
книги из ГПНТБ / Иванов, Г. С. Эксплуатационная надежность и совершенствование технологии изготовления железобетонных шпал
.pdf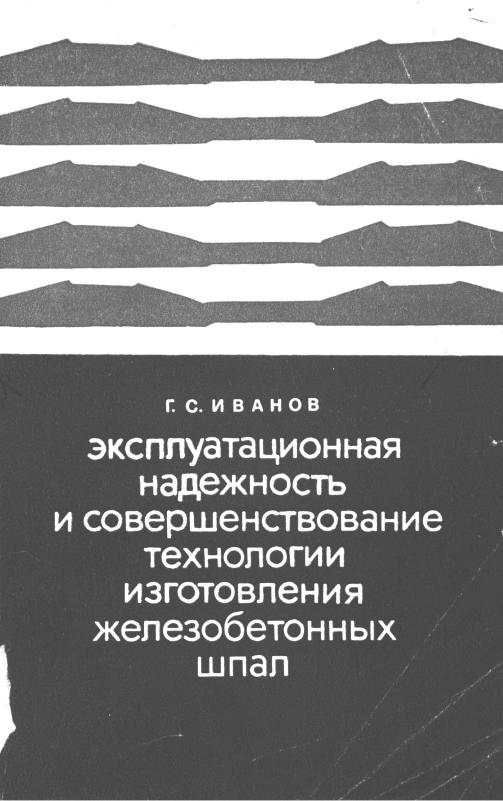
Г. С. ИВАНОВ
ЭКСПЛУАТАЦИОННАЯ
НАДЕЖНОСТЬ
И СОВЕРШЕНСТВОВАНИЕ
ТЕХНОЛОГИИ
ИЗГОТОВЛЕНИЯ
ЖЕЛЕЗОБЕТОННЫХ
ШПАЛ
М О С К В А «ТРАНСПОРТ» 1974
УДК 625.142.42—(192+666.982.2—423
Эксплуатационная надежность и совершенство вание технологии изготовления железобетонных шпал. И в а н о в Г. С. «Транспорт», 4974, стр. 1160.
В книге рассмотрены повреждения и дефекты железобетонных шпал, а также меры по их предот вращению; дан анализ отечественного и зарубежно го опыта изготовления железобетонных шпал и их долговечности при работе в пути. Содержатся реко мендации по совершенствованию заводского произ водства шпал на основе изучения взаимосвязи меж ду возникающими в пути дефектами шпал и , техно логическими приемами их изготовления. Освещены вопросы автоматизации изготовления шпал.
Рассчитана на инженерно-технических работников путевого хозяйства, а также инженерно-технический персонал заводов железобетонных конструкций и проектных организаций.
Рис. 62, табл. 29, библ. 32.
И 31802(31801)-169 049(01)-74
© Издательство «Транспорт». 1974.
ОТ АВТОРА
Достигнутые успехи в области промышленного, гражданс кого и транспортного строительства в Советском Союзе нераз рывно связаны с интенсивным развитием заводского производ ства конструкций и деталей из сборного железобетона. Наи большее применение в транспортном строительстве сборный железобетон получил в мостостроении, при электрификации железных дорог и капитальном ремонте верхнего строения пу ти, в тоннелестроении, а также в конструкциях служебно-тех нических и жилых зданий.
Важным элементом верхнего строения являются шпалы. Из вестно, что средний срок службы деревянных шпал на сети железных дорог СССР составляет примерно 16 лет, а для укладки одного километра пути требуется вырубить почти два гектара лучшего по качеству леса. Объем заготавливаемых ежегодно шпал превосходит 5 млн. м3, на это идет около 8 млн. м3 шпаль ной древесины.
Применение железобетонных шпал становится экономичес ки целесообразным, если обеспечена их высокая долговечность, которая зависит как от качества их изготовления, так и от ус ловий эксплуатации. Поэтому ведутся обширные исследования по определению оптимальных условий работы пути с различны ми железобетонными основаниями и экономически рациональ ной сферы их применения на сети железных дорог СССР.
За последние 15 лет в нашей стране на основе комплексных исследований конструкций шпал, технологии их изготовления, методов укладки и содержания пути создана новая отрасль промышленности по заводскому изготовлению железобетонных шпал, выпуск которых непрерывно увеличивается. Большой вклад в создание рациональных конструкций железобетонных шпал, технологии их изготовления, укладки в путь и норм экс плуатации внесен трудами советских ученых, инженеров-проек- тировщиков, специалистами шпальных заводов и служб пути.
Важную роль в становлении на научной основе и развитии массового производства железобетонных шпал в Советском Со юзе сыграла разработка специальных нормативных докумен тов— технических условий и ГОСТов.
3 .
В то же время накопленный опыт проектирования заводов, изготовления и эксплуатации шпал требует критического ана лиза с точки зрения определения путей дальнейшего развития и совершенствования производства. Это тем более необходимо, поскольку на ряде участков пути после непродолжительного срока эксплуатации были случаи преждевременного разруше ния шпал и симптомы прогрессирующего развития в них раз личных дефектов.
Не все шпалы, выпускаемые заводами, удовлетворяют тре бованиям ГОСТа, высока себестоимость их изготовления.
За истекший период в существующей технологии и приме няемом оборудовании выявлен ряд недостатков, от которых зависит качество шпал и их эксплуатационная надежность. В настоящей книге автор поставил перед собой задачу изложить выявленные за это время основные направления совершенство вания технологии изготовления железобетонных шпал с целью повышения их качества и долговечности. В работе использова ны результаты многолетних научно-исследовательских, проект но-конструкторских и опытных работ, в том числе выполненных автором.
Автор выражает искреннюю признательность рецензентам книги — Д-ру техн. наук проф. А. Ф. Золотарскому, канд. техн. наук В. В. Серебренникову и инженерам Н. М. Исаеву и А. А. Балашову, замечания которых учтены при подготовке рукопи си к изданию.
Г л ав а 1
ОПЫТ ИЗГОТОВЛЕНИЯ ЖЕЛЕЗОБЕТОННЫХ ШПАЛ
1.Технические требования
Внастоящее время шпальные заводы выпускают главным образом предварительно напряженные железобетонные шпалы типа С-56-2 (рис. 1).
Для того чтобы оценить сложность задач по высококачест венному изготовлению предварительно напряженных железо бетонных шпал, рассмотрим основные технические требования, которые к ним предъявляются действующим ГОСТ 10629—71 [6[.
К шпалам предъявляются весьма высокие |
требования |
по |
прочности, морозостойкости бетона, точности |
расположения и |
|
натяжения арматуры и точности соблюдения |
заданных проек |
|
том конструктивных размеров. Требования к |
материалам |
для |
изготовления шпал (цемент, щебень, арматура) являются про изводными и вытекают из условий обеспечения требуемой проч
ности, морозостойкости бетона и трещиностойкости |
конструк |
|
ций в целом. |
установлены требования |
|
Поясним, из каких предпосылок |
||
к шпалам по ряду названных характеристик. |
качество |
|
П р о ч н о с т ь б е т о н а однозначно |
не определяет |
|
шпал, но от нее зависят многие их |
характеристики. |
Прежде |
всего высокая прочность бетона необходима, чтобы не произо шло разрушения подрельсовых площадок шпал от динамичес ких нагрузок подвижного состава. Напомним, что отечествен ные шпалы не имеют поперечной арматуры и хомутов, поэтому бетон должен обладать достаточной прочностью для предупре ждения появления продолных трещин и скалывания неармированных участков и углов.
Заанкеривание напряженной проволочной арматуры в же
лезобетонных шпалах происходит исключительно за |
счет сил |
|
сцепления арматуры с бетоном. |
восстано |
|
При спуске натяжения арматуры она стремится |
||
вить свой первоначальный диаметр, чему препятствует |
бетон. |
|
В результате на анкерных участках в торцах шпал |
возникает |
|
расклинивающий эффект от арматуры, приводящий |
к |
образо |
ванию в бетоне растягивающих напряжений и нередко микро трещин. При отсутствии плавного спуска, например при обруб ке проволок, расклинивающий эффект вследствие удара воз-
Э
1993
192
---------------------------J ------------
. . . . .1 | Ь . г |, ,1 |1 . . . ■ ■ ■ - |
^4 , |
2700
Рис. 1. Шпала типа С-56-2
растает в несколько раз, поэтому вероятность образования, микротрещин в торцовых участках шпал возрастает.
От прочности бетона зависит длина анкерных участков ар матуры. Поскольку величина продольного обжатия бетона воз растает в зоне анкеровки арматуры от нуля до заданной вели чины, то необходимо стремиться к уменьшению длин анкерных
участков, так как растягивающие напряжения |
в бетоне |
от |
внешней нагрузки также возрастают от торца |
шпалы до |
мак |
симума в середине шпалы под осью рельса |
(около 50 см от |
|
торца). |
|
|
Если растягивающие напряжения в бетоне от поездной на грузки будут превышать напряжения его обжатия плюс сопро тивление разрыву, то неизбежно появление трещин. С возрас танием диаметра арматуры при равной прочности бетона уве личивается необходимая длина зоны анкеровки проволок.
Исходя из этих условий ГОСТ устанавливает марочную прочность бетона (>500 кгс/см2) и прочность бетона в шпалах к моменту спуска натяжения арматуры (>350 кгс/см2). Оба эти ограничения по минимальной прочности бетона имеют боль шое значение для обеспечения долговечной работы шпал в пути.
М о р о з о с т о й к о с т ь б е т о н а определяет морозостой кость шпал, однако отождествлять эти два понятия не следует. ГОСТом на шпалы предусмотрены испытания бетона на моро зостойкость лишь в образцах-кубах.
Наиболее обширные по своим масштабам (120 шпал) опыты по определению морозостойкости самих железобетонных шпал были проведены С. В. Шестоперовым [3] на полигоне Широковской ГЭС в ее нижнем бьефе. Эти опыты выявили харак терные виды разрушений шпал при их попеременном замора-
6
живании и оттаивании. Разрушение железобетонных шпал е проволочной арматурой диаметром 2,6—3 мм, как правило, на чиналось с торцов и боковых граней, причем в одной и той же шпале иногда один торец разрушался, а другой оставался це лым. Отмечены случаи локальных разрушений бетона от во ды и мороза.
Причинами разрушения торцов являются микротрещины в бетоне, образующиеся на анкерных участках арматуры, и не достаточное уплотнение бетона на концевых участках шпал в результате вытекания части цементного молока из опалубки через диафрагмы. Разрушение бетона в торцах шпал начина лось с появления сетки видимых трещин над арматурой, кото рые с увеличением числа циклов замораживания и оттаива ния как бы прорастали по направлению к подрельсовым пло щадкам.
Таким образом, во всех случаях наблюдалось постепенное разрушение торцов шпал, что может быть объяснено пере мещением зоны анкеровки арматуры по мере ослабления проч
ности бетона |
с увеличением числа циклов его замораживания |
|
и оттаивания. |
пери |
|
Локальный характер разрушения бетона по длине и |
||
метру шпал |
объясняется его неоднородным уплотнением |
при |
формовании |
изделий. Часть шпал разрушилась с боковых |
по |
верхностей по защитному слою бетона. Морозостойкость конт рольных кубов, изготовленных из того же бетона, что и шпалы, почти во всех случаях оказалась намного выше, чем самих шпал.
Кроме сказанного, следует учитывать, что шпалы при экс плуатации в пути испытывают значительные динамические на грузки, которые приводят к образованию сложных напряжен ных полей в бетоне конструкций. Исследованиями О. П. Мчед- лова-Петросяна и его сотрудников [7] установлено, что в ре зультате этих напряжений в бетоне повышается общая трещи новатость. Трещины возникают в зоне контакта заполнителя с
цементным |
камнем, а |
иногда переходят даже в зерна заполните |
ля. Все это |
приводит |
к постепенному разрушению структуры |
бетона, что на первых стадиях почти не улавливается при его испытаниях на сжатие. В то же время предел прочности тако го бетона при растяжении и изгибе изменяется в значитель ных пределах, что свидетельствует о развитии в нем процессов старения. Естественно, что замораживание и оттаивание тако го бетона при насыщении водой будут способствовать интенси фикации процессов деструкции и более быстрому его разру шению.
С. В. Шестоперов [3] на основе проведенных опытов при шел к выводу, что вполне возможно решить задачу изготовле ния долговечных шпал (способных работать в течение 100 лет и более) из предварительно напряженного бетона, которые мо-
7
гут выдержать более 400 циклов замораживания. Заметим, что этот вывод относится к шпалам, сформованным при вертикаль но направленной объемной гармонической вибрации из жестких бетонных смесей при содержании цемента не более 450 кг/м3 и при расходе воды не более 140—150 л/м3.
М. Ф. Вериго и В. В. Серебренников [4] в результате ла бораторных испытаний на пульсаторе установили, что железо бетонные шпалы с проволочной арматурой обладают достаточ но высокой выносливостью. Комплексные испытания, прибли женные к условиям эксплуатации шпал, т. е. одновременно на морозостойкость и выносливость, из-за сложной методики опы та пока не проводились.
В целом морозостойкость бетона зависит от многих факто ров: прочности, состава цемента и бетона, водо-цементного от ношения, качества уплотнения, плотности, условий твердения бетона, длительности его выдержки до замораживания, степе ни насыщения водой, величин перепадов температур при замо раживании и оттаивании и т. п.
Из этого неполного перечня факторов видно, что один и тот же по составу бетон при изменении параметров технологии и условий испытаний может обладать различной морозостой костью.
Точных методов расчета марки бетона по морозостойкости пока не создано, но накоплено большое количество опытных данных, на основе которых ГОСТом определены общие требо вания, выполнение которых гарантирует получение бетонов вы сокой морозостойкости.
А р м а т у р а для шпал предусмотрена из стальной проволо ки периодического профиля по ГОСТ 8480—63 диаметром 3 мм. Допускается применение арматуры диаметром 4 и 5 мм.
Проволоку периодического профиля получают из гладкой проволоки путем образования вмятин, очерченных по цилинд рической поверхности и расположенных с двух взаимно проти воположных сторон. Количество таких вмятин на участке длиной 100 мм для проволоки диаметром 3—4 мм должно быть не менее 15 пар.
Проволока периодического профиля (табл. 1) имеет предел прочности на 5—6% ниже, чем исходная гладкая. Например, гладкая проволока диаметром 3 мм имеет предел прочности 190 кгс/мм2, а периодического профиля 180 кгс/мм2. Вмятины увеличивают сцепление арматуры с бетоном, что, как указано выше, является одним из важных условий надежной работы шпал.
Большое значение имеет однородность упругих свойств проволоки. От модуля упругости при прочих равных условиях зависит равномерность напряжений в арматуре при ее группо вом натяжении. Модуль упругости не регламентирован
8
Т а б л и ц а 1
Основные технические характеристики проволоки периодического профиля
|
|
|
|
|
Диаметр проволоки, |
мм |
Наименование характеристик |
3 |
4 |
5 |
|||
|
|
|
|
|||
Расчетная площадь сечения, мм2 |
7,06 |
12,56 |
19,63 |
|||
Глубина вмятин, |
мм |
разрыву |
0,15 |
0,119 |
0,24 |
|
Временное |
сопротивление |
160 |
170 |
160 |
||
(браковочный минимум), кгс/мм2 |
144 |
136 |
,128 |
|||
Условный предел текучести, кгс/мм2 |
||||||
Относительное |
удлинение |
после |
4 |
5 |
6 |
|
разрыва |
на |
расчетной |
длине |
|
|
|
100 мм, |
% |
|
|
4 |
3 |
3 |
Число перегибов на 180° при диа- |
||||||
метре валиков 30 мм |
|
|
|
|
ГОСТом; по данным многочисленных испытаний он может ко лебаться в пределах (1,8—2,1) 106 кгс/см2.
Число перегибов характеризуют пластические свойства про волоки, не всегда одинаковые для различных партий и даже по длине бухты. Самым распространенным дефектом для некото рых партий проволоки является ее расслоение по продольной оси, что приводит к частым обрывам при натяжении армату ры. Опасны также закаты, окалины, местные повреждения и т. п.
Лучшее сцепление арматуры периодического профиля с бе тоном по сравнению с гладкой обеспечивается образованием шпонок в местах вмятин и наличием бочкообразных участков на самой проволоке, возникающих в результате ее сплющива ния при нанесении вмятин.
Иногда для улучшения сцепления с бетоном прибегают к волнированию гладкой проволоки (см. опыт Венгерской На родной Республики).
Величина предварительного напряжения арматуры должна быть не менее 65% браковочного минимума, указанного в табл. 1.
Допускается кратковременная перетяжка до 75% для умень шения потерь от релаксации и ползучести.
Т р е щ и н о с т о й к о с т ь |
является важной качественной ха |
рактеристикой шпал. При |
расчете шпал исходят из условия, |
что в процессе работы под действием поездной нагрузки в бе тоне растянутых зон не должно возникать трещин. Под дейст вием сосредоточенных поездных нагрузок в шпале, опираю
щейся подошвой на балласт, возникают положительные изги бающие моменты в подрельсовых частях и отрицательный мо-
9