механического оборудования применительно к специали зации «Автоматизация предприятий строительной индустрии» соз дается впервые, поэтому автор с благодарностью примет все кри тические замечания и пожелания.
1*
Р а з д е л I
ДРОБИЛЬНЫЕ, СОРТИРОВОЧНЫЕ И ОБОГАТИТЕЛЬНЫЕ МАШИНЫ, УСТАНОВКИ И ЗАВОДЫ
Г л а в а 1
ОСНОВНЫЕ СВЕДЕНИЯ О ДРОБЛЕНИИ
В большинстве отраслей промышленности строительных материа лов и особенно на предприятиях нерудных строительных материа лов поступающее в производство сырье подвергается дроблению, помолу, сортировке (обогащению).
Нерудные строительные материалы — щебень, гравий и песок — применяют в качестве заполнителя при изготовлении бетонов для гражданского, промышленного и автодорожного строительства, а также для строительства гидротехнических сооружений. Щебень широко применяют также и для балластировки железных дорог.
Щебень изготовляют путем дробления твердых горных пород магматического (гранит, сиенит, диорит, габбро, кварцевые пор фиры, диабазы, базальты и др.), осадочного (известняки, доломиты, песчаники) и метаморфического (гнейсы, кварциты, мраморы) про
исхождения. |
|
|
Гравий |
представляет собой |
зерна окатанной формы размером |
3 (5) — 70 |
мм, образовавшиеся |
в результате естественного разру |
шения горных пород. Зерна размером 70—150 мм называют круп ным гравием, а крупнее 150 мм — валунами.
Песок для строительных работ применяют природный (естест венный) и искусственный. Природный песок (горный и речной) представляет собой смесь зерен размером до 5 мм.
В качестве заполнителей для легких бетонов применяют пори стые каменные материалы:
природные — пемзы, вулканические шлаки и туфы, ракушеч ники, доломиты и др.;
искусственные — металлургические и топливные шлаки, а также заполнители, получаемые после переработки природных каменных материалов путем вспучивания и поризации (керамзитовый гравий, шлаковая пемза, аглопорит, перлит, вермикулит и др.).
Заполнители для легких бетонов отличаются большим разнооб разием объемных весов и пределом прочности на сжатие.
Полученные при взрыве (добыче) на карьерах куски горной массы имеют разную крупность, начинай от каменной пыли и кончая
Глава 1. Основные сведения о дроблении |
5 |
максимальными кусками примерно до 1000—1200 мм; следовательно, для получения конечного продукта — щебня, например крупно стью 0—40 мм, необходимо раздробить исходный кусок в 1000:40 = = 25 раз! Одним из основных показателей дробильных машин является степень измельчения.
Под степенью измельчения принято понимать отношение сред невзвешенного размера куска исходного материала D c p . „ к средне взвешенному куску конечного (готового) продукта dc p .в . Таким образом, степень измельчения (дробления) может быть выражена следующей формулой:
ö c p . в и dc p . в определяют ситовым анализом.
Степень измельчения зависит от конструкции дробильной ма шины, физико-механических свойств перерабатываемой каменной породы и абсолютной величины кусков. С увеличением степени из мельчения производительность дробильных машин снижается, а рас ход энергии возрастает.
Каждой конструкции дробильной машины при максимальной производительности соответствует оптимальная степень измельче ния: так, например, для щековых и конусных дробилок крупного
дробления |
і = 3 ч- 5, для однороторных молотковых дробилок при |
дроблении |
неабразивных пород і = 10 -f- 15 и двухроторных — |
і = 30 -s- 40. |
Когда требуется большая степень измельчения, дробление осу ществляют в несколько стадий, т. е. последовательно устанавливают ряд дробильных машин, различных по конструкции и техническим характеристикам. При этом постепенно переходят от крупного к среднему и затем мелкому дроблению с таким расчетом, чтобы эффективность дробления на последующих стадиях была выше, а затраты энергии меньше.
Количество стадий дробления является основным показателем, характеризующим технологическую схему дробильно-сортировоч- ного завода. Обычно современные дробильно-сортировочные заводы имеют две-три стадии дробления и реже четыре. При определении необходимого количества стадий дробления учитывают максималь ные размеры отдельных кусков и их количество в массе.
Процесс дробления отличается большим расходом энергии и быстрым износом деталей машин, находящихся в соприкосновении с дробимым материалом. Такие детали изготовляют большей частью из дорогих легированных сталей.
Перед дроблением из исходного материала следует удалять фракции готового продукта, так как, распределяясь между более крупными кусками, они повышают упругость измельчаемой массы. Для этого перед дробильной машиной устанавливают классифика-
6 Глава Г. Основные сведения о дроблении
тор (грохот), на который подают исходный материал. Мелкие куски материала проходят через отверстия сита грохота, а крупные поступают в дробильную машину. Предварительное грохочение предотвращает переизмельчение мелких кусков, сокращает расход энергии, а также уменьшает износ рабочих органов дробильной машины.
При переработке нерудных строительных материалов машины могут работать по открытому и замкнутому циклам.
При дроблении по открытому циклу (рис. 1-1, а) материал про ходит через дробильную машину только один раз, при этом куски конечного продукта получаются неодинаковыми по величине.
При дроблении по замкнутому |
циклу (рис. 1-1, б) крупные фрак |
ции оставшегося на сите материала после сортировки возвращаются |
|
на повторное-дробление. Так как материал неоднократно проходит |
|
через дробильную машину, то нагрузка (циркуляционная) на нее, |
|
естественно, увеличивается, однако машина работает с большей |
|
производительностью, чем при |
открытом цикле, и выдает более |
равномерный |
продукт. При замкнутом цикле дробления материал |
а) |
б) |
Рис. 1-1. |
Схема циклов дробления |
|
1 — д р о б и л ь н а я машина; |
2 , 3 |
— к л а с с и ф и к а т о р (грохот); 4 — пи |
татель |
пластинчатый |
не переизмельчается и уменьшаются расход энергии, а также износ рабочих органов машины. Недостаток замкнутого цикла дробления заключается в том, что с ростом числа машин и транспортирующих механизмов увеличиваются высота зданий и капитальные затраты.
Применяются одностадийные, двухстадийные, трехстадийные и реже четырехстадийные схемы дробления. При определении числа стадий дробления следует учитывать мощность предприятия, раз меры кусков исходного и конечного продукта, а также конструкции дробилок. Число стадий дробления является основным показателем, определяющим схему дробильно-сортировочного завода.
Одностадийную схему дробления (рис. 1-2, а) применяют на предприятиях небольшой мощности и при переработке исходного
Глава 1. Основные сведения о дроблении |
7 |
материала с наибольшим размером кусков 400—450 мм. После грохочения сверхмерные куски (не прошедшие сито грохота 3) поступают в щековую дробилку 2 для повторного дробления. Как видно из схемы, работа совершается по замкнутому циклу.
Двухстадийную схему дробления (рис. 1-2, б) применяют на заводах средней и большой мощности и при переработке кусков исходного материала размером до 700—1000 мм. Величина кусков
а) |
б) |
Рис. 1-2. Схемы стадий дробления
/ — питатель; 2 — щековая д р о б и л к а |
п е р в и ч н о г о д р о б л е н и я ; |
3 —- гро |
|
хоты (одно - и трехситные); 4 — |
к о н у с н а я д р о б и л к а второй стадии д р о б |
||
л е н и я ; 5 — к о н у с н а я д р о б и л к а |
третьей |
стадии д р о б л е н и я ; 6 — |
б у н к е р а |
не позволяет осуществить в одной машине (стадии) дробление до крупности 10—20; 20—40; 40—70 мм (см. главу 2 настоящего раз дела). Количество сверхмерных кусков в дробимом камне и в этом случае будет значительным, и это потребует установки дробилки для вторичного дробления (вторая стадия). Окончательная сорти ровка осуществляется на втором грохоте, куда поступает продукт вторичного дробления, а также материал, отсортированный на пер вом грохоте. В этой схеме работа совершается также по замкнутому циклу.
Трехстадийную схему дробления (рис. 1-2, б) применяют на за водах большой производительности и при переработке исходного материала с размером кусков до 1000—1200 мм.
8 Глава 2. Способы дробления. Классификация оборудования
Трехстадийная схема является более гибкой и рациональной, так как обеспечивает выпуск в требуемых пределах как крупных, так и мелких фракций и применяется в качестве основной при дроб лении прочных каменных пород.
При дроблении малоабразивных (осадочных) каменных пород, когда снижается износ рабочих органов, находящихся в контакте с дробимым материалом, рекомендуется применять роторные дро билки (вместо щековых и конусных). Они имеют сравнительно боль шую степень измельчения, что позволяет осуществлять в одном агрегате две стадии дробления. Схема с роторными дробилками имеет преимущества перед схемой со щековыми и конусными: уменьшается вес установленного оборудования, сокращается расход энергии и улучшается форма конечного продукта.
Г л а в а 2
СПОСОБЫ ДРОБЛЕНИЯ. КЛАССИФИКАЦИЯ ОБОРУДОВАНИЯ. ОСНОВНЫЕ ЗАКОНЫ ИЗМЕЛЬЧЕНИЯ
§ 1. Способы дробления
Основными способами дробления, осуществляемыми рабочими органами дробильных машин, являются раздавливание (сжатие), удар, истирание и раскалывание.
Часто эти способы сочетают друг с другом, например, раздавли вание с ударом, удар с истиранием и т. п., при этом комбинируется действие сил изгибающих, срезающих и разрывающих.
Выбор способов дробления зависит от физико-механических свойств материала (твердости, хрупкости, вязкости, загрязненности глиной, склонности к замазыванию дробильной камеры), началь ной величины кусков и требуемой степени измельчения.
Твердые материалы наиболее эффективно измельчаются ударом или раздавливанием, пластические (глина) — раздавливанием в со четании с истиранием, хрупкие материалы (уголь) — раскалыва нием.
От правильного выбора типа дробильной машины, а следова тельно, и способа дробления в значительной степени зависят каче ство готового продукта и производительность агрегата. Никогда не надо стремиться осуществлять полное измельчение в одной ма шине, всегда выгоднее и целесообразнее стадийное дробление по следовательно на нескольких соответствующих по размерам и кон струкциям дробильных машинах.
В настоящее время созданы и успешно эксплуатируются дро билки различных конструкций. Основные требования, которым должна удовлетворять любая дробилка, сводятся к следующему.
§ 1. Способы дробления |
9 |
1. Конструкция и размеры загрузочного отверстия должны соответствовать прочности дробимого материала и размерам его отдельных кусков: так, например, дробилка, измельчающая твер дый материал, должна иметь достаточно большой запас прочности конструкции и ширина загрузочного отверстия должна быть больше размера наибольших кусков в поперечнике на 30—40%. Это пре дотвращает явление «зависания» кусков в приемном отверстии, сни жает простои оборудования, связанные с извлечением «негабарита», и создает благоприятные условия для автоматизации технологиче ского процесса.
2.Для технологической увязки последовательно работающих дробилок и надежной работы систем автоматизации необходимо, чтобы приемное отверстие дробилок последующей стадии было на 60—80% больше разгрузочной щели дробилок предыдущей стадии.
3.Дробилка должна иметь некоторый запас (15—20%) произво дительности, чтобы в случае увеличения количества поступающего материала не было перегрузки.
4. Дробление — весьма энергоемкий процесс, поэтому удель ный расход энергии должен быть небольшим. Следует помнить об щее свойство всех дробилок: при увеличении степени измельчения уменьшается производительность машины и увеличивается расход энергии.
5.Необходимо сводить к минимуму количество пыли, образую щейся в процессе дробления. Пыль и каменная мелочь играют роль амортизатора (подушки). Заполняя пространство между крупными кусками, они смягчают удар и тем самым снижают эффективность дробления: уменьшается производительность, увеличиваются рас ход энергии и износ дорогостоящих деталей дробилок. Пыль вредна для здоровья обслуживающего персонала.
6.Раздробленный материал следует из дробилки выгружать быстро и непрерывно во избежание его переизмельчения, чрезмер ного пылеобразования и усиления износа деталей.
7.Конструкция дробилки должна позволять быстро и легко заменять износившиеся или поломавшиеся детали.
8.Раздробленный материал должен состоять из кусков по воз
можности одного размера и кубообразной формы, что особенно важно при дроблении щебня для бетонных работ.
9. Дробилка должна иметь легкие и недорогие предохранитель ные детали. В случае попадания недробимых предметов (кусков рельсов, зубьев ковша экскаватора и др.) такие детали деформи руются или ломаются, тем самым предохраняя основные дорого стоящие детали дробилки от поломки.
Как и всякая машина, дробилка должна быть прочной, дешевой, простой в изготовлении и эксплуатации, не требовать высококвали фицированного обслуживания и потреблять минимальное количе ство энергии.