
книги из ГПНТБ / Де Барр, А. Е
.pdf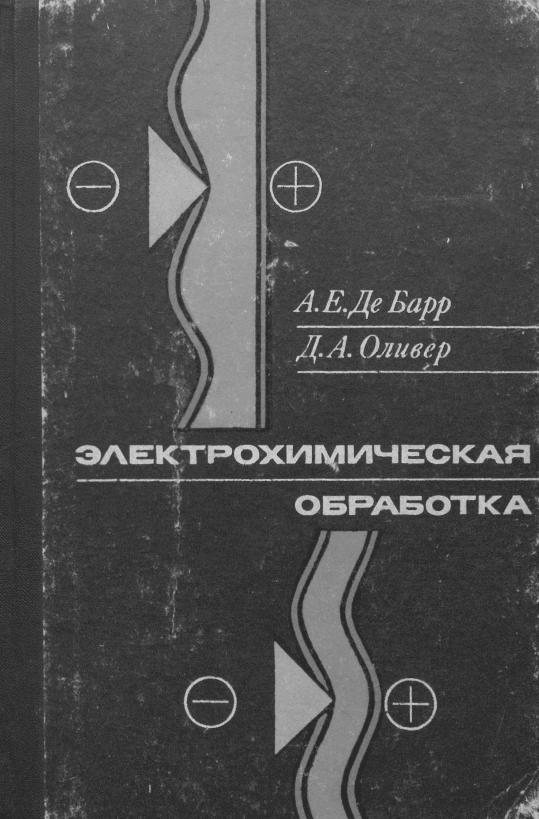
Electrochemical
Machining
edited by
A E. DE BARR
B . S C , F.1NST.P
and
D. A. OLIVER
C . B . E . , M . S C . ( E N G . ) , F . I . M . , F . INST . P
MACDONALD: LONDON
А. Е. ДЕ БАРР, Д. А. ОЛИВЕР
Электрохимическая
обработка
Перевод |
с английского |
|
П е р е в о д ч и к и : |
||
Е. М. РУМЯНЦЕВ, |
Е. А. |
КУЗНЕЦОВА, |
Е. Л. |
ФОРТУНАТОВ |
М о с к в а « М А Ш И Н О С Т Р О Е Н И Е » 1973
Б 21 УДК 621.9.047
-"ТоЄГ'пУВЛРГЧНЯН
НАУЧНО-ТЕХНИЧЕСКАЯ
Б И Б Л И О Т Е К А СОЄР
Де Барр А. Е., Оливер Д. А. Электрохимическая обработка (пер. с англ.). М., «Машиностроение», 1973, 184 с.
Электрохимический метод обработки деталей с по мощью интенсивного контролируемого анодного рас творения является одним из новых наиболее произво дительных и перспективных. Этим методом обрабаты вают детали из сверхтвердых, вязких и жаропрочных материалов, широко применяемых в промышленности. Цель книги — обобщить имеющиеся сведения по элек трохимической обработке, показать ее современное состояние и области внедрения. В книге освещены важ нейшие вопросы теории и практики применения элек трохимической размерной обработки, особенности кон струирования оборудования, методика расчета электро дов-инструментов, известные способы очистки и пере работки электролита и т. д. Представлен справочный и графический материал, пригодный для расчета технических параметров процесса.
Книга предназначена для инженерно-технических и научных работников, специализирующихся в области электрохимической размерной обработки. Табл. 11, ил. 93.
Редактор канд. техн. наук Е. М- |
Румянцев |
Р е ц е н з е н т канд. техн. наук А. К- Алтынбаев
Предисловие к русскому изданию
Прежде чем предложить читателям перевод книги англий ских авторов А. Е. Де Барра и Д. А. Оливера «Электрохимиче ская обработка», хотелось бы обратить их внимание на некоторые вопросы развития электрохимического метода. Этот метод нахо дит все большее применение в различных отраслях современного машиностроения. Первые опыты по размерной электрохимиче ской обработке металлов были проведены около 40 лет назад в СССР. Разработка основ электрохимического метода и техно логического его применения принадлежит талантливому совет скому ученому В. Н. Гусеву (1904—1956 гг.). В последующие годы как самим В. Н. Гусевым, так и другими учеными были разработаны различные варианты электрохимической технологии и созданы основы теории электрохимического метода. Электро химическую обработку применяют для получения профиля пера турбинных и компрессорных лопаток, ковочных штампов и прессформ, корпусных и кольцевых деталей, прошивки отверстий и щелей, заточки инструмента, удаления заусенцев и др.
Начальный период развития метода характеризуется тем, что наряду с его использованием в производстве происходило накоп ление экспериментальных и статистических данных; делались попытки теоретических обобщений, которые позволили бы зара нее, без испытаний, предсказать конечные результаты обработки. Позже появилось стремление к выявлению основных зависимостей процесса, которые позволяют управлять процессом электрохими ческой обработки.
Успехи, достигнутые в области электрохимического образо вания деталей сложной формы, и прежде всего лопаток турбин и компрессоров, а также полостей ковочных штампов, достаточно полно изложены в книге В. А. Головачева и др. «Электрохимиче ская размерная обработка деталей сложной формы». Попытка обобщения накопленного материала в области теории и практики электрохимической обработки с учетом опыта отечественных и зарубежных заводов сделана в монографии И. И. Мороза и др. «Электрохимическая обработка металлов».
&
В настоящее время в СССР значительные успехи достигнуты в области моделирования электрических полей и решении задач формообразования поверхности при электрохимической обработке, сделаны попытки аналитического расчета простых форм инстру ментов, обеспечивающих достаточно высокую точность изготов ления отверстий и полостей. Созданы математические модели, учитывающие гидродинамику потока электролита, для опреде ления формы поверхности, получаемой при электрохимической обработке, и методики определения погрешностей, припусков и качества обработки. В области теории разработаны оригиналь ные методики прогнозирования обрабатываемости металлов и сплавов в условиях электрохимической обработки (ИЭ АН СССР).
Впредлагаемой книге довольно полно освещены вопросы, встре чающиеся в теории и практике электрохимической обработки. Приведены рекомендации' по конструированию оборудования и электродов-инструментов, методы очистки электролита и их экономическое сравнение, справочный материал по применению коррозионностойких материалов и их стойкости в различных средах. Теоретические разработки, представленные в книге, инте ресны для оценки уровня развития теории электрохимической обработки за рубежом.
Вглавах книги, касающихся теоретических и эксперимен тальных исследований рабочего зазора, электролитов, а также гидродинамических характеристик потока электролита, упомя нуты работы, которые были выполнены в Советском Союзе в пос ледние годы.
Приведенные в гл. 4 уравнения имеют тот недостаток, что при их выводе делался ряд допущений, с которыми нельзя согла ситься. Получение равновесного зазора зависит не только от постоянных скорости подачи и напряжения, но и от стабилизации ряда других параметров: температуры, электропроводности, ско рости протекания электролита, его газонасыщенности и т. д., которые не были учтены при выводе этих уравнений
Несомненный интерес представляют материалы гл. 6, в ко торой рассмотрены электролиты в зависимости от свойств метал лов и их сплавов, а также приведены сведения по кислотным и газообразным электролитам.
Вгл. 7 систематизирован обширный материал по очистке электролитов различными методами, восстановлению их и реге нерации шлама. Материал этой главы имеет прикладное значение, он ценен тем, что отражает все вопросы с учетом нейтрализации сточных вод.
Вгл. 9 приведено решение уравнения Лапласа ступенчатым методом («методом шагов») для определения предполагаемой формы детали и профиля инструмента и необходимая для этого аппаратура. Метод расчета предполагает, что проводимость элек тролита постоянна, в действительности же она меняется с повы шением температуры, поэтому рассчитанные формы : инструмента 6
и |
детали |
должны |
рассматриваться |
как первые приближения |
к |
окончательным |
формам. |
|
|
|
Работы, |
выполненные в Советском |
Союзе, позволяют модели |
ровать задачи формообразования с учетом влияния гидродина
мики, а созданная |
аппаратура осуществляет выдачу' |
решения |
|||
в |
непрерывном режиме. |
|
|
||
|
Материал гл. 11 подтверждает правильность одного из основ |
||||
ных направлений разработки и создания |
стабилизированных |
||||
источников |
питания |
с быстродействующими |
системами |
защиты |
|
от |
коротких |
замыканий. |
|
|
|
|
К приводящимся в книге данным следует относиться осторожно, |
так как авторы преследуют и рекламные цели. В целом моногра фия позволяет судить об уровне теоретических и технологических разработок, направлениях создания оборудования и источников питания за рубежом, так как авторы пользовались информацией английской научно-исследовательской ассоциации станкострои тельной промышленности и ряда фирм, выпускающих и эксплуа тирующих электрохимическое оборудование.
Канд техн. наук Е. М. Румянцев Инж. Е. П. Фортунатов
Г л а в а |
1 |
ВВЕДЕНИЕ |
|
1. ВОЗМОЖНОСТИ ОБЫЧНЫХ |
МЕТОДОВ ОБРАБОТКИ |
Станки с механическим приводом являются станками сравни тельно недавнего происхождения, и большинство из тех, с кото рыми мы знакомы, были разработаны за последние 180 лет. При мерно только в 1800 г. появились сведения о технологии металло режущих станков, которая быстро совершенствовалась. В повсе дневной практике использовали закаленную и отпущенную инстру ментальную сталь, чтобы резать отожженный материал, который, если требовалось, закаливали и отпускали после обработки.
Если два шара одинакового радиуса из различных материалов сжать вместе, то они деформируются, но шар, из более мягкого материала деформируется больше твердого. Аналогично, если два шара различного радиуса из одинакового материала сжать
вместе, то |
шар большего радиуса деформируется больше шара |
|
с |
меньшим |
радиусом, и если маленький твердый шар сжимается |
с |
большим |
мягким шаром, большая деформация наблюдается на |
большем шаре (рис. 1.1, а). По мере того как давление между двумя шарами увеличивается, достигается предел пластичности в большом шаре и наступает пластическая деформация (рис. 1.1,6). При дальнейшем увеличении давления начнется более глубокое проникновение маленького шара в большой, но часть приложен ной силы будет расходоваться на преодоление трения, так как один шар будет вдавливаться в другой (рис. 1.1, в).
Описанное явление составляет основу всех обычных процес сов обработки металла (или дерева, пластика и т. д.). Заточенный инструмент из твердого материала врезается в более мягкую деталь, часть которой, таким образом, удаляется в виде стружки по мере продвижения детали или инструмента (рис. 1.2). Чем тверже и острее режущий инструмент, тем меньшая сила требуется для снятия стружки, но следует учитывать и другие факторы. Вершина резца должна быть достаточно прочной, противостоять действующим на нее силам, а материал резца должен быть стой ким против сил трения. Более того, работа по преодолению сил трения и пластической деформации детали приводит к повышению температуры вершины инструмента и детали. Повышение темпе ратуры увеличивает пластическую деформацию детали, а также приводит к возрастанию деформации и износа резца.
Мягкие материалы можно обрабатывать относительно легко, часто на скоростях свыше 15 ООО с м - м и н - 1 для дерева или алю-
миния. Однако по мере увеличения твердости материала экономич ная скорость резания снижается; она определяется в основном производительностью обработки в зависимости от стоимости изно шенного или поврежденного режущего инструмента. Но обычно твердые материалы могут обрабатываться, если вообще это воз можно, только на низких скоростях резания. Это же касается и специальных жаропрочных материалов, которые не склонны
а) |
6) |
Рис. 1.1. Схема |
пластической деформации |
к пластической деформации и, следовательно, трудно обрабаты ваются резанием. Некоторые современные высокопрочные леги рованные стали должны обрабатываться в закаленном или отпу щенном состоянии, так как они тверды и очень вязки. В резуль
тате |
этого |
нельзя |
|
найти |
инстру |
|
||
ментальные |
материалы, |
которые |
|
|||||
имели |
бы |
достаточную твердость |
|
|||||
и прочность для |
резания |
на эко |
|
|||||
номичных |
скоростях таких мате |
|
||||||
риалов, |
как |
титан, |
нержавеющая |
|
||||
сталь, |
нимоник |
и |
аналогичные |
|
||||
им жаропрочные |
и |
труднообраба |
|
|||||
тываемые |
сплавы. |
|
|
|
|
|||
Быстрое развитие технологиче |
|
|||||||
ски |
развитых отраслей |
промыш- |
Рис. 1.2. Схема резания металла: |
|||||
Л Є Н Н О С ТИ — |
|
а В И а Ц И О Н Н О Й , |
ЯДер- |
1 — деталь; 2 — с т р у ж к а ; 3 — инстру - |
||||
ной |
и т. д. — сопровождалось по- |
м е и т |
вышением доли использования труднообрабатываемых сплавов. Материалы и способы обработки, используемые в этих отраслях промышленности, применяют и в других отраслях, в результате чего характер металлообработки начинает изменяться. Тради ционные способы резания металлов больше не соответствуют современным требованиям, и нет никакой уверенности в том, что они и в дальнейшем будут отвечать этим требованиям.
Хотя скорость резания таких материалов, как низкоуглеро дистая сталь, в результате успехов технологии станкостроения и режущих инструментов удваивается примерно каждые 10 лет, предельная прочность на разрыв материалов, которые можно обрабатывать, например, со скоростью 3000 см-мин"1 , удваи вается примерно только каждые 50 лет (рис. 1.3). Кроме того, предельная прочность на разрыв используемых материалов,
по-видимому, удваивается примерно каждые 20 лет. Следова
тельно, |
уже наблюдается |
упадок технологии |
металлообработки |
||||||||
в некоторых отраслях |
промышленности (рис. 1.4). |
|
|
||||||||
Отсюда вытекает, что новым подходом к металлообработке |
|||||||||||
является |
решение проблем, возникших в |
результате |
появления |
||||||||
и использования^ труднообрабатывае |
|
|
|
|
|
||||||
мых |
материалов. |
Предпринимались |
|
|
|
|
|
||||
попытки |
|
преодоления |
этих |
труднос- |
|
|
|
|
|
||
|
|
|
|
|
|
|
SO |
|
|
|
|
|
|
|
|
/ |
|
|
60 |
|
|
|
|
|
|
|
|
|
|
- |
|
|
|
|
|
|
|
|
|
|
|
|
|
|
|
|
|
W 2ІО0 |
|
|
|
2 |
^ |
15000 S |
|
|
|
|
|
І |
|
|
|
в |
|
|
\\ |
|
|
||
|
|
|
|
|
|
|
|
|
|||
%9200 • |
|
|
|
|
|
|
\ |
|
|||
|
|
|
|
1,000 g |
|
|
|
|
|||
g- |
|
|
|
|
|
5 |
|
|
|
\ |
|
|
|
|
|
|
20 |
|
|
\ |
|
||
а: |
|
|
|
|
|
\JO0O І |
|
|
\ |
||
|
|
|
|
|
|
|
|
|
|
\ |
|
- I 2300 |
|
|
|
|
|
-A1500 |
|
|
|
|
\ |
|
|
|
|
|
|
|
|
|
\ \ |
||
|
|
|
|
|
|
|
|
|
|
||
|
no |
|
1920 mo |
ran |
mm |
|
1955 |
I960 |
1952 1969 |
I960 |
i960 1970г |
Рис. 1.3. Прочность |
материалов |
и скорости |
Рис. 1.4. Диаграмма применения |
||||||||
|
|
|
резания |
металлов: |
|
обработки металлов |
резанием |
||||
/ — скорость |
р е з а н н я |
н и з к о у г л е р о д и с т ы х мате |
|
|
|
|
|
||||
риалов; |
2 |
— прочность |
материалов, |
обрабатывае |
|
|
|
|
|
||
мых со |
скоростями р е з а н н я 30 м/мнн; 3 — проч |
|
|
|
|
|
|||||
|
ность |
материала корпуса ракеты |
|
|
|
|
|
тей, например, путем горячей обработки, при которой деталь на гревают для увеличения скоростей резания, или путем примене ния абразивных методов, или таких как ультразвуковая обра ботка. Успех, однако, был частичным. Необходим метод, при ко тором скорость обработки не зависела бы от твердости детали.
2. НОВЫЕ МЕТОДЫ ОБРАБОТКИ
Наметились два основных направления р решении упомянутой выше проблемы — термические и химические методы обработки; для того и другого направления характерна независимость ско рости съема металла от его твердости.
Термические методы обработки основаны на том, что путем концентрации энергии на маленьком участке детали материал
можно расплавить |
или испарить. |
Энергия |
может |
подаваться |
|
в форме |
теплоты |
(газопламенная |
или плазменная |
обработка), |
|
света (лазеры) или путем электронной бомбардировки |
(электрон |
||||
ный луч и электрическая ^эрозия). Используя |
плотность энергии |
||||
порядка |
108—108 Вт - см - 2 в 'виде |
кратковременных |
импульсов, |
можно удалить металл с поверхности детали без какого-либо
значительного изменения в поверхностных слоях. |
Характерные |
показатели новых методов обработки представлены |
в табл. 1.1. |
10 |
|